Sustainability
What's New
Latest News
結果: 456
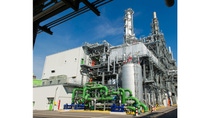
BASF launches aroma ingredients with reduced Product Carbon Footprints to enable customers reach their sustainability targets
Ludwigshafen, Germany – BASF Aroma Ingredients has successfully launched L-Menthol FCC rPCF as its first product with a reduced Product Carbon Footprint (rPCF). Further rPCF product launches are planned to help customers achieve their ambitious Scope 3 carbon reduction targets. BASF's rPCF aroma ingredients come with a PCF reduction of about 10 to 15% compared to conventional BASF products.
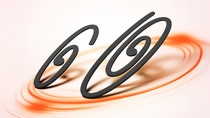
New possibilities for challenging E&E parts with specialty plastic Ultrason® D
For challenging E&E components, BASF has now developed the high-flow Ultrason® D 1010 G6 U40. The blend based on polyethersulfone (PESU) is optimized to meet special needs for easy injection molding of energy-efficient parts in data and energy transmission, smart electronics and e-mobility. Because of its excellent flowability at lower processing temperatures the new BASF thermoplastic gives manufacturers greater flexibility when designing sophisticated switches, circuit breakers and sensors as well as IGBTs and semi-conductor parts like burn-in test sockets. Ultrason® D 1010 G6 U40 shows stable electrical properties at elevated temperatures with a high relative thermal index (RTI) and a higher comparative tracking index (CTI) than polyetherimide (PEI) and polyphenylenesulfide (PPS).
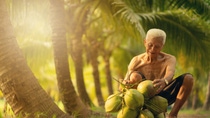
BASF’s Care Chemicals division publishes its Responsible Sourcing Report for 2024
Ludwigshafen, Germany, March 31, 2025 – BASF’s Care Chemicals operating division today released the third edition of its Responsible Sourcing Report (RSR). The report shows the division’s progress in 2024 in the three pillars of sustainability – economy, environment and society. At the same time, it underscores BASF’s commitment to sustainability, demonstrating the company’s dedication to supporting smallholder farmers and promoting sustainable practices. BASF’s comprehensive sustainability statement can be found in the company’s Annual Report 2024.
A Vision for Collective Action – BASF Coatings’ Sustainability Future Target Picture
As a leading supplier of global surface solutions with a clear vision for the future, BASF Coatings is implementing its Sustainability Future Target Picture. This target picture represents an important cornerstone of the company’s commitment to sustainability and innovation. The visionary framework is designed to inspire optimism and collective action among stakeholders, emphasizing that small, individual contributions can collectively create a significant impact on our future.
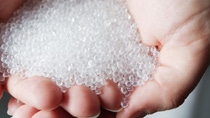
BASF receives Operation Clean Sweep® certification at all its European production sites for plastic pellets
All BASF's European production sites for engineering plastics, polystyrene, expandable polystyrene, polyurethane, thermoplastics polyurethanes, polyamides and specialty polymers are now certified by independent third parties according to the Operation Clean Sweep ® (OCS) standard. "With the successful certification of the polyamide production in Antwerp, the final milestone of this important project has been reached. We are delighted with this great achievement together with all teams involved in the proper handling of plastic pellets," says Sophie Van Dyck, Vice President Operations Polyamides & Precursors Antwerp. In total, 16 production plants for plastic pellets were certified at six BASF production sites in Europe.