Sustainability
BASF plastic additives protect sports shoe soles from prematurely biting the dust
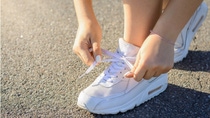
Over the years, the footwear industry has experimented with various materials in its quest for the best sole material for sports shoes. While a plethora of materials exhibited exceptional results in specific criteria, there was one material that stood out of the crowd when it comes to holistic performance – Thermoplastic Polyurethane (TPU).
Soles from TPU are obtained by injection molding at high temperature under pressure. TPU is considered the ‘all-rounder’ of soles and the most commonly used. It is sturdy, abrasion resistant and flexible.
However, TPU is UV-sensitive, and without light stabilizers, TPU soles will turn a hideous shade of yellow.
Additionally, soles made of TPU must withstand degradation caused by oxygen, humidity, intense sunlight, and high temperatures. Degradation can lead to significant changes in the polymer mechanical properties, surface chemistry, and structure, leading to embrittlement and cracking. Basically, the soles can fall apart. It turns out Earth is an extremely hostile environment for TPU material.
That's right, the three things that make human life possible – air, water and sunlight – can kill your beloved sneakers.
To prevent TPU degradation, Tinuvin® PUR 866, a UV light stabilizer, has been used by customers in Taiwan, China and India, to achieve the quality results required by the high-end sports shoe brands.
Unlike many other light stabilizers, BASF’s Tinuvin® PUR 866 does not affect the initial color of TPU after compounding. Additionally, by reducing discoloration, it allows TPU products to maintain their visual appeal, and thus protect the product’s brand.
A UV light stabilizer is critical to the final product. Even at a lower dosage level Tinuvin® provides weathering resistance and long-term strength. In this way it extends the useful lifetime of sport shoes and saves natural resources and contributes to sustainability.
“The unique properties of TPU allows the finished material, such as shoe soles, to be made rigid or flexible, highly elastic or with good shock absorbing properties, and with varying degrees of thermal stability and abrasion resistance,” said Hermann Althoff, BASF’s Senior Vice President, Performance Chemicals Asia Pacific. “With a stabilization technology based on the Tinuvin® light stabilizer solution, our customers are able to make a more durable TPU shoe sole.”
BASF conducts intensive research in its laboratories to stabilize plastics against UV radiation. Application testing takes place in specially equipped laboratories and application centers. The knowledge gained in this process flows directly into the development of novel light stabilizer solutions.
The performance of Tinuvin® is also tested under simulated environmental conditions in accelerated weathering devices according to the requirements of ISO 4892-2:2013. This international standard specifies the methods for exposing specimens to xenon-arc light in the presence of moisture to reproduce the weathering effects (temperature and humidity) that occur when polymers are exposed in actual end-use environments to sunlight. Based on the data obtained from accelerated weathering, the durability to be expected for polymers in the different applications will be estimated.