Media
The endurance runner
BASF researchers revolutionized running shoes ten years ago with the Infinergy® foam: The first expanded thermoplastic polyurethane is built into the midsole and returns part of the energy used to the runner, who can thus increase his performance. Today, a wide range of companies swear by the durable foam, which is also going to play a pioneering role when it comes to sustainability.
Around 10,500 kilometers, a heat wave, stormy headwinds and thunderous storms lie behind extreme athlete Jonas Deichmann when he reaches New York at the beginning of November – welcomed by his fans. He has crossed the U.S. twice in a row by bike and on foot, first from the East to the West Coast, then back again. During his TRANS AMERICA TWICE Tour, his bicycle saddle played a supporting role, as the 36-year-old world record holder in the ultralong distance explains. "With these enormous distances, the saddle is extremely important: If you have the wrong one, it'll become very painful." What makes it special: The core of his saddle is made of Infinergy® foam, which makes a completely new riding experience possible. It minimizes seat pressure, absorbs road shocks and vibrations, and is particularly gentle on the back. This is a major advantage when the route leads over gravel roads or bumpy ground, which can hardly be avoided on extreme tours. What Deichmann appreciates about Infinergy is that it makes the saddle so "comfortable and very light."
Small beads with great potential
Runners have long since discovered Infinergy for themselves. In the past, they had to choose between hard competition shoes or very soft, highly cushioning training shoes. That changed when adidas and BASF jointly developed the Boost model ten years ago, to which the Infinergy sole gave completely new spring and cushioning properties. "This allowed us to find the ideal balance between lightness and stability of the shoe," says Martin Vallo, Head of Tech Development Infinergy at BASF Polyurethanes GmbH. The runner experienced an energy return that no other shoe could offer. This is thanks to an expanded thermoplastic polyurethane, or E-TPU for short. To produce E-TPU, BASF employees foam up TPU granules, heat them and subject them to pressure. They then let the granules blow up like popcorn. This increases their volume tenfold, creating oval foam beads with tiny, closed gas bubbles inside that provide the elasticity and the so-called rebound effect. This makes it possible to return up to 75 percent of the energy to the runner.
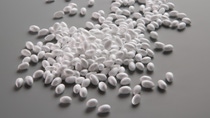
2023 saw the launch of the Ultraboost Light, adidas' lightest Boost shoe to date. The midsole weighs 30 percent less than the first-generation Boost while providing optimal spring and cushioning properties.
This also convinced event manager and passionate athlete Teresa Hermann, who ran the Palma Marathon on Mallorca with the adidas Ultraboost in mid-October. "I love running, it gives me a sense of freedom," she explains. "Plus, it clears your head and you can just start virtually anytime, anywhere." For that, she says, it takes nothing more than the right clothes and the right shoes. "Everyone has slightly different requirements there, but good cushioning is a must," she thinks. What she appreciates about the Ultraboost, besides its lightness, is the special feeling due to the rebound effect. "The material feels dynamic and you feel a lot of energy when jogging."
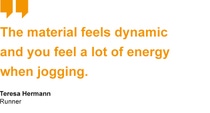
Comfortable? For sure!
This not only benefits athletes. The foam has also proven its worth in work and safety shoes. On the one hand, they have to be resistant to impacts or liquids, but on the other hand they also have to be comfortable. After all, they are often worn for quite a number of kilometers a day. Shoe manufacturer Elten in Uedem in the Lower Rhine region uses Infinergy for its Wellmaxx series. "If employees wear the wrong safety shoes at work, sooner or later this will lead to pain," explains Nadine Claaßen, master orthopedic shoemaker at Elten. "That's why we wanted to develop a shoe that combines foot protection with wearing comfort. Infinergy has opened up completely new possibilities for us here. Thanks to the special cushioning, ligaments and joints are subjected to significantly less stress than in other safety shoes. In addition, the lightweight material and the spring ensure that the wearer uses less energy when walking."
For BASF foam expert Martin Vallo, there is still plenty of potential in the material: "It can be used wherever the combination of low weight, extraordinary mechanical properties and high long-term durability in a wide temperature range is required." By now, Infinergy can be found in sports field and playground surfaces, bicycle inner tubes and tennis rackets, among other things.
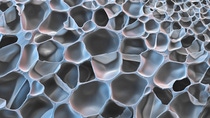
The future is circular
BASF researchers also have big plans for Infinergy. "The future of footwear is circular," says Lionel Gehringer, Senior Manager Sustainability Projects Infinergy at BASF. "That's why we've launched a comprehensive circular economy program and are aiming for carbon-free production by 2050." Already today, Infinergy can be recycled, less and less waste is generated during production, and less and less fossil energy is needed. Alternative raw materials are also employed: Instead of natural gas, for example, biogas is used to reduce the Product Carbon Footprint. A biomass balance approach, which has been audited by independent examiners, assigns the share of renewable raw materials to the respective products.
Alternatively, fossil raw materials can also be replaced by pyrolysis oil. To obtain this, plastic waste such as used tires – which up to now could not be reused – is chemically recycled. In this process, the bonds in large molecules are broken by high temperatures and smaller molecules are created from which new products can be manufactured. This raw material is also allocated to the material using the mass balance approach.
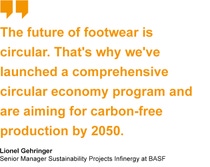
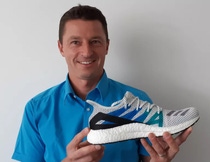
Infinergy is therefore being continuously developed. "It is also conceivable, for example, that new polymers will be used in the production process," says Martin Vallo. "Or highly durable coatings for the foam beads, for which automotive paints have been the inspiration." The beads themselves will be smaller and more compressed in the future. They are already versatile today. While they were initially only available in white, all colors are now possible. Here, too, BASF researchers are continuously looking for new, sustainable solutions. For brown shades, for example, coffee grounds have proven their worth as a dyeing agent. Black color comes from used tires, and turmeric provides a rich yellow. "Sometimes a solution is closer than you think," says Martin Vallo, but when it's not, perseverance and tenacity are needed from researchers. To motivate themselves, a look at the current bestseller by extreme athlete Jonas Deichmann, who is not easily deterred by any challenge, may help. He is convinced: "The limit is just me." His fans can look forward to see how and where he’ll prove it on his next tour.