Media
A new way of seeing our business
“At BASF, embracing the circular economy means not just rethinking materials and production processes, but also seeing our role in the value chain in a whole new light”, says Talke Schaffrannek.
“Moving to a circular economy means innovating not only our products but the whole way we see our business. For example, it means shifting from a model where we are paid for a product to a model where we are paid for performance – because this is one way to decouple growth from resource consumption.
But that’s not all. We are also contributing as early as the design stage of products, with innovations that mean products can be made with fewer materials, are longer-lasting, or easier to recycle. We are taking responsibility for our products from beginning to end and closing loops with organic, mechanical and chemical recycling. And we are replacing fossil raw materials with renewable or recycled raw materials, like pyrolysis oil derived from plastic waste or old tires, thus preventing incineration. To drive this transition, we are working on digital approaches to track materials, collect and sort them economically and bring them back into the value chain.
If there is one term that sums up what we need next, it is systems thinking. We are at the beginning of the shift to a circular economy. In every industry, we need to not only rethink our own business, but also rethink who we work with and how.”
Circularity by BASF
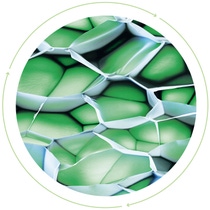
Renewable | Biomass balance approach
The biomass balance approach enables BASF to shift from fossil to renewable resources quickly because it works within existing value chains. Bio-naphtha and biogas derived from organic waste are used as feedstock in the first steps of chemical production.
The majority of BASF’s portfolio, including insulation and hygiene products, as well as plastic applications for many industries, can be produced with this approach. The bio-based feedstock amount is allocated to each product following a certified method.
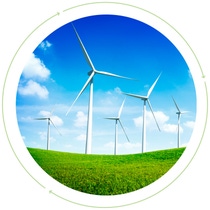
Reuse | Wind turbines
The blades of a wind turbine are usually made of a strong composite with reinforcing fibers that are hard to separate. This makes the blades difficult to repair or recycle.
As part of the E.U.-funded research consortium Vitrimat, BASF is working on a material that can be chemically weakened in a controlled way and then returned to a hard and stable state. This would allow it to be reused, reshaped, repaired or recycled.
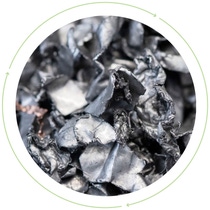
Recycling | Lithium-ion batteries
Over 1.5 million metric tons of battery cells from electric vehicles will have to be disposed of in the year 2030. These contain valuable resources such as lithium, cobalt and nickel.
BASF is investing in battery recycling so that these raw materials can be reclaimed and reprocessed, and is part of the industry-led Global Battery Alliance, which is driving sustainability across the entire value chain.
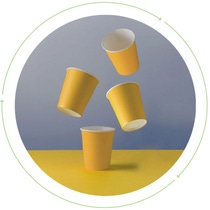
Reduce and recycle | Coffee cups
Food and drink packaging is often made of paper with a polymer film on it. Think of a takeaway coffee cup. The film makes the cup leak-proof, but because the two materials are bonded together, it is difficult to recycle. The two materials have to be separated and the polymer film disposed of. Some of the paper fibers are disposed of along with it.
BASF has developed Joncryl® HPB, a heat-sealable liquid polymer barrier that is water-based. It can be used by existing systems to make leak-proof packaging. In many locations, the packaging can easily be repulped after use and recycled.
Three recycling processes
From plastic waste to new products
Plastics do have proven benefits during their use phase – for example preservation of food loss in packaging applications, lightweight construction of vehicles, and building insulation. Plastic waste, however, has become a major global challenge. Globally, around 250 million metric tons of plastic waste are generated each year. Only around 20 percent of this plastic is recycled, thus keeping the material in circulation. Therefore, more plastic waste should be recycled overall. Solving this challenge and building a more circular economy for plastics requires innovation and joint efforts across the value chain. BASF will contribute to this by developing innovative technologies and products that promote the recycling of plastics.
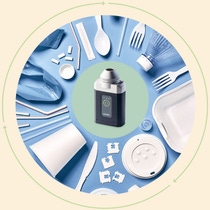
Mechanical recycling | Plastic sorting and PET recycling
Mechanical recycling is an important part of the circular economy. In North America, BASF makes Petra®, a thermoplastic polyester, out of post-consumer and post-industrial PET waste. For the process to work well, the material has to be all of one type. BASF subsidiary trinamiX provides a mobile, near-infrared spectroscopy solution that enables fast, on-the-spot identification of different types of plastics. Once sorted, they can be cleaned, shredded and reprocessed into new plastic products.
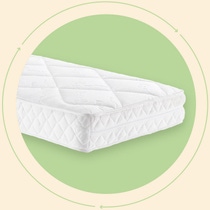
Depolymerization | Mattress recycling
What happens to old mattresses dumped at the curbside for collection as bulky waste? Often they end up in landfill or are incinerated. But through depolymerization the old polyurethane foam can be used to produce foam for new mattresses. BASF breaks down the material into its building blocks, the monomers, from which the polymers are rebuilt. Old mattresses provide the raw materials for the new ones, meaning fewer fossil resources are required.
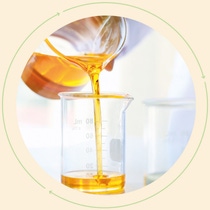
Pyrolysis | Waste-2-Chemicals
In Lagos, Nigeria, plastic waste often ends up on the streets or in the ocean. Waste-2-Chemicals is a project run by BASF Nigeria with social entrepreneurs who collect plastic waste. Through a thermochemical process, the plastic waste is turned into pyrolysis oil. The oil is similar to naphtha and can be used by the chemical industry as a feedstock to make new products that have the same properties as conventional products. Pyrolysis requires more energy than depolymerization but it recycles mixed plastic waste. It can also be resource-efficient: A small part of the waste is pyrolyzed into gas and used to generate the energy for the process. In Europe, BASF uses pyrolysis oil as feedstock in its ChemCycling™ project.