Sustainability
BASF Solutions for Reduced Greenhouse Gas Emissions
BASF Corporation’s Disclosure required under Division 26, Part 10 of California’s Health and Safety Code Section § 44475.2 (“California AB 1305” regarding “Voluntary carbon market disclosures”)
BASF Corporate Greenhouse Gas Commitments
We want to play an active and responsible role in shaping the transformation toward a climate-neutral society. The transformation of BASF towards climate neutrality is challenging. We are determined to take this path and become a pioneer in climate-neutral chemistry.
By 2030, we want to reduce greenhouse gas emissions from our production sites and our energy purchases (Scope 1 and 2) by 25% compared with 2018 – while growing production volumes in parallel. Compared with 1990, this would translate into a reduction of around 60%.
By 2030, BASF aims to reduce its specific Scope 3.1 emissions by 15% compared to 2022 across the portfolio – from 1.57 to 1.34 kilograms of CO2 per kilogram of raw material bought.
Our long-term ambition is net zero greenhouse gas emissions by 2050 (Scope 1, Scope 2 and Scope 3.1)
In working toward our Scope 3.1 target, we will focus on raw materials for those products for which our customers are prepared to pay for a lower carbon footprint.
To reduce our Scope 1 and 2 emissions, we are planning investments of around €4 billion between 2021 and 2030.
Progress toward these corporate commitments and our carbon management roadmap are detailed in BASF’s integrated Annual Report.
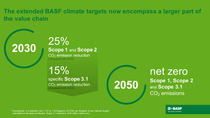
BASF Products with Reduced Carbon Footprint in North America
We offer our customers in North America a portfolio of products with significantly reduced product carbon footprints (PCFs) compared to standard products.
Product classes available in North America with selected examples:*
Product Class (Identifier) | Description | Specific Product Examples / Links |
LowPCF due to efficient production processes (LowPCF) | Products with PCF significantly below industry global average due to BASF’s integrated Verbund production set up and efficient production processes. |
|
Reduced PCF primarily due to the use of mass-balanced biogenic feedstock (BMBCert, LowPCF) | In the biomass balance approach: Instead of fossil feedstock (e.g., naphtha and natural gas), equivalent quantities of certified renewable (biogenic) feedstock are fed into the process at an early stage of production. One example feedstock is renewable natural gas. These sustainable attributes are then allocated to finished product using a certified mass balance methodology. |
BMBCert Biomass Balanced products are being marketed across BASF’s portfolio.
Selected examples include:
Lower carbon footprint certified Geraniol Extra BMBCert™
Adhesives and Coatings: LowPCF High Performance UV Acrylic Hotmelts CASE Monomer: 2-Octyl Acrylate Biomass Balanced Acronal® MB biomass balanced acrylic binders Acronal, Luphen® biomass balanced LowPCF product portfolio
Oppanol® BMBCert Polyisobutylene Glysantin® ECO BMB premium engine coolants Hydraulan® BMB premium brake fluids
Ultramid, Ultradur®, Ultraform®, Elastollan®, Elastopir®, and Elastocool® LowPCF
BMBCert Polyols and isocyanates
|
Zero PCF due to the use of mass-balanced biogenic feedstock plus renewable energy (ZeroPCF) | ZeroPCF products have a cradle-to-gate carbon footprint of zero, utilizing the biomass balance approach plus use of renewable energy and efficiency benefits of BASF integrated Verbund production. |
Adhesives and Coatings: ZeroPCF High Performance UV Acrylic Hotmelts
ZeroPCF Chemical Intermediates
|
Lower PCF due to the use of mass-balanced chemically recycled feedstock (Ccycled) | In the ChemCycling approach: Instead of fossil feedstock, feedstocks are derived from hard-to-recycle plastic waste materials such as end-of-life tires or mixed household waste. These sustainable attributes are then allocated to finished product using an certified mass balance methodology. |
|
Lower PCF due to mechanically recycled feedstock | Mechanically recycled feedstocks reduce the need for virgin fossil feedstocks and may reduce PCF |
Mechanically recycled polymers overview Examples: |
Lower PCF due to Roundtable on Sustainable Palm Oil (RSPO) Certified raw materials | BASF supplies a line of products utilizing RSPO-certified palm oil as a raw material. Due to improvement in forest conservation and harvesting practices, RSPO-certified palm oils have a lower PCF than products produced using non-certified oils. BASF supplies a line of products utilizing RSPO-certified palm oil as a raw material. | BASF Sustainable Palm Oil |
Other BASF solutions to reduce carbon footprint |
Solutions in various markets that BASF serves:
|
Circlestar™ Catalysts for reduced carbon footprint biobased ethylene Haptex® Polyurethane Synthetic Leather Home care ingredients for low temperature washing Solutions to promote mechanical recycling Sustainable surface solutions (lower carbon emissions coatings, surface treatments) |
*Not a guarantee of local availability, please contact your local BASF account manager for details. Please note that not all Specific Product Examples listed above are subject to the disclosure requirements of California AB 1305. Certain examples may only be included given the possibility of future claims made within the State.
Methodologies
Product (Identifier) | Methodology |
Product Carbon Footprints (PCF) for the entire BASF portfolio (SCOTT Methodology) |
The partial PCF is generally calculated using the digital application SCOTT, which determines the PCF for almost the entire BASF portfolio and thus nearly 45,000 products. Primary and secondary data are used for the calculation. Secondary data are, for example, raw material data from commercial databases.
The methodology for calculating the PCF is based on the ISO 14040, ISO 14044 and ISO 14067 standards and is compliant with the Greenhouse Gas Protocol Product Standard. The partial Product Carbon Footprint takes into account the greenhouse gas emissions that occur when raw materials are extracted (cradle) until they leave the BASF site (plant gate). The consideration from the cradle to the factory gate (cradle-to-gate) thus only covers part of the product’s life cycle, not a complete life cycle analysis (cradle-to-grave).
A methodology review carried out by TÜV Rheinland Energy GmbH has certified that the PCF methodology SCOTT (Strategic CO2 Transparency Tool) that was developed and is used by BASF for calculating the PCFs of BASF products complies with ISO 14067:2018 and reflects the state of the art.
|
Life Cycle Analysis (LCA) | Where required to validate product carbon footprint reduction claims, BASF employs Life Cycle Analysis (LCA). BASF established this holistic method in 1996 and was one of the first companies in the chemical industry to do so. The Eco-Efficiency Analysis was most recently validated by NSF International in 2016 and in the NSF (USA) in 2019. The Eco-Efficiency Analysis follows ISO 14040:2006 and 14044:2006 for environmental life cycle assessments. The assessment of life cycle costs and aggregation to an overall Eco-Efficiency is based on ISO 14045:2012. |
LowPCF due to efficient production processes (LowPCF) |
To identify the products with a low product carbon footprint (PCF) we have calculated the individual PCFs of BASF’s products using the SCOTT methodology above. We then compared the results with assessments of market-wide average carbon footprints of the corresponding products of third parties (all produced from fossil-based raw materials). A significant PCF reduction of greater than 20% is required to make a lowPCF claim for this class of products; in many cases 30% or greater reductions are seen.
BASF has made the assessments of corresponding third-party products using publicly available information and fee-based, proprietary market survey data on production routes and deployed raw materials, to the extent available, as well as BASF’s own market and technology know-how. The data assumptions and allocation factors for third-party PCFs are the same as for the calculation of the PCF of the BASF product, as applicable.
For the determination of PCF reduction for Chemical Intermediates, BASF’s assessments of the PCFs of the corresponding third-party products have not been subject to an LCA critical review by an independent third party.
To identify the PCF of BASF ibuprofen products versus industry average, a third-party LCA by Ecovamed was carried out. (Link)
To determine that the embodied carbon (PCF) of Neopor GPS insulation is lower than competitors, an LCA was carried out to determine Neopor GPS embodied carbon. (Link to Environmental Product Declaration (EPD)). This was then compared to competitive technologies using publicly available EPDs in the Embodied Carbon in Construction calculator tool (EC3) (link) |
Reduced PCF or Zero PCF primarily due to the use of mass-balanced biogenic feedstock (biomass balanced BMBCert, LowPCF, ZeroPCF) |
BASF has established a closed chain of custody from the renewable feedstock it uses through to the final product. An independent certification confirms that BASF has replaced the required quantities of fossil resources for the biomass balanced product with renewable feedstock. BASF’s biomass-balanced products are certified according to either the Redcert2 or the ISCC Plus certification scheme.
Reductions in Product Carbon Footprint due to biogenic carbon uptake are accounted separately and are carried out in accordance with BASF SCOTT methodology.
Ellen MacArthur Biomass Balance Methodology Whitepaper (co-written with BASF) ZeroPCF Intermediates certified carbon neutral by Carbon Trust ZeroPCF Lupranat Zero certified by TUV Nord
|
Lower PCF due to the use of mass balanced chemically recycled feedstock (Ccycled) |
Products with mass-balanced chemically recycled raw materials may have lower PCF in some cases dependent upon the baseline comparison. For an overview of BASF-sponsored global LCA studies please see the following link. |
Lower PCF due to Mechanically recycled feedstock | Mechanically recycled feedstocks reduce the need for virgin fossil feedstocks and may reduce PCF. This is determined on a product-by-product basis in BASF SCOTT tool. (Please see SCOTT methodology above). The reduction in PCF due to mechanically recycled raw materials is determined relative to the closest-performing conventionally sourced product where applicable. |
Lower PCF due to Roundtable on Sustainable Palm Oil (RSPO) Certified raw materials | An LCA carried out by a third party showed approximate 35% reduction in the PCF of RSPO-certified palm oil versus standard supply chains. BASF supplies a line of products utilizing RSPO-certified palm oil as a raw material. Certified Palm Oil Club - 2.-0 LCA consultants (lca-net.com) |
Other BASF solutions to reduce carbon footprint | Determined on a case-by-case basis using BASF LCA or SCOTT methodologies. |
This website is intended to provide information in response to document compliance with California Law AB 1305.