Media
Hydrometallurgy: A more sustainable solution to extracting metals in mining
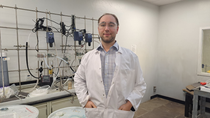
Born in Bavaria, Germany, Julius Heidlas relocated to the United States at age 11 with his parents and siblings. He studied chemistry at the University of Houston, where he also completed a Ph.D. in organometallic chemistry.
Julius is one of the most recent additions to the Mining Solutions team, bringing a wealth of knowledge in the field of hydrometallurgy. He joined BASF in 2021 and works as a hydrometallurgical chemist. Learn more about the exciting field of hydrometallurgy, the challenges and opportunities this field brings and more below.
What is hydrometallurgy?
Hydrometallurgy is a method of processing metals via aqueous solutions. Hydrometallurgical processes all share the characteristic of having the metal dissolved in water, but each process is tailored to the materials. Therefore, they don’t necessarily resemble each other beyond that aspect.
In many cases, hydrometallurgy is the only way a particular metal can be converted from the host rock to a form that can be used by consumers. This method of processing ores is relatively new, with the copper-based process being around 50 years old. All aluminum is made today using the Bayer process, a hydrometallurgical process. Approximately 20% of copper is made hydrometallurgically. Battery and e-waste recycling is done hydrometallurgically as well.
The process varies from metal to metal. It depends on what metal you extract and the ore or host rock. For example, copper requires a very dilute sulfuric acid solution to wash the rocks and leach the copper. For nickel, an ammonia solution might be needed. And with uranium, it can also be an acid or a carbonate solution. It’s usually a relatively dilute solution for washing large amounts of ore or, sometimes, a more concentrated solution for more concentrated feedstocks.
What does a hydrometallurgical chemist at BASF do?
I’m privileged to have an incredible cross-section of topics in my work. I get to view many aspects of production, including quality control process improvements, problems in the process, and everything to do with getting the material delivered to the customer.
I also get to work with customers in the analysis of their plant data, assess how the extraction process is running on their end, and all the sorts of problems and nuances that appear. Every one of these extraction plants is unique, just as every mine and every ore body, and we try to work closely with our customers to keep everything running optimally.
We also conduct research and development, so we always try to develop new products that fill a particular customer need. It’s an incredibly varied job.
For me, the best part of the job is collaboration. Our Global Center of Excellence is based in Tucson, Arizona, but we have an incredible international team represented on every continent. We collaborate on many different matters: customer processes, production, and various challenges and opportunities on any given day.
What are the biggest challenges and opportunities your position offers today?
The biggest challenge is keeping a clear overview of everything we are simultaneously managing. We have a lot of different projects and many different fields, so keeping everything in mind can be challenging sometimes. Inversely, all the industry's challenges can offer great opportunities on our end. We look for organic molecules that can affect change in a large amount of inorganic metal-bearing material. If we can solve any of these huge industry problems, we have a great business opportunity.
Currently, there's a big focus on products that improve leaching kinetics by various means, for instance, by improving the wetting of the ore or by improving the rate at which particular minerals dissolve to improve hydrometallurgical recoveries.
Flotation is a recovery process commonly used for sulfidic minerals, in which the ore is finely ground and separated from the gangue by selectively attaching air bubbles, causing the desired material to float. The industry is challenging companies to move more material from the flotation side into a hydrometallurgical space.
For example, when it comes to copper, the leaching of chalcopyrite is one of the most recognized problems for which the industry is seeking a solution. Chalcopyrite is currently produced using a more energy-intensive flotation process. The industry has long tried to move it from the flotation to the hydrometallurgical space because it costs less and has environmental advantages. There are many interesting approaches to this challenge, but if our contribution has the potential to assist a customer, it would be a significant accomplishment.
Why is mining and metal extraction becoming such a driving force today?
The concentrations of mineral deposits are decreasing. Yet, metal production will have to radically increase over the next decades to meet increased global demand. There are two prevailing trends that are overall very positive: the global middle class is growing every year, and a middle-class lifestyle requires large amounts of metals. The other is electrification and electromobility. Electricity is transmitted through copper wires, and electric vehicles, as well as electronic devices such as cell phones, require batteries. So, all these new green technologies require significantly larger amounts of metals than the carbon-intensive technologies they're replacing.
Simultaneously, mining and metal production needs to become more sustainable. So really the only way to meet any or all of these challenges is by introducing new technologies. The mining industry has widely recognized this and they're really pushing to bring these new technologies into the field.
What makes hydrometallurgy a more sustainable process compared to the more traditional methods?
Hydrometallurgy must be assessed for every mineral, mine, etc., but a few key attributes give hydrometallurgy an advantage. The first is that the ore doesn't have to be very finely ground as it does for flotation. This process is very energy-intensive and can be eliminated using hydrometallurgical methods.
Concentrates produced via flotation, and sometimes processed hydrometallurgically, are generally smelted to produce metal. The high temperatures needed for smelting are energy and usually carbon-intensive. Smelting also comes with significant emissions concerns. Hydrometallurgy can often recover metals at relatively low temperatures using electricity, a potentially more carbon-friendly energy source.
The third advantage is that hydrometallurgy can have a superior circularity to other processes. Materials that leave the hydrometallurgical cycle, particularly acidified water, can often be immediately reused. One would expect a hydrometallurgical process to use a lot of water compared to the amount of metal produced, but it is significantly lower in many cases compared to flotation and other processing methods.
For questions, please contact mariana.licio@basf.com.
For media inquiries, please contact molly.birman@basf.com