Media
BASF helps create a one-of-a-kind floating solar panel system
In less than 12 months of close collaboration, BASF and Noria Energy developed an entirely new floating solar pontoon racking system and installed the first pilot in BASF’s McIntosh, Alabama site, achieving great results.
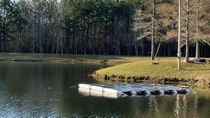
The pilot is currently located in BASF's McIntosh, Alabama site and will be extended to other larger BASF sites in the near future.
The renewable energy market in the United States has consistently been growing over the past decade. In fact, according to a 2021 report by the Environment America Research and Policy Center and Frontier Group, between 2011 and 2020, the proportion of electricity in the country generated by solar and wind power quadrupled.
Solar power in particular experienced accelerated growth of 23-fold during that timeframe.
In an effort to bring BASF closer to achieving its net zero goal by 2050, the Plastic Additives team reached out to Noria Energy, a renewable energy company, to find potential ways of collaborating.
After several months of exchanging information and ideas, they came up with a new concept and built a pilot installation at BASF’s McIntosh, Alabama site to test it, collect data and eventually scale it up.
Floating solar panels, a practical and efficient way of producing clean energy
Floating solar panels are quickly becoming a major contributor to the renewable energy market worldwide, mainly due to the number of benefits they offer when compared to conventional land-based solar systems. In fact, in Europe and Asia alone, there are over 3 gigawatts of floating solar projects already installed.
As James Raiford, Head of Technology Development of Noria, explains, “floating solar allows you to utilize existing bodies of water that are already serving a purpose and make them dual-use by adding energy generation at the site as well. In addition to that on-site renewable energy generation, floating solar has the benefit of improving the efficiency of the panels. It can also help with reducing evaporation and improving water quality, especially in the Western parts of the United States where droughts are a big issue.”
Aside from these benefits, by placing the solar panels closer to the water, the systems remain cooler, which in turn improves efficiency and energy production. Positioning them in bodies of water also helps reduce the growth of toxic algae. As Alex Mayer, Chief Technology and Growth Officer of Noria Energy, states, “floating solar allows us to add more megawatts of solar behind the meter to offset a site’s energy consumption, lower energy system costs and help them meet their climate goals.”
The floating solar array on water essentially comprises a floating structure that supports a network of solar panels. To get the energy back to shore, Noria uses different techniques, always making sure that they are safe and resistant to environmental conditions.
The systems are built taking into consideration the weather conditions of the area to make sure the array operates safely and produces maximum energy year-round. This includes anything from drought and snow to extreme weather phenomena, such as hurricanes, tropical storms, or typhoons.
The fruits of collaboration: from concept to installation
One of the key motivators behind Noria’s mission is “to reduce energy costs through the adoption of clean energy.” As part of these efforts, the company was looking to build pontoons that provided more flexibility and were cheaper and easier to transport and ship to different destinations.
As part of Noria’s efforts to make solar more accessible and visible, they wanted a floating solar system that would be easier and cheaper to ship, lowering costs. They needed a material that could withstand long-term water contact and sunlight exposure, and easily attached to the solar panel system. The solution BASF came up with provides structural rigidity but doesn’t deform over time and can last for 20 to 30 years without having to be replaced.
Joe Fay, Ph.D., and Senior Application Scientist in the Plastic Additives team at BASF, was one of the people who met with Noria to discuss the concept they had in mind, helping select the right material to meet their specific requirements and develop the pontoon. In his words, “they wanted to develop a system that was a flat-packed design, which required a more flexible material. So in dialogue with them, we were able to come down to one or two materials pretty quickly, and then it was a matter of looking at the availability of those materials in the marketplace for a pilot system, and we readily settled on thermoplastic polyolefin (TPO) as the material of choice for this initial project.”
To test the technology, BASF put Noria in touch with one of its customers and the pontoon system was produced, and the floating solar panel pontoon racking system was installed at BASF’s McIntosh site, where the plastic additives used in the pontoon are actually produced.
According to Mayer, “the pilot has been, so far, a large success. It’s producing energy, as it should, we’re collecting different data on the working pressure of the pontoons, the energy they produce and things like this, and so we’re going to feed that into our new design. Also, in doing this first pilot we found a few things that could be improved in the design that would otherwise not work at a large scale.”
What’s next for BASF and Noria’s relationship
The collaboration between Noria and BASF has, according to all involved, been extremely fruitful. And there is much more to come.
Neil DeLoggio, BASF’s Business Development Manager for Plastic Additives in the Americas – the person responsible for bringing together both companies explains: “Now that we have the installation and the proof of concept at McIntosh, they're working with our energy management team to look at installations at our Wyandotte site, that's also going to be a large-scale pilot for the Noria-specific design, which will be a hundred times the size of the pilot we have in place. We're also looking into our Geismar Verbund site, which currently can support a 5 MW system”.
There are many different aspects of floating solar that BASF can also help Noria develop, including construction of the systems themselves. The renewable energy company aims to reuse several of the materials with which they build the panels and racking systems, which is another angle they are currently exploring with BASF.
According to Raiford, “there is a lot of potential to expand on the initial collaboration that we started with BASF over the past year, specifically improving the products that we installed at the McIntosh site, scaling that out to a larger commercial system to demonstrate the ability of that product to impact at a larger scale, as well as exploring other ways of integrating BASF materials and plastics into floating solar installations in the future.”
Published on June 26, 2023 by Mariana Licio.
For media inquiries or to repurpose this article, please contact Lisa Brown.