Media
Sustainable construction—using fibers to extend service life of concrete
BASF offers an advanced alternative for concrete reinforcement.
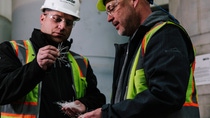
Those in the construction industry who are still using steel as a secondary reinforcement for concrete crack control—take heed—there’s another material on the block, and it's easier to manage, less expensive and safer.
That material is MasterFiber® from BASF’s Master Builders Solutions brand, a synthetic fiber that’s an advanced alternative concrete-reinforcement solution to traditional steel resulting in enhanced crack control and prolonged structure service life.
What makes these synthetic fibers a better reinforcement choice over traditional steel wire mesh and light-gauge steel bar? Made with a proprietary blend of polypropylene polymers, these reinforcement solutions reduce the amount of labor required to properly place secondary steel. In the construction industry where skilled labor shortages are becoming the new norm, fibers can help offset this industry-wide challenge.
MasterFiber reinforcement is integrally distributed throughout the concrete mixture, providing a three-dimensional reinforcement system. A fiber-reinforcement system ensures that the reinforcement is always in place for optimal concrete crack control.
“Steel is very cost prohibitive. It’s very labor-intensive to place and locate that steel correctly and appropriate alignment inside that concrete element that’s being placed,” said Dan Vojtko, Product Manager, Construction Chemicals, BASF. “With fibers being automatically distributed throughout that concrete mix, a lot of those challenges are virtually eliminated with the fiber-reinforced systems solution.”
Additionally, fibers provide flexural (bend strength) toughness and impact resistance, while controlling crack size proliferation. Controlled cracking reduces the ingress of water, a major contributor to the corrosion of steel. And since fibers, unlike steel, don’t corrode, this reduces the maintenance and repair cycles for concrete; hence, lowering the use-phase environmental footprint and costs to owners.
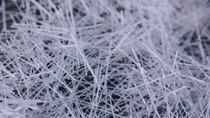
Also, in transporting fibers for a typical fiber-reinforced concrete application, the amount of fibers transported per truckload would require the steel equivalent of four to six times more trucks for the same amount of concrete placed with equal design requirements, according to David R. Green, Manager, Applied Sustainability, BASF.
“With the use of fibers, there’s less transportation, less jobsite or plant space needed to store reinforcement inventory and the concrete product arrives ready to place and finish without the prework required for placing welded wire,” said Green.
With all these benefits of synthetic fibers, one would wonder why the industry hasn’t made a more rapid change from steel? According to Green, there are engineering and code requirements that must be met to support utilizing fiber reinforcement. Project success and further education will drive advancements in that arena. Supplementing steel reinforcement with a lower life-cycle-cost alternative of fibers is the innovative solution for sustainable construction.
Precast elements such as manholes, septic tanks, burial vaults and flared ends are especially difficult to reinforce with steel. By eliminating the amount of steel required for each project, MasterFiber products can increase production efficiency by 28%, according to BASF data.
One such customer—Forterra—a Denver-based utility precast company chose to use MasterFiber as an alternative to traditional steel reinforcement.
“[Our] company decided to try out MasterFiber, because it can be a huge time-saver in some of our production methods as well as cutting cost compared to some of the other methods that we’ve used, such as steel reinforcing the product,” said Corey Cooper, Production Manager, Denver Precast, Forterra.
MasterFiber reinforcement solutions are said to be changing the game for everyday concrete construction. Production efficiency is greatly increased by integrating the secondary fiber reinforcement within fresh concrete– ultimately saving time and money, plus extending long-term concrete service life.
Published by Anna Spiewak & Calvinia Fields.
For media inquiries or to repurpose this article, contact Lisa Brown.