Media
Taking concrete to a higher level—space
BASF collaborates with NASA and Penn State on cement-hydration-in-zero-gravity study.
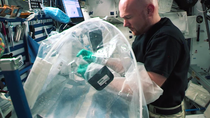
BASF and its products are known for taking concrete where it’s never gone before—and now they’re taking it all the way aboard the International Space Station (ISS).
BASF Construction Chemicals, North America, teamed up with NASA, CASIS and Penn State University—who’s leading the project called “ Microgravity Investigation of Cement Solidification”—to see what can be learned from cement hydration in space that will help make better concrete on Earth as well as in extraterrestrial environments—if structures might be needed on other planets in the future.
“If the moon or Mars were to be colonized in the future, it will require concrete (or a version of the concrete that we know today), because it could be produced using locally-available materials. Concrete would provide design flexibility because of its ability to be easily molded, and potential to be used in a 3D-printing process,” said Mark Bury, Product Manager, BASF. “In addition, the harsh environment of space may be problematic for any inhabitant, but concrete could be the solution by providing the needed protection from cosmic radiation, for example, in extraterrestrial structures.”
As a result, BASF provided two of its Master Builder Solutions brand products— MasterGlenium 7920 high-range, water-reducing admixture and MasterLife 300D crystalline capillary waterproofing admixture—to take a trip into space in an unmanned rocket on May 21, launched from NASA’s Wallops Flight Facility in Virginia, to meet with the ISS.
About 120 samples of water, cement and admixtures were sent into space —all in sealed clear plastic pouches with separate compartments to hold each material- and the ability to burst the seal connections so they can be mixed without leaving the pouch.
Astronauts used the unique environment of space to mix the concrete and permit scientists the ability to study and more fully understand the hydration reaction and microstructure of cement pastes. Considerations involved in mixing in microgravity included the fact that cement particles may not disperse very well and there is a certain amount of effort needed for proper mixing. To that end, MasterGlenium 7920 admixture was used to help disperse cement particles and provide an environment for easy mixing of the materials. Furthermore, BASF’s MasterLife 300D admixture facilitates the growth of crystals to fill voids in cracks within concrete to help keep it watertight. Therefore, crystal growth in zero gravity was of great interest to those involved in the experiment.
“Protein crystals grow larger in space and they’re more ideal in shape. Anything that grows in space tends to be more ideal—more as a physics theory than what we see as a practice on Earth,” said Aleksandra Radlinska, Ph.D., Assistant Professor, Civil and Environmental Engineering at Penn State, who is leading the research.
Radlinska spoke on the experiments at a BASF panel discussion in Cleveland, Ohio the day before the mixed concrete was expected to land back on Earth, Aug. 3, to be studied further by Penn State and NASA.
This was not the first time, however, that BASF products have made their way into space. Back in 1994, the company partnered with the University of Alabama in Huntsville and NASA to conduct a single concrete experiment—with the first chemical admixture MasterPolyHeed 997—on the Space Shuttle Endeavour, mission STS 68, to observe if concrete could indeed be mixed in zero gravity. The mixing equipment, at that time for just the one sample, was larger than all the 120 samples sent this time.
“[Back then] we didn’t know if you could even mix concrete (composed of powder and liquid ingredients) in space. Would these materials just be floating around within the mixing vessel, or would they actually combine together,” Bury added, “and if they did, would the concrete mixture get hard—we had many of these types of fundamental questions.”
BASF found out that concrete can, indeed, be mixed in zero gravity and to this day it is still the sole company to have its admixtures mixed into concrete in space. This time around, since admixture technology has changed greatly, BASF decided to provide its unique materials and consultation expertise to Penn State for the current-day experiment with concrete to further the research effort.
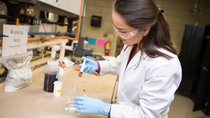
Another significant aspect of cement and concrete study in space was to see if they can be made more durable and sustainable, as buildings have the capability to make a major contribution to a more environmentally sustainable future for Planet Earth and beyond.
“Longevity of the built environment is always our prime objective—create structures that will be more durable, that’s right away implementing a sustainable solution,” said Radlinska in an interview with BASF.
“We have the tools and techniques to make concrete more durable. We just need to be able to translate that innovation through all the safety and scientific findings, so we can prove that this research is going to give us a more durable structure or infrastructure component,” she added.
Radlinska and her team (Richard Grugel, Ph.D. of Marshall Space Flight Center at NASA and Juliana Neves, graduate student at Penn State) ran tests on Earth parallel to the space experiments for a reference of comparison, even if it meant doing the experiments at all times of the night, sometimes at 4 a.m. Concrete samples received from space are currently being analyzed and the results will be shared once available.
Published by Anna Spiewak.
For media inquiries or to repurpose this article, please contact Lisa Brown.