Sustainability
Taking action in the plastic waste dilemma: Interview with Dirk Voeste
July 20, 2019
Despite the recent bad publicity that plastic waste has been getting—plastic is, in fact, our friend in terms of usage. From better living standards and health, to nutrition and convenience, plastics have provided many critical benefits to individuals and communities worldwide. Plastic is light, easily shaped, strong and inexpensive. Its ability to guard against contamination makes it useful in sterile medical environments such as hospitals, according to the Plastics Industry Association.
Nevertheless, our overdependence on the material is loading up the planet with single-use plastic waste. Worldwide, 1 million plastic drinking bottles are purchased every minute, while up to 5 trillion single-use plastic bags are used every year. This causes about 8 million tons of plastic to enter the world’s oceans from coastal regions every year, according to the Earth Day Network.
To combat this disposable-waste dilemma, 30 companies came together this year to form the Alliance to End Plastic Waste, a growing non-profit organization that has committed $1 billion, with a goal of investing $1.5 billion over the next five years to help end plastic waste in the environment. BASF is one of those companies as well as a cofounder of AEPW.
Many sustainability-focused companies, including BASF, recently gathered at the annual Sustainable Brands conference in Detroit for a discussion on sustainability including circular economic approaches in terms of plastic waste. At the conference, BASF’s former Head of Sustainability Strategy Dirk Voeste co-led a workshop on circular economy and presented BASF’s sustainability targets in his keynote. Read the interview with Dirk about the company’s measures to support circular economy.
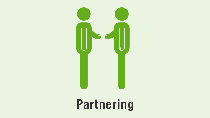

The demand for sustainable products is increasing. What kind of demands are you seeing from the market and from BASF customers?
Dirk Voeste: It’s not only a demand for more sustainable products but a demand for an additional societal value that products bring. Therefore, in whatever we produce and do as a company, we need to deliver a societal, ecological and economical value. Our sustainable solutions steering helps us drive innovation and make up a broad portfolio of sustainable products to satisfy our customers’ business needs. We also see that our customers commit to sustainability aspects like the recyclability of products, and we support them in their choices.
The past few years show a stronger trend towards recyclability of plastic packaging. What do you think is required to solve the issue of plastic waste and how can chemistry contribute to this?
Voeste: We benefit from plastic, be it in the field of medicine or food. There are many fields in which plastic innovations strongly enhance our living standard. The question is how we will use plastic in the future. We clearly want to maintain the benefits of plastic use and develop it further, but we also want to address the misuse of plastic. That’s why we joined the Alliance to End Plastic Waste. It’s our time now to tackle this problem actively, not only as a chemical company, but as an industry—it’s a whole value-chain approach: You need recyclers on board, you need waste collectors, you need the chemical industry and you need the customers and brands. And this is the first time that you see such a cross-value-chain’s strong commitment. Companies who have never worked together before now join forces to fight plastic waste. Chemistry plays the role of an enabler. We need to innovate in new ways for plastics to be used and re-used. Furthermore, we need to develop new plastics that will be easier to recycle or find ways to move plastic recycling forward, such as ChemCycling.
Let’s talk about ChemCycling. How does it work?
Voeste: In the ChemCycling process, plastic waste is turned into pyrolysis oil by our partners. The oil is fed into our Verbund system (into our chemical plants) as feedstock to generate new products. Up until now, the general option was mechanical recycling. Plastic bottles, for example made of thermoplastics, can be re-melted and re-molded. However, if there are products, such as a chocolate bar wrappers or mozzarella cheese packages, that consist of a multilayer of various materials, it is very difficult to disintegrate them. This kind of packaging often ends up in landfills, which I think is not an option at all, or are incinerated. ChemCycling fits exactly into that scenario: You find high-performing materials that cannot be disintegrated or mechanically recycled, and you bring them back into the system.
Could you talk about some of the challenges that you’re seeing with corporate circular economy initiatives?
Voeste: One of the challenges is making the right decisions — is it more eco-efficient to reuse old plastic material, to clean it, dry it, grind it and transport it or is it better to use newly generated pyrolysis oil (ChemCycling)? And from an eco-efficiency perspective, we often conclude that using oil with its intense energy rate and its high carbon rate is much more sustainable than reusing old materials. On the other hand, we know that our resources are limited, and we can’t continue like in the past. One of the main challenges as a result is—how we can introduce enough renewable material to start a circular approach.
Lastly, what does the future hold for BASF in terms of sustainability?
Voeste: BASF’s goal is to grow CO2-neutrally until 2030 – we want to be a leader in the chemical industry and to bring value to society. We really want to show that we’re not only talking the talk but also walking the walk and getting things done.