Who we are
Our research focus
We are a global leader in chemical industry R&D. With a more than 150-year history of innovation excellence, a broad global presence and knowledge Verbund, and a creative team of in-house experts and external partners, we drive innovative sustainable solutions, unleashing the potential of chemistry to solve some of the world's most pressing challenges. We create chemistry for a sustainable future.
Our researchers are working on many hundreds of research projects to meet the challenges of our customers:
Sustainable Food Supply

Solutions for better crop yields and nutrition
Crops are the basis for human food and to feed livestock, which play an increasing role in human nutrition habits globally. With more than 100 years of experience, BASF continues to research solutions that help farmers protect crops and ensure yields. Today, our scientists do research in many different areas including seeds, crop protection products and digital farming.
It is one of the most important tasks of our time to produce high-quality and safe food. Our products help to create personalized nutrition, making food healthier and more nutritious, such as by enriching it with vitamins. Either in classical chemical synthesis or by biochemical fermentation processes, our scientists work on even more sustainable ways of production and on formulations to meet the highest quality standards. At the same time, growing meat consumption worldwide requires high- performing animal farms and new approaches in animal nutrition. BASF researchers have many years of expertise in developing solutions for improved feed conversion and less greenhouse gas emissions. Currently, we focus on digital solutions that manage and optimize feed formulation while minimizing the environmental impact.
More about BASF’s research in agricultural solutions and digital farming, its efforts to improve human nutrition and animal nutrition.
Mobility of the Future
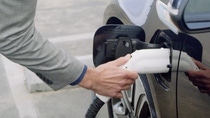
Research at the heart of an electric vehicle
BASF is researching cathode active materials (CAM), the key component of lithium-ion batteries in electric vehicles. With high energy density, safety and efficiency, our battery materials are the heart of e-cars. We set ourselves ambitious goals to further push e-mobility with our proven research know-how: by 2025, our innovations in battery materials aim to double the real driving range of midsized cars from 300 to 600 km (180 to 360 miles) on a single charge, while reducing the charging time to only 15 minutes, halving the size of batteries and doubling its lifetime. With these research goals, we strongly contribute to the success of future mobility to make it a practical reality for everyone.
Recycling of lithium-ion batteries
According to experts, more than 1.5 million metric tons of battery cells from electric vehicles will have to be disposed of in the year 2030. In addition, there is scrap from the production of cells and cathode active materials as well as their precursors. These contain valuable resources such as lithium, cobalt and nickel. With battery recycling, these raw materials can be reclaimed and reprocessed. To recycle lithium-ion batteries, they are first dismantled and shredded, which creates a substance called “black mass.” It is currently possible to recover raw materials from black mass using various chemical processes. This reduces the carbon footprint of the battery metals by at least 25 percent compared to mining from natural deposits.
Until now, however, this process has been very energy-intensive or has created large volumes of salts that require disposal. In addition, the yield of raw materials is still too low. BASF is developing a new highly efficient chemical process with numerous advantages: It can recover high-purity lithium from the batteries with high yields, it prevents waste and it further reduces the carbon footprint compared to existing processes. In this way, BASF supports the European Commission’s goals of establishing a sustainable European battery value chain. The BASF recycling process can play an important role in the creation of a circular economy for batteries in Europe. Learn more about lithium-ion battery recycling.
While battery materials are the heart of an electric vehicle, our researchers work on improving many more determining factors for sustainable mobility of the future. This ranges from the interior and exterior parts of a vehicle to the powertrain and chassis, all with the goal to make mobility cleaner, quieter, safer and more comfortable.
Have a look at our research in battery materials, an overview of our Automotive Solutions or discover all our products in our virtual car.
Circular Economy
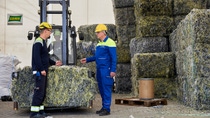
Turning waste into gold
The idea of a circular economy is to decouple growth from resource depletion by developing innovative business models - this requires moving away from the linear “take-make-dispose” approach and finding new methods in production and consumption by developing and implementing circular solutions. This could be the biggest economic transformation since the industrial revolution and research plays a key role in achieving this ambitious goal. BASF is researching multiple projects, such as developing compostable and biobased consumer products (for example food packaging), recycling processes (for example recycling of mattresses) and ChemCycling™, a process which turns plastic waste into new chemical products. But of course, research does not stop here. We continue developing ongoing and new projects to push for a circular economy that saves energy and resources while reducing waste.
Find out more about our contribution to a Circular Economy and our sustainability goals.
Climate-friendly processes
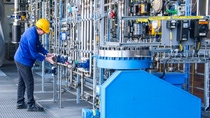
Net zero emissions by 2050
It is our goal, to achieve net zero emissions by 2050. In recent decades, BASF has already achieved a considerable reduction in CO2 emissions by optimizing energy generation and production processes as well as systematically reducing emissions of nitrous oxide. We continue these efforts by intensively focusing on improved production processes and fundamentally new technologies. Our researchers are working on multiple projects to prevent CO2 emissions from occurring at all, and additionally focus on integrating biomass, CO2 or waste as a raw material for chemical production.
One example is the methane pyrolysis, a new process technology for producing clean hydrogen from natural gas. The chemical industry needs large quantities of hydrogen. BASF, for instance, uses it as a reactant for the ammonia synthesis. As part of the Carbon Management program, we are working together with collaboration partners to develop this new process technology.
Deep dive into the methane pyrolysis and other examples to reduce CO2. More about BASF's carbon management efforts.
Sustainable Consumer Products
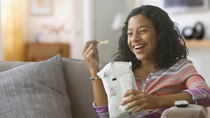
Research that combines high performance and sustainability
Today, we use more and more products in our daily life that follow the principles of circular economy. Our customers have a growing need to differentiate with sustainability. They face new regulations and standards in value chains, as well as changing societal and business environments. Thus, sustainability is starting in our labs with research to create new solutions for consumer industries. Let's take a look.
In everyday applications like automotive interiors, designer fashion and furnishing, our innovative synthetic leather solution Haptex® stands for sustainability in design and quality. Developed in our labs, Haptex® is the first solution for synthetic leather with zero organic solvent that adheres to low VOC (volatile organic compounds) standards.
Coatings today need to combine an ecofriendly profile with high performance. Be it with preservative free interior paints that provide high opacity and scrub resistance, such as Acronal® 6292, or with Joncryl® 9500, a water-based coating that forms a homogeneous surface that protects white furniture from tough household stains such as mustard, red wine and coffee, while ensuring high scratch resistance.
Saving water and energy resources when doing the laundry is another driver of our research. The results out of our labs are enzyme based liquid formats with excellent performance at low temperatures. Our new protease Lavergy® Pro grades lift stubborn stains like egg, blood and milk even at low washing temperatures between 20°C and 30°C (68°F and 86°F).
More about Haptex®, Acronal® 6292, Joncryl® 9500 and Lavergy® Pro. If you are interested how certified biodegradable plastics contribute to Circular Economy, please click here.