非凡工程:在中国建造模块化化工装置
用乐高积木搭建一栋自己设计的房子,是不少人童年美好的回忆。你能想象,如今,现实世界中的化工装置也能像搭乐高一样建造起来吗?
今年9月,位于巴斯夫上海漕泾生产基地内的全新抗氧化剂装置机械竣工。与以往不同的是,这一项目从巴斯夫董事会批复到竣工仅花了10个月的时间。建造过程中,施工现场的粉尘几乎为零,施工噪音也明显降低。这一切主要得益于高达90%的装置的预制率。建造过程中,整套装置被分为了10个模块,在异地独立的生产车间内,所有的设备、管道、仪表、电线等都在钢结构的框架内进行预组装,完成后被运往施工现场,与公用设施对接并进行拼装。
这是巴斯夫全球首套使用模块化制造方式建成的化工装置。随着施工机械化程度提高,现代化大型吊装运输能力不断增强,在日益讲求安全、高效的工程建设的背景下,模块化制造正在取代现场施工,成为巴斯夫大型投资项目的更有效执行方式。
模块化施工优势明显
巴斯夫亚太区工程与维修部高级经理陆国平负责整个抗氧化剂装置建设项目的设计、实施和机械竣工后的试运行支持。据他介绍,模块化制造具有诸多亮点,包括用时短、施工效率与质量可控性更好、施工安全性更高等。
首先是用时短。此次采用模块化方式建造大幅缩短了建设周期,是巴斯夫同规模生产装置从未达到的速度。传统建设工程需要先完成建筑工地土建,再进行上方工厂管道建设;现在,由于工厂在异地车间预制,土建和管道建设可以同时进行,因此能够节省大量时间。
其次,这种异地车间预制在厂房内进行,不受天气、环境等外界因素的影响,因此工人的工作效率显著提升,工程质量也更高。以焊接效率为例,传统建设工程中,焊接管道每个工人一天焊接的寸径数为20-25寸(单根管道的寸径或直径为1寸),而厂房内制作焊接量达到每人每天50-60寸。传统的装置建设往往在雨天就得暂停焊接工作,厂房内则完全没有这些因素的干扰,温度、湿度得到控制,还大大提高了焊接的质量。
最后,预制模式还免去了不少安全和污染隐患,提高了施工安全性。“传统建设工程需配置固定脚手架,安全意识差的工人爬上爬下有不少潜在风险。如今在车间内生产,虽然装置总高30米,但完全免去了固定脚手架。只是在需要的时候使用了移动脚手架,”陆国平说,“车间内还能进行管道自动焊接,没有烟雾、减少噪音,机床切割的铁屑还实现了再利用。”
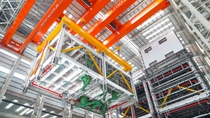
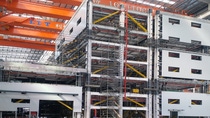
由于优势明显,这一施工方式提出后便获得了业务部门的肯定。“通过更高效地建立新工厂,我们能够缩短产品上市时间,并保障供货的连贯性。”巴斯夫化工有限公司负责抗氧化剂装置运营的翁建表示。
突破重重挑战
尽管模块化建设好处多多,但想要建成一座模块化工厂着实不易。“目前阶段,模块化施工的限制很多,特别是预制模块‘最后一公里’的陆路运输条件。”陆国平说,“而这是巴斯夫全球首个模块化项目,没有过往参考经验,一切都是从零开始。”在他看来,无论是工程设计、制造还是现场施工,整个团队戮力同心,才使得项目得以成功。
巴斯夫亚太区工程与维修部颜东波主要负责本次项目的工程设计管理。据其介绍,在工程设计阶段,巴斯夫与其全球工程合作伙伴沃利帕森的上海办公室组建了一支核心人员接近20人,总人数超过70人的项目团队。“各方合作伙伴参与其中,包括工程管理合作伙伴、模块制造商、设备供应商、海外专家和巴斯夫工程设计、生产技术、运营和工厂维修方面的同事。”颜东波说,“工程师们发挥各自所长,对各个组块都进行了精密的设计和计算。”
针对模块化工厂的特殊性,团队首先进行了道路勘察,包括运输时将经过的码头、吊机和漕泾基地最后一公里的陆路情况,在掌握模块制造、运输、拼装过程中的各项外界因素后,再着手设计。“模块化工厂的设计中既要考虑化工装置本身,也要思量如何分割各个模块:主体装置不能拆分、每个模块设计都需符合运输条件,模块间的连接也要尽量减少。”颜东波说。
设计的最大难点是如何避免模块在运输过程中变形。“模块在吊装、运输中的变形不仅会对拼装造成困难,还会造成土建楼面的损坏。要确保现场拼装成功,部件的偏差3毫米都不行。”颜东波指出。
其中,结构专业设计师面临的挑战尤其艰巨,他们需要全方位计算模块的受力条件,找到精确的重心,从而精准设计钢结构和模块的连接。为此,结构设计团队收集了大量数据,包括准确的部件信息,设备、桥架、管道、控制箱、甚至螺栓螺母等的精确重量,进行了超以往3-4倍的计算,以确保各模块日后的顺利组装。
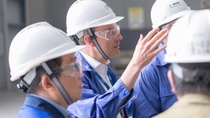
设计完成后,模块化装置开始在位于张家港的利伯特集团公司车间内进行预制。利伯特是中国知名的模块化部件制造商,曾服务于多个海外项目,其模块制造基地具有先进的制造设备和经验丰富的人员。由于良好的车间内安全控制环境,项目组可以更有效地管理装置制造的安全性和质量,并实现零工时损失的安全管理记录。“此外,在模块预制过程中,我们已经开始调试装置、排除故障,为工厂的试运行做准备。”陆国平介绍。

预制完成后,为期24小时的海路加陆路运输是对模块结构的一次严峻检验。
其中,最大的挑战来自于运输起吊期间的安全性。“因为化工工艺的要求,某些模块的重心偏得很厉害,起吊的时候容易变形,而且可能造成吊车翻车,”陆国平说,“如果增加吊车配重,费用会大幅上升。因此,根据每一个部件的重心,采用合理的吊装方式很重要。在大件吊装具有丰富经验的巴斯夫高级经理王昌银和安工院负责安全评估的专家的协助下,我们针对这些模块设计了更合理的吊具,确保吊车载重不变、吊车能安全起吊、吊件不变形。”
多方的共同努力最终换得了令人满意的结果:所有的模块运到现场后,变形量微乎其微,5天就完成了整套装置的拼装,所有螺栓完美连接。
未来潜力巨大
作为巴斯夫全球首个模块化项目,漕泾基地抗氧化剂装置完全由中国团队负责设计、执行。项目团队用实践证明了巴斯夫在技术和工程方面的综合实力,并展示其在质量、创新和安全方面的技术专长和价值。“我们很荣幸成为开拓者推动这一项目的执行,这对于真正实现定制化工厂至关重要。”陆国平说。颜东波也表示,当得知设计成果与实际结果相符,装置顺利拼装时,他感到十分自豪。
项目竣工后,巴斯夫全球各地不少团队对这一工程及其采用的模块化施工表现出浓厚的兴趣,项目团队迎接了一波波的访问团,其中既有工程部门,也包括其他业务部门、技术采购同事等。他们对工程设计、团队内部沟通、成本控制等方面都很关心。陆国平认为,作为一种新兴施工方式,模块化建设在未来潜力巨大:“在一些人工成本更高、气候环境恶劣的地区,或对于一些标准化程度高的化工装置,模块化施工或将成为一种理想的工程建造方案。”
目前,这一新装置已按计划顺利完成交付。新工厂现已经进入试产阶段。产品在经过客户认证后,将于2019年投入市场。届时,这一装置每年可生产 42000 吨抗氧化剂及相关产品和混合物,提升现有产能,以满足亚太市场日益增长的需求。