Sustainability
Fresh salmon packed with Styropor® Ccycled™: The world’s first EPS fish boxes based on chemically recycled plastics introduced in Norway
December 14, 2021
Fresh fish and ChemCycling™: How does this go together? In a joint project, three companies have demonstrated how it works: BASF as raw material supplier for EPS, VARTDAL PLAST, who converts the beads into filet fish boxes and Bremnes Seashore that uses the boxes for the transport of some of its high-quality salmon brand BÖMLO® as of Christmas 2021.
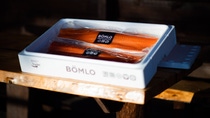
High-quality BÖMLO® salmon filets packed with Styropor® Ccycled™ / photcredit: Peter Tubaas, Vestland Media
“The EPS Fish Box is a well-known and trusted companion of ours with excellent properties for maintaining and securing the cold chain during transport. A secure cold chain is vital for food safety and preventing food waste. For us at Bremnes Seashore it’s exciting to try an alternative where the carbon footprint is significantly reduced and we always appreciate initiatives that promote the circular economy,” says Simon Nesse Økland, Head of Development at Bremnes Seashore.
Food contact approval and virgin-quality packaging
Thanks to its manufacturing process, Styropor® Ccycled™ has the same properties as conventional Styropor®. This maintains the excellent packaging properties such as thermal insulation and pressure-resistance with good buckling stiffness and stacking stability, which are essential to keep fish cool and safe at the same time. In the production of the packaging foams that have become so well-known over the last 70 years, pyrolysis oil replaces fossil raw materials. BASF sources this oil from technology partners who use a thermochemical process called pyrolysis to transform post-consumer plastic waste that would otherwise be used for energy recovery or go to landfill into this secondary raw material. BASF then uses the oil at the very beginning of the value chain to manufacture new plastics and other products.
Since recycled and fossil raw materials are mixed in BASF’s production Verbund and cannot be distinguished from each other, the recycled portion is allocated to Styropor® Ccycled™ using a mass balance approach. Both the allocation process and the product itself, have been certified by an independent auditor. In addition, a certified Life Cycle Assessment evaluating the environmental performance of the product concludes, that compared with conventional Styropor®, at least 50 percent of CO2 is saved in the production of Styropor® Ccycled™.
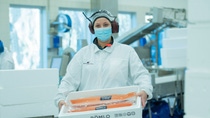
Perfectly cooled and packed safely: Styropor® Ccycled™ with proven properties and lower carbon footprint / photcredit: Peter Tubaas, Vestland Media
Styropor® Ccycled™ for each key application in BASF’s EPS product portfolio
“Chemical recycling of plastic waste is not only an essential building block to achieve the European circular economy targets but is especially useful for applications with high requirements for the quality and safety of the material such as protective packaging, pharma boxes and food packaging. We are therefore very proud of the ChemCycling™ project with Bremnes Seashore on EPS fish boxes and we are happy to have helped our customer to progress on his sustainability path,” says Klaus Ries, head of BASF’s styrenics business in Europe.
Also, for the converter VARTDAL PLAST Styropor® Ccycled™ brings a lot of advantages as the product is identical to virgin material. Therefore, the production process does not have to be adjusted. The company and their products are certified according to the ecoloop certification programme, confirming that 100 % recycled material was used as feedstock. “Bremnes Seashore has been a customer of VARTDAL PLAST for decades and we are excited that they are the first customer to choose VARTDAL AIRBOX LOOP, an EPS fish box made from 100 % Styropor® Ccycled™ raw material derived from chemically recycled plastics”, says Jan Endre Vartdal, owner and CEO at VARTDAL PLAST. “Our goal is to transform our entire production from using fossil based raw materials into using fossil free or recycled raw materials. The use of Styropor® Ccycled™ raw material from BASF enables us to begin this transformation in close cooperation with our customers without compromising on quality and recyclability”.
Circular economy in action: fish boxes are recyclable and recycled
EPS fish boxes are an important packaging product within the EPS product family. The first fish box was made back in 1965 and has since become an essential tool for transporting fresh fish all over the world. With an average weight of 0.6 kg per box the standard EPS fish box on average can carry 22 kg of fresh fish. In addition, EPS fish boxes are recyclable and recycled widely in Scandinavia and other European countries. Therefore, fish boxes are collected, compacted, and shredded. The shredded EPS fish boxes are then used as feedstock to produce recycled polystyrene which can be used for various applications such as insulation boards. “As a plastic producer we have a responsibility to contribute to getting our products back into the loop. For this reason, we have set up two high-capacity compacting sites in the middle of Norway and in the eastern part of Norway. By utilizing return freight, our own trucks collect and transport EPS from waste disposal sites, fish processors and building and construction hubs back to our compacting sites, where the EPS is shredded, compacted and palleted ready for recycling. Our long-term goal is to source the compacted material back into our product series VARTDAL LOOP® which only consists of products made from recycled or fossil free raw materials”, Jan Endre Vartdal adds.
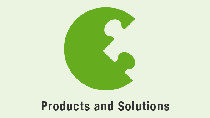