Sustainability
What's New
Latest News
Results: 445
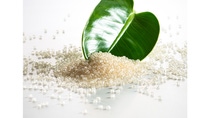
The world's first biomass-balanced polyethersulfone (PESU)
To all industries relying on high-performance thermoplastics, BASF is now offering the world’s first biomass-balanced polyethersulfone (PESU). Ultrason® E 2010 BMB contributes to substituting fossil resources, reducing greenhouse gas emissions, and increasing the use of renewable feedstock. This unique PESU enables customers in industries as diverse as household and catering, automotive, electrics and electronics (E&E), healthcare as well as water and sanitary to differentiate their products from the competition. It also helps them to achieve their sustainability goals - all without compromising on the material’s performance, quality or the need to invest extra money into new processing lines.
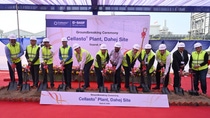
Cellasto® strengthens its position in India by taking steps for capacity enhancement
Dahej, India – February 24, 2025 – BASF India Limited has broken ground on a new plant to increase the production capacity of its Cellasto® microcellular polyurethane (MCU) in Dahej, India. Under BASF's new "Winning Ways" strategy, the plant will be constructed with state-of-the-art technologies and automation systems to ensure that BASF’s high standards of safety and quality are upheld. The plant, expected to be operational in the second half of 2026, features a new mold line in its first stage and empowers Cellasto® to meet the high demands of the rapidly growing local market.
This News Release is only available in English
This News Release is only available in English
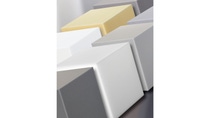
For sustainable sound absorption: the world’s first high-quality melamine resin foam with a reduced PCF
As the world’s first melamine foam manufacturer, BASF now introduces Basotect® EcoBalanced which helps to reduce the Product Carbon Footprint (PCF) of many sound absorption applications in the transportation as well as in the building and construction industries. Basotect® EcoBalanced has an up to 50% lower PCF than the respective BASF standard grades because of two sustainability levers: It is manufactured in a resource-efficient process using 100% green electricity; and the fossil raw materials needed to produce it have been replaced with renewable feedstock at the very beginning of the production. The renewable feedstock comes from organic waste and residual biomass and is attributed to the Basotect® grade via a mass balance approach which is certified according to REDcert2 and ISCC PLUS.
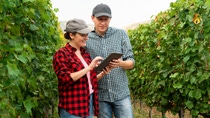
BASF launches xarvio ® FIELD MANAGER For Fruits & Veggies
Cologne, Germany - BASF Digital Farming GmbH announces its global expansion into horticulture, launching xarvio FIELD MANAGER For Fruits & Veggies today.
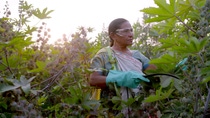
BASF and its partners publish 2024 results of the world’s first sustainable castor bean program, Pragati
Pragati, the world’s first sustainable castor bean program, completed eight years of operation in the 2023/2024 season. More than 8,000 farmers are now certified under the program, and individual farmer yields have increased significantly. The program has grown to more than 9,000 hectares of mostly semi-arid land under the SuCCESS® sustainability code.