Media
trinamiX: Enabling classifying and recycling at all levels
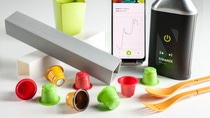
What kind of plastics? BASF's innovative sensing technologies support recycling efforts by identifying product specifics
Classifying and sorting materials – whether for product optimization or specifically for recycling – can be both challenging and costly. Founded in 2015, BASF’s start-up, trinamiX GmbH, is focused on innovative sensing technologies used in both classifying and recycling. Brian Schmatz, Business Development Manager for trinamiX North America, is working to ensure that barriers to recycling are removed. From animal nutritionists to recyclers to wineries, Schmatz helps customers utilize trinamiX to solve their most challenging problems.
How did you get your start in the sciences?
In high school, I enjoyed chemistry and physics, but I just kind of gelled with chemistry. I remember others not liking chemistry so much, which made me think there might be something there to pursue. So, I did my undergraduate studies in chemistry and did some research on solar cell technology. I found that very interesting and that was my entry into the field of organic electronics.
I knew that there would be many more options for me as a chemist if I pursued my Ph.D., so I looked for universities that offered research opportunities in organic electronics. I ended up going to Georgia Tech and became familiar with polymer-based electronics. It’s similar in the field, but instead of discrete organic compounds, it involved synthesizing polymers. I like to say that I straddle the line between an organic chemist and a polymer chemist. For me, it’s all driven by the application of these materials and the ways we can address big sustainability challenges.
Tell us a little bit about trinamiX.
trinamiX has two different technology focuses. One is 3D imaging where, essentially, we’ve got a proprietary algorithm that enhances applications like face authentication. We’ve created a new way of using the data you can get from a regular light projector and camera to make those applications more secure: our software is able to recognize different materials and thus to verify a person’s liveness by skin detection. The other focus, which is where I work, is infrared detection and spectroscopy. We have patents around our own semi-conducting infrared detectors that we not only manufacture and sell, but also package into a full trinamiX solution launched last year that looks like a simple handheld device. You can scan things and in seconds, get chemical information read back to you. For example, I can scan my skin and get its moisture and lipid levels. I can scan plastic scrap and see what polymer it’s made from. I could also scan foods and get protein, fiber and fat readouts. The applications can be customized based on customer needs, and these applications can be accessed and controlled through a smartphone app.
What kind of innovations have been made possible with trinamiX?
There are so many opportunities, which is exciting. I work with animal nutritionists who formulate feed on-site and use our scanner to get accurate protein and fat levels of farm silage in order to gauge what nutrients and additives must be added to create efficient feed. I also work with wine and grape growers who can use our device to assess quality and ripeness of growing grapes to optimize their harvest schedule.
In my role, I work with a lot of plastics recyclers. A lot of people in the plastics industry use trinamiX Mobile NIR Spectroscopy Solution to scan plastic pieces and read out what they’re made of. It helps determine how they can be recycled. I am very passionate about sustainability and I’ve been doing a lot of work on how we can enable circular economy opportunities with this device.
A big innovation that I’m excited about is fishing net recycling. We have a partner who uses one of our devices in their work with major fisheries. They take used, old and torn nets, fishing lines and other gear, and they can sort them on the spot. They can then find appropriate end-of-life opportunities for those materials. I’m working right now to see how we can bring that material into BASF and then repurpose it into a new BASF product made from fishing lines.
It’s an exciting way to get in touch with a lot of different stakeholders in the plastics chain and see how we can enable them to have better and easier sorting of these plastics by using trinamiX technology.
Tell us more about your work on the trinamiX team.
I really enjoy doing research, but I’m also interested in big-picture, conceptual work. So, moving into more of the business side from the lab was a good change for me. New business development was where I wanted to take my career because it gets you out into the world and shaping new ways of using an innovation. That’s a big part of how you get technology adopted – it’s not only the people in the lab making the technology, but its someone who knows how to find the right fit for it in our world.
I like that I’m still tied to the technical side and I love that I get to engage with our customers regularly. I like seeing how they use this technology in such different industries – from animal nutrition to cosmetics, dairy farms, and others. I’ve gotten to interact with so many different people in different fields.
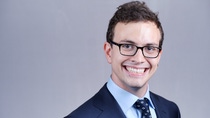
Brian Schmatz, Business Development Manager for trinamiX North America, is working to ensure that barriers to recycling are removed.
How does trinamiX technology help BASF’s efforts in the circular economy?
We have a lot of customers who are recyclers. Often, materials are channeled into huge recovery facilities with multimillion-dollar equipment that helps sort everything. The sorted plastic materials are then sold to smaller recyclers – who wash, grind, and repurpose it into new recycled-grade plastics. These recyclers typically do not have access to large-scale sorting capabilities, and so for them the trinamiX technology really helps assure they are buying and processing the correct plastic types. For example, PVC recyclers may receive hundreds of pounds of offcut labels to recycle and need a technology to be sure the labels are actually made of PVC. If, for instance, the labels were actually made of PET, it could damage their equipment and ruin the quality of their recycled PVC products. Because recyclers are so specialized, our technology provides assurance that the proper materials are being processed in the right facilities.
Previously, recycling could have been difficult for those recyclers working at a smaller scale, particularly on unconventional waste streams. We’ve found a lot of traction with these recyclers, and there are many of them across the United States alone. They need something quick, affordable, and portable that they can bring out on sourcing trips or have in their plant to quickly test something that might be creating a jam in their system. We’re able to approach these smaller, more localized waste streams – all of which are still significant – and help them achieve clean streams of recycled materials.
What’s your favorite project related to the circular economy?
A good example that I am very excited about is carpet recycling. Carpets, which are predominantly composed of plastic fibers, cannot be recycled through traditional curbside programs or through major sorting facilities. Instead, a specialized ecosystem of carpet recyclers exists to manage this unique waste stream – and they require tools to help them sort carpets by their plastic type (e.g., Nylon vs. PET). We are currently working with this community to not only create a carpet-specific identification app, but to also connect them back with BASF as a potential outlet for their recycled product. BASF already purchases reground materials from carpet recyclers and with that material has created a new composite product called Nypel. By enabling these recyclers to efficiently sort their waste streams, and provide an avenue for their re-entry into society, we are on the path to creating a circular economy for carpets. At the same time, we are working on similar projects with other unconventional waste streams like nets, textiles, and mattress foams.
It’s been an amazing start to our journey at trinamiX in enabling circular economy opportunities, and we are excited to see how our customers will continue to utilize our technology in this space.
For media inquiries and questions, please contact: katharina.meischen@basf.com.