Media
The future of comfort: flexible foam and innovation at BASF
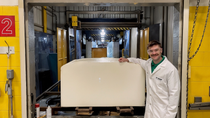.png)
After completing his bachelor’s degree in chemical engineering, Mark McBride began working for BASF in 2016. He completed his MBA from the Ross School of Business, University of Michigan, in 2023 and today is the Flexible Slabstock Foam Technology Lead at the Wyandotte, Michigan site. He is also the lead technical contact for customers and drives the development of new innovations in flexible polyurethane foam formulations. Learn more about Mark and his work below.
What exactly is flexible slabstock polyurethane foam, and what is it used for?
It’s known as slabstock flexible foam due to its continuous manufacturing process. Imagine a big conveyor line: all the chemicals are fed to a mixing head and dispensed onto a moving conveyor, and the polyurethane reaction takes place, causing the foam to rise and expand. This creates huge blocks of foam that look like giant bread loaves. At BASF we supply the two main components that make polyurethane foam: polyols and isocyanates. Flexible polyurethane foam is used in the furniture and bedding industry, as well as for automotive applications. The mattresses and pillows we sleep on, the couches and car seats we sit on, and the carpet we walk on all contain polyurethane foam.
What does the Flexible Slabstock Technology Lead do?
The team I'm on is responsible for the technical service and development of flexible foams. Essentially, we are the main technical contact for our customers, and we work closely with our sales and marketing teams. While our account manager handles pricing and supply, I work alongside the commercial team and handle all the technical aspects of our customers’ needs. This involves recommending products for specific applications, developing new products based on customer requests, troubleshooting issues they may be experiencing at their sites, and traveling to their plant locations to run trials of new formulations and products.
How are your research operations structured for flexible foams?
Here in Wyandotte, Michigan we have our flexible foam labs. They are small benchtop-scale labs where we can embark on quick development projects. We also have a pilot scale area, where we run a larger slabstock foam machine. One of our main selling aspects to our customers, and what differentiates us from some of the other suppliers and competitors in the industry, is the fact that our pilot line mimics what our customers have at their production sites. If we can make high-quality foam on our pilot line, it will directly reflect the capabilities our customers can expect at their production facilities. This seamless scalability saves our customers time and money.
Often our development projects come from specific customer requests. They might ask, “This is what we're looking for. Do you have this specific formulation or product in your portfolio?” If we have something off the shelf, we will share the information with them. If not, we can start a project to try and meet those needs.
Overall, our group's main objective is to support the diverse needs of our customers and beyond. We maintain a continuous dialogue with our contacts across the bedding and automotive industries to get a clear view of current opportunities, trends, and needs. We also attend industry events and stay up-to-date with all the relevant technical papers to help us understand what's coming down the pipeline. In line with BASF’s strong commitment to sustainability, many of our flexible foam customers are requesting sustainable raw materials, support on how to reduce their product carbon footprints, foam recycling, and more. I am proud that BASF offers the technology and expert support to fulfill the industry’s growing demand for these sustainable solutions.
How much does innovation play a role in R&D in the flexible foam sector?
A big part of our innovation pipeline is customer-driven and comes from specific requests, but we also work closely with our new business development team. In addition to our own innovation work, the team scouts and brings ideas to us so that we can advance larger-scale phase gate research and development (R&D) projects.
The innovation pipeline is an important part of what we do, whether it’s kicking off new projects, making slight tweaks to our existing portfolio, or advancing our portfolio of sustainable solutions.
Can you explain what the digitalization and predictive modeling of the foam formulations project is about and your role in it?
To continue our long and storied history of flexible foam innovation at BASF, we are always looking for ways to modernize and further digitalize our processes. I’ll use the example of our predictive modeling project. The main purpose behind it was to create a digital log and database where all the details of our many foam formulations and trials could be stored. Before this, the results from all our lab and pilot trials were scattered throughout lab notebooks and Excel formulations across multiple databases and file systems.
To improve the organization and searchability of our formulations, we created a new database and tied in different systems to feed all our information into one area. Now, when I run a trial on our pilot equipment, the particular foam formulation, all physical properties associated with it, and processing conditions are all tied into the database. I can now type in a unique identifying number, and the database pulls up everything associated with that experiment.
Once the database was set up, we took the technology to the next level. We leveraged data science and began modeling, extrapolating, and predicting the foam properties for a specific foam formulation. The data science team in BASF’s central research group put together a modeling app that constantly accesses the database we created with our flexible foam formulations. We recently presented this powerful tool as it relates to new-generation foam development, and it certainly sparked a lot of interest from our customers.
As demonstrated by this digitalization project, our team is constantly innovating and working to bring the best solutions and support to the industry. I am excited to be part of the next wave of flexible foam innovation here at BASF – serving our customers and countless consumers across the region for years to come.
For questions, please contact Mariana Licio.
For media inquiries, please contact Molly Birman.