Towards the “passive” era
Passive house, as a model of energy-efficient buildings, has been introduced to China. Will it lead the Chinese construction industry towards a new era?
Changxing County by the Taihu Lake in Zhejiang Province turns all scorching and humid in August. When the outdoor temperature reaches 35 centi-degrees, the vapor in the air would make one feel as if in sauna. However, if you walk into the Bruck Green Boutique Hotel completed just recently, the heat and humid and everything that irritates your body will be just gone and replaced by fresh, dry air and a suitable temperature of over 20 centi-degrees.
Surprisingly, this unique German style hotel does not use any air-conditioning method – the comfort was simply achieved by ventilation system with low energy consumption.
The hotel with an area of 2,500 square meters has 48 standard rooms and 4 suites. Judging from the interior decoration and design, it is just like an ordinary boutique hotel. However, it is the first large passive house designed and built by Chinese developer for hot summer and cold winter climate of Yangtze River Delta region, a house certified by Passive House Institute (PHI) in Germany, as well as the first project in China fulfilling requirements of three standards - China Three Stars Green Building Evaluation Standard1, DGNB (German Sustainable Building Certificate) 2 and LEED3.
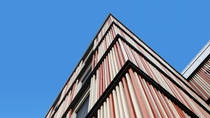
“Passive houses allow for space heating and cooling related energy savings of up to 90% compared with traditional building blocks and over 75% compared to average new buildings – substantially less than common ‘low-energy’ buildings,” said Dr. Wolfgang Feist, Director of PHI.
As Feist introduced, passive houses make efficient use of the sun, internal heat sources and heat recovery, rendering conventional heating systems unnecessary throughout even the coldest of winters. During warmer months, passive houses make use of passive cooling techniques such as strategic shading to keep comfortably cool. Special windows and a building envelope consisting of a highly insulated roof and floor slab as well as highly insulated exterior walls keep the desired warmth in the house – or undesirable heat out. A ventilation system imperceptibly supplies constant fresh air, making for superior air quality without unpleasant draughts.
“The advantage of passive house is not only in energy saving, but also in enhancing the comfort of living to a great extent. That is our greatest motivation to build a passive house in China,” said Tian Ming, Chairman of Landsea Group Co., Ltd. (Landsea).
In 2011, Tian visited Feist who is known as the “Father of Passive House” in Austria. After a long conversation, he captured the core elements to build a passive house: adapted to climate and local conditions, as well as low technology. “Every place has different climatic conditions, which should be a major consideration. Passive house is not an integration of high technologies, but leverages natural conditions to achieve lower energy consumption and better comfort,” explained Tian.
Germany is the country with most densely located passive houses in the world. It now has thousands of passive houses. According to German government, by 2020, all new buildings must achieve the “zero emissions” standard. For this reason, passive house construction in Germany has received more and more attention.
However, if we copy the model of German passive houses entirely here in China, we are destined to fail. Germany is mainly in the cold temperate zone, while China has a vast territory spanning multiple climatic zones, each with different features. “The main climate feature of China’s Yangtze River region is hot in summer and cold in winter, which creates entirely different conditions to the construction of the passive house than in Germany where only heat insulation in winter is considered. In China, we not only need to keep the indoor temperature warm in winter, but also to achieve coolness and removal of moisture in summer, which is very challenging, ” said Xie Yuanjian, Vice President and Technical Director of Landsea.
After returning from Austria, Tian decided to build the first passive house in the Yangtze River Delta region. Landsea was facing many challenges at that time, for example, how to find an innovative way to adapt the passive house to local conditions, how to achieve high air tightness and how to handle cold and thermal bridge during construction. Besides, there were few supporting suppliers for passive house construction, which leads to difficulties in project management and cost control. To conquer the challenges, Landsea invited PHI for evaluation and consultancy throughout the construction period, and cooperated with partners who were experienced in passive house construction, like BASF.
After designing and planning stage for over a year, Passive House Bruck began construction in April 2013 and was completed a year later. “It’s proven that Bruck met or even surpassed the indicators for German passive houses,” disclosed Tian with pride. “With this successful case, we are planning to introduce passive houses to our real estate projects in China.”
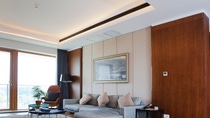
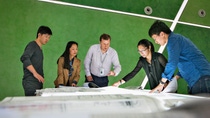
As a representation of energy-efficient buildings, passive house has multiple advantages. “In thermal insulation properties, for example, boiling dumplings in a passive house in winter for once could increase the indoor temperature for two centi-degrees which lasted two days,” said Zhang Xiaoling, Head of Project Cooperation Division, China’s Ministry of Housing and Urban-Rural Development (MOHURD), taking her personal experience in a passive house project in North China for example.
She also summarized other advantages of passive house, including energy saving, independence on fossil fuels, no worry of the heat island effect, longer service life and health benefits for occupants, etc. “Energy used for heating every year in North China equals roughly to 200 million tons of standard coal. However, when these buildings become passive houses, energy consumption can be reduced to 14 million tons,” said Zhang. She disclosed that currently MOHURD is formulating a standard for passive house construction in Hebei Province, in which BASF is also an active contributor who provides professional suggestions on some indices.
Passive houses have so many advantages that people are wondering about their economic return on investment, to which Feist responded with his experience in Germany. “In fact, the investment of passive houses is only about 5% higher than ordinary buildings,” said Feist. “In the long run, with the energy cost savings, the initial extra investment of passive houses can be recovered quickly in a certain period.”
However, due to comparatively lower building standards in China, the initial investment costs for passive house in China are much higher than the percentage in Germany. “It’s expected to be 20% to 50% higher,” said Xie. “This could be a substantial income in the highly competitive real estate market.” For this reason, Xie believes that different levels of standards should be implemented to meet the market needs.
Feist expressed his optimism towards the positive prospects of the passive house market in China. According to him, the main obstacle in passive house development is not the cost, but the whole process of mastering passive house development technology and process to adjust to the local conditions. “Passive house is an open system and is not patented. What it requires to build a passive house is a long and committed learning process,” said Feist.
Supplier could be another factor influencing the development of passive house. “At the moment the number of suppliers able to provide materials or components of passive house is very small, which also leads to the high cost. However, as time goes by, the cost will be reduced sooner or later,” he explained. Currently he still resides in the world’s first passive house he built by himself in 1991. “It is still in a good state after over 20 years.”
BASF is very experienced in global passive house renovation and construction. As early as in 1996, LUWOGE, an architectural design firm under BASF began to rebuild the Brunck residential quarter, an old building block first built in 1930s, into a more energy-saving and comfortable one in Ludwigshafen, the location of BASF headquarters. By virtue of its passive house concept, BASF made continuous breakthrough in reducing energy consumption per unit area, creating the “7-liter house”, “5-liter house” and “3-liter house” and is now making efforts towards “zero-heating cost house”. In Europe, North America and Asia, LUWOGE designed and participated in the construction of many sustainable building projects. During the World Expo 2010, BASF provided insulation solutions to the Hamburg House, China’s first certified passive house.
"We are actively developing the business related to passive houses in China, contributing to the future of sustainable construction," said Dr. Liu Yanli, Senior Manager, Industry Team Construction Greater China, BASF. "In addition to thermal insulation materials for roof and external wall, BASF also provide a series of solutions including flooring and window for passive houses."
1 China Three Stars Green Building Evaluation Standard is the highest level of certification among all green building assessment standards in China.
2 DGNB (German Sustainable Building Certificate) is a system describing and evaluating building sustainability developed jointly by Transportation, Architecture and Urban Construction Department, The German Federal Agency.
3 Leadership in Energy and Environmental Design (LEED) is established and implemented by The United States Green Building Council.