Innovative catalyst technologies for cleaner air
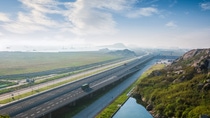
Roads within cities form a traffic network while the vehicles driving on them support economic development and people’s lives. Vehicles including buses, trucks and long-distance coaches, among others, powered by diesel engines are a non-negligible part. While they do meet people’s travel needs and carry cargo, they have also created problems such as traffic congestion, noise and exhaust emissions.
It is an indisputable fact that diesel vehicles produce high emissions. In the China Vehicle Environmental Management Annual Report 2017 released by the Ministry of Environmental Protection Department, statistics show that nitrogen oxide (NOx) emissions from diesel vehicles in the country accounted for nearly 70% of the total vehicle emissions, and the proportion of particulate matter (PM) exceeding 90%. A large number of fine particles floating in the air forms a smog. In addition, according to research results published online in the journal PNAS by the Wang Gehui Research Group of the Institute of Earth Environment, Chinese Academy of Sciences, nitrogen dioxide and liquid-phase oxidized sulfur dioxide found in atmospheric fine particles are a cause of the formation of sulphates during smog, and sulphates are one of the major components of PM2.5.
In the past, diesel fuel quality was poor and companies were afraid of losing cost advantages due to the price increase caused by technological upgrading. Diesel emission standards were not strictly enforced.
Over the past few years, the public call for a solution to the smog has been increasing and the government has shown its steadfast determination to solve the problem. In the past two years, the intervals of Beijing’s issuance of motor vehicle emission regulations have become shorter and the standard requirements have been more tightening. Take the heavy-duty diesel vehicle standard in the China National Stage V emission regulation (NS V for short) for example. Compared with the China National Stage IV emission regulation (NS IV), the NOx emission standard is set to drop from 3.5 g/kWh to 2 g/kWh; by 2020 when the China National Stage 6 emission regulation (NS VI) is implemented, this value will drop to 0.4 g/kWh. In addition, emission requirements in actual on-road driving conditions tested by portable emission measurement system (PEMS) are added to the NS VI regulation, i.e. vehicle emissions should reach the standard under both laboratory conditions and actual normal driving conditions. It can be recognized that diesel vehicles have become the focus of China’s vehicle emission treatment issue.
The new version of the Atmospheric Pollution Prevention and Control Law of the People’s Republic of China (New Atmospheric Law for short) was formally implemented on January 1, 2016, and the status of the Ministry of Environmental Protection as the main body of regulating vehicle emissions has been defined. In terms of regulatory means, the government has transformed the former practice of focusing on examination and approval while neglecting supervision of the present practice of emphasizing supervision over permission. In the past, it was alright as long as the vehicles submitted for inspection were compliant, but now each should be compliant and reach the same standard as well as being subject to a spot check at any time.
In facing stringent emission standards and more elaborate and transparent regulatory means, the diesel vehicle industry is experiencing a vital battle. How can companies get through this siege? Product upgrading driven by innovative technologies may be the only way out. As a result, companies have had to change their approach and have begun to attach importance to policies and regulations, research trends and actively participating in technological and product upgrading. Forward-looking companies have already experienced competitiveness resulted by innovation from technological upgrading.
“BASF is one of the closest partners of Weichai and we are willing to choose international suppliers with good reputation and technical competence as our partners.”
Feng Gang, Vice President of Weichai Power
Founded in 1946, Weichai Power is one of the most powerful automotive and equipment manufacturing groups in China and a market leader in the development and production of high-powered engines. Its product development has been widely recognized by the industry.
In the view of Feng Gang, Vice President of Weichai Power, technical strength is an important guarantee for the company to win the market. Reducing emissions has been a major focus of engine technology innovation. “Weichai is forward-looking regarding emissions in relevant areas. Since the issuance of the China National Stage III emission regulation (NS III) in 2006, it has been unswervingly implementing relevant national laws and regulations and developing appropriate technical routes.”
With the continuous enhancement of emission standards, it becomes almost impossible to meet relevant requirements using in-engine purification technology improvements. To maintain its leading edge in technology, Weichai has been attaching great importance to cooperation with an “external brain”.
“BASF is one of the closest partners of Weichai and we are willing to choose international suppliers with good reputation and technical competence as our partners,” said Feng.
In 2005, BASF became the first catalyst supplier for Weichai’s after-treatment system. The company also cooperated with Weichai in its R&D on engine after-treatment systems. It has addressed this challenge by installing a catalyst-equipped after-treatment system to the engine. “For more than 10 years, BASF has provided Weichai with technical support and new ideas regarding the after-treatment systems,” said Feng.
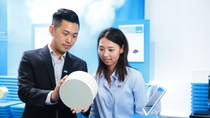
During this period, BASF provided Weichai with a series of diesel vehicle emission control catalysts suitable for the NS IV and NS V emission regulations. For example, the WP10, WP12, WP7 engines of Weichai are the first to meet the requirements of NS IV emission regulations. They are equipped with the after-treatment system that adopts BASF’s vanadium-based selective catalytic reduction (SCR) catalyst. This technology can transform NOx into water and nitrogen in the presence of a urea solution. Its advantages include a wide applicable temperature range, high durability and improved hydrocarbon poisoning resistance.
Through years of cooperation, Weichai has fully come to trust the reliability and support of BASF’s technologies, and the two sides have gradually formed a strong relationship. In 2008, BASF became the initial member of Weichai’s R&D Community. This community aims to invite relevant suppliers to collaborate and innovate on the same platform in the early stages of product R&D and project approval. This is undertaken to shorten the R&D cycle and reduce R&D costs. In 2015, by virtue of its after-treatment simulation software CatSim with independent property rights, BASF provided Weichai’s engine electronic control unit (ECU) control software with after-treatment system dynamics support.
To become a market leader, it is required to not only meet current standards but also look further afield. “When the NS V emission regulation was issued, Weichai’s laboratory standards had already been stricter than the national standards. We took full account of the oil quality after marketization, user maintenance and actual road conditions, and did a good job in developing technical reserves in advance,” said Lang Junyu, Deputy General Manager of Weichai Power Air Purification Technology Co., Ltd. These indicators were the issue to be considered in the national emission regulation setting process of the next stages.
In October 2015, the government issued a new regulation – the Special Beijing V emission regulation. This required that as of January 1, 2016, all new heavy-duty diesel vehicles should implement the fifth-phase emission standards. In addition, heavy-duty diesel vehicles used in the administrative area were recommended to adopt a Diesel Particulate Filter (DPF) with a high purification rate to ensure that the the number of particulate matter (PM) was no more than 6x1012, which is stricter than the NS V emission regulation. Fortunately, Weichai had already started the technological R&D with BASF targeting the NS VI emission regulation. By the time the new regulation was issued, relevant products had already created a strong foundation and product upgrading could easily be conducted after debugging and matching. This helped Weichai to seize market opportunities.
When relevant national policies and regulations change, Weichai needs to re-evaluate the entire system. As the NS VI emission regulation incorporates a vehicle’s actual on-road emission (RDE) test results into the measurement system and requires the use of a portable emission measurement system (PEMS) for testing, the diesel vehicle emission limits are facing more stringent requirements. This means catalyst performance needs to be further enhanced. At present, BASF is working with Weichai to upgrade and improve after-treatment-related technologies. The WP10 engine series is one of Weichai’s engine products with the highest sales volume and has been popular since the NS III emission regulation was issued in 2011. BASF’s solutions can help this engine meet more stringent emission requirements under the premise of maintaining the original engine size, thus guaranteeing the vitality of the product. This program has taken the lead in passing the internal verification of Weichai. In addition, BASF’s products and technology can not only meet laboratory testing requirements but also reach emission standards under an aging state with outstanding stability. This is an important guarantee for the manufacturer to pass testing and maintain quality stability.
“We hope that with future cooperation, especially regarding the NS VI emission regulation, BASF can introduce foreign resources and experience into China, and meet the country’s actual road demands through innovative R&D for China,” said Feng. “This is the guarantee of meeting national emission standards as well as maintaining Weichai’s competition differentiation.”
“We are committed to developing innovative and cost-effective solutions to help our customers cope with the most stringent emission control regulations while improving their comprehensive product capabilities and achieving greater business success.”
Dr. Michael Baier, Vice President of Mobile Emissions Catalysts Asia Pacific, BASF
As a global leader in the field of catalysts, BASF has not only one-sided industry experiences across regions but also a wealth of product lines. So far, the company has introduced multiple products targeting the upcoming NS VI emission regulation. For example, BASF’s copper-based selective catalytic reduction (Cu-SCR) catalyst has adopted BASF’s patented copper-based molecular sieve technology. It can reduce NOx emissions by up to 95% and it is of excellent durability and a wide applicable temperature range. SCR on Filter combines SCR catalyst with diesel particulate trap, realizing the removal of both NOx and particulate matters (PM) by using a single substract. While meeting relevant new emission requirements it saves more after-treatment system space, thus reducing the overall system costs.
“BASF owns a strong development competence in China and has maintained a long-term relationship with Weichai,” said Dr. Michael Baier, Vice President of Mobile Emissions Catalysts Asia Pacific, BASF. “We are committed to developing innovative and cost-effective solutions to help our customers cope with the most stringent emission control regulations while improving their comprehensive product capabilities and achieving greater business success.”