Composite utility poles: conquering the wind
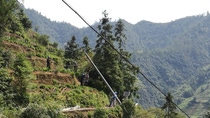
Surrounded by peaks with steep rocks, Huangshan is a typical mountainous region in eastern China’s Anhui province. The dangerous terrain makes it difficult to install utility poles. Dong Qiaonan, who had worked at Anhui Electric Power Design Institute for more than 30 years, deeply understood the challenges in it.
A traditional cement pole weighs 1,200 kilograms and requires dozens of workers to carry it up the mountain. The poles, which are more than 10 meters in length, have great tail beat amplitude when making a turn, which can easily hit those moving them. In addition, there has been a massive loss in young manpower in mountainous regions in recent years. Therefore, the installation work often faces difficulty in recruitment.
In severe winter conditions snow and ice on the wires can easily produce an unbalanced force that will break the traditional poles. “Due to difficulties in installation, the repair time is often long,” said Dong.“Previously in Huangshan, power blackouts happened frequently for one week or so.”
In addition to installation challenges and difficulties in repairs the cement poles do not have a long service life. In general, cement poles installed in a good environment can be used for 20 years. “At present, there are about 500 million to 1 billion utility poles in China, with up to 50% of them ‘running sick’,” said Dong. Cement is a brittle material that can easily crack at the surface after three to five years of high temperatures and cold weather. When the rain or snow penetrates into the poles and corrodes the internal steel bars, the cement poles easily collapse. In some extreme environments, such as saline soil or beach wetlands, the service life would be even shorter.
To tackle the challenge, BASF has started to explore the application of polyurethane (PU) materials in the power industry since 2010. It was an innovation based on market demand and born in local R&D labs. Meanwhile, in order to understand the situation in the Chinese market, construction team of Performance Materials, BASF invited Dong Qiaonan, who has 30 years of industry experience, to become a project consultant. In Dong’s view, the breakthrough of this issue lies in the development and application of new pole materials. Thanks to the accumulated experience of the R&D department in the field of polyurethane composites, BASF was capable of changing the industry. Therefore, Anhui Huike Hengyuan Composite Material Company Limited, founded by Dong, began cooperating with BASF on the PU composite utility pole project, covering aspects of R&D, production and marketing, among others. The cooperation allows high-quality and reliable products used in the power industry to safeguard the power supply.
The utility pole is made of the BASF PU composite material Elastolit® and its advantages are fully demonstrated in the actual use: it is of good rigidity and flexibility that can stand firm in snow and ice, strong wind, wood lodging and other natural disasters. Weighting one-sixth of traditional poles, installations are easier; only two workers are needed to complete the entire process from transport to installation. Moreover, its service life can reach 50 years. “Composite utility poles can significantly shorten the time of power supply repair and reduce the cost of their installation,” said Dong. “Therefore, it brings a profound change to the power industry.”
For Dong, who was familiar with the power industry but not proficient in production, BASF offered more than raw material supply. “BASF helps us in all aspects, including introducing equipment suppliers and providing manufacturing guidance,” he said. When the production line was first set up, BASF stationed technical staff to guide the manufacturing. “BASF has been in the industry for many years and has accumulated a lot of practical experiences,” said Ellen Yang, Manager, Sales, Construction Performance Materials, BASF Greater China, “We not only provide support on materials but work with customers to create higher value-added solutions.”
In addition to Huangshan, China’s southern coastal cities and some Southeast Asian countries, which often hit by typhoon, also benefited from the new composite utility poles. In July 2014, when the level-14 Typhoon Rammasun blasted Guangdong province, it was the composite utility poles that withstood the wind. Thanks to their good performance during typhoon conditions, the poles were recognized by China Southern Power Grid Company Limited.
It takes a lot to achieve the current results. As we know, the power industry has a very high standard in product quality. The access threshold is high and the products are required to undergo rigorous product experimentation and effect demonstration. With the good performance of composite utility poles in the south, Dong and Huike Hengyuan are now in active contact with the State Grid Corporation of China (SGCC) to develop application scenarios under more geographical surroundings and meteorological environment. Pilot projects for the composite utility poles have been carried out in Guangdong, Yunnan, Hainan, Xinjiang, Tibet, Hunan, Hubei, Anhui and Fujian, among others.
The extension in application scenarios has brought new requirements. The “one pole for all scenarios” seems too ideal, and the business model of “selling the standard products” have no way out. “Materials will have the maximum value only in the practical application,” said Ellen Yang. “Therefore, we need to start with the actual demand in the power industry and move from answering ‘what do we provide’ to ‘what do we solve’”.
In Xinjiang province in China’s north-west, utility poles are required to withstand strong sandstorms. “A colleague once saw the cement poles heavily damaged by Level 12 sand storm in Turpan, Xinjiang, which were full of small holes,” said Ellen Yang. In view of this scenario, Huike Hengyuan and BASF had an in-depth discussion. The two sides found that by adding a protective layer to the poles they would be able to resist this severe environment. However, they could not find a protective layer supplier at the time. Therefore, BASF sought a manufacturer and invited them to join in the development of a product perfect for sandstorm scenarios. Next, BASF will work with parties along the supply chain to provide relevant solutions for the extreme weather (minus 60 degrees Celsius) in Xinjiang.
At present, the application of composite poles focuses mainly on low-voltage distribution networks, while high-voltage transmission networks remain open to innovation. As high-voltage transmission towers are steel structures that can weigh tens of tons, their transport costs can be very high. In Europe, research on lightweight towers has been carried out. In Norway, university research institutes and BASF are collaborating on the development of new composite materials for the towers. As a leading chemical company, BASF provides not only raw materials but Computer Aided Engineering technology at an early stage of development. This technology can simulate the structural mechanics performance of complex engineering and products, thus largely reducing the time required for R&D.
The new materials can not only be used in the power industry, but also embrace great business opportunities in the telecom field. The 5G network is the future development trend of the industry, on which autopilot and telemedicine rely. “The signal poles design may refer to street lighting and communication network to ensure the speed of 5G signal transmission,” Ellen Yang explained. “The use of traditional cement or metal materials could result in great loss of 5G signals, while it won’t be a problem with composite poles.” At present, domestic telecommunications equipment suppliers are looking for new materials for signal poles to which BASF has responded positively. “We hope to provide an excellent solution with our in-depth understanding of the industry and mastery of the scenarios,” Yang said.