Performance materials: a magician changing the world
How does plastics arouse the passion in people?
How can plastics change people's lives and begin an imaginative era?
In 1912, BASF set up the first materials testing laboratory in the chemical industry. It was the precursor for materials engineering today, to solve the growing materials-related problems and the associated safety issues.
Since the 1950s, BASF has been in an era of product innovation with plastics. Plastics, a collective term of a wide range of polymers, can be modified to demonstrate excellent physical and chemical properties over conventional materials. These include superior strength, hardness and heat, abrasion and corrosion resistance.
Such plastics are called "performance materials". They have found extensive applications in the transportation, construction, industrial production and application, and consumer goods sectors. They have become indispensable for industrial production and everyday life and are quietly but magically changing the world.
Styropor®, a foamed polystyrene, was only used for wire insulation and lifebuoys when it was first produced by BASF in 1951. Its breakthrough as an insulation material only came towards the end of the 1950s when, due to its excellent insulating properties, Styropor® was increasingly used in the construction industry and for refrigeration. Today, it is the classic among insulation materials.
The importance of plastics in the transportation industry was discovered through experimentation. In 1964, the auto maker Porsche applied BASF plastic “Palatal” to the exterior of its new model 904 Carrera GTS and successfully reduced the weight by 150 kilograms, hence lowering fuel consumption and emissions. The car became the first lightweight vehicle and caused a sensation worldwide. Today, lightweight has become a major trend in the automotive industry and is of great significance in energy reduction and environmental protection.
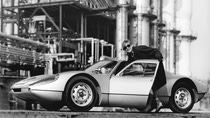
Tay Jui Seng, Vice President, Business Management Transportation, Performance Materials Asia Pacific, BASF, explained that today's innovations not only applies to the development of new materials but also on the smart use of existing materials in innovative applications.
"How do we meet customer requirements through the use of existing materials, development of new products and application development know-how is something we always take into consideration," said Tay. "With a broad product portfolio and profound industry expertise, BASF is committed to integrating chemistry, process and market needs to create innovative solutions and address various challenges of urban life."
In March 2016, the adidas NMD sneakers started a worldwide craze. The shoe’s biggest highlight is the midsole that uses BASF's revolutionary material Infinergy®, the world's first expanded thermoplastic polyurethane (E-TPU).
Infinergy® is made of expanded thermoplastic polyurethane (E-TPU), which is manufactured by foaming the starting material, TPU granules. After pretreatment with pressure and heat, the individual granules, measuring up to five millimeters each, are blown up like popcorn and their volume increases tenfold to produce oval foam beads with tiny, closed gas bubbles inside.
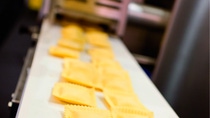
Therefore, sneakers using Infinergy® are not only lightweight, but can effectively absorb the impact on feet when jogging. In addition, the high-rebound effect of Infinergy® can provide much energy to bring a unique and comfortable experience to runners.
As more and more people have learned about Infinergy®'s uniqueness, its range of applications continues to grow. For instance, Infinergy® has been used in the central part of the rebound racket most recently launched by renowned sports racket manufacturer Dunlop. Its unique foamed microsphere structure makes it an unprecedentedly lightweight high-elastic material and significantly improves the racket's performance and durability, enabling players to make each swing confidently.
Recently, how to provide eco-friendly, safe and durable-sports venues for children has increasingly become a public concern. BASF has not only created modern fashion sporting goods, but also protects children from harm when playing.
BASF's newly developed sports flooring solutions include eco-friendly plus weather resistant polyurethane systems Elastan®, and Elastocoat® combined with E-TPU foam particles, whose formulations and applications don't need any other organic solvent or heavy metal. Eco-friendly materials can pave the way for the health of children instead of causing any harm to them (construction workers included). The use of Infinergy® in a running track can effectively reduce the impact of falling due to its excellent rebound performance to guarantee the safety of children.
In June 2016, the “Limits of the Harmful Substances in the Plastic Surface of School Sports Venues” was officially approved as a group standard for plastic running tracks in Shanghai. By using construction-convenient, safe and harmless BASF sports flooring materials, Dingding Kindergarten in Shanghai’s Minhang district has become one of the first educational institutions in the city to offer safe plastic flooring since the introduction of the industry standard.
In the 1970s, BASF and Porsche co-developed plastic (polyamide-based) intake manifolds, which broke through the bottleneck of industrial development. The intake manifold, located between the vehicle's throttle valve and the engine's intake valve, distributes the air and fuel mixture to each cylinder inlet.
The reason for the use of plastic intake manifolds is that metal manifolds have a complex forming process. It is difficult to process large hollow parts of such a complex shape using general technology; semi-finished metal products have a low yield and high machining costs. However, plastic intake manifolds may be integrally molded, have a high yield and reduce the overall cost by 20-35% on the premise that the process is workable. In addition, plastic manifolds are 40-60% lighter than metal manifolds and can dramatically reduce vehicle weight, fuel consumption and emissions. When mass-produced, plastics can better demonstrate process, cost and environmental advantages.
"BASF innovatively replaced steel intake manifolds with plastic ones,” said Tay. “Its commercial value has been fully recognized, which shed light on lightweight development in the automotive industry."
In recent years, as a raw materials supplier, BASF has closely cooperated with customers and actively participated in their product and process design by fully leveraging the advantages of plastics and constantly developing innovative applications of lightweight components for the transportation sector.
The BMW 5 Series Gran Turismo 550i sedan is the first to use BASF Ultramid® polyamide plastic to manufacture the gearbox beam bracket instead of traditional aluminum, reducing the part’s weight by 50%. The gearbox beam bracket, as a structure directly connecting the engine and gearbox, needs to bear a greater load. Gearbox beam brackets of good quality can help improve a vehicle's robustness and provide support for the power and torque output of the engine gearbox unit.
In addition to reducing weight, the plastic gearbox beam bracket significantly lowers driving noise, improves crash safety, and enhances safe driving performance. Not long after the BMW 5 Series Gran Turismo 550i was put into production, the gearbox beam bracket manufactured with BASF's ultra-high strength polyamide was awarded the Gold Innovation Award by AVK.
In the aviation field, the combination of the innovative Ultrason® carbon fiber panels and the Ultrason® honeycomb panels produces a synergistic effect and can replace traditional metal materials. They not only make aircraft's structural components lighter, but also guarantee reliable structural strength and bring natural flame retardant properties while meeting strict technical specifications.
Getting lighter but safer, more durable and eco-friendly is exactly the contribution that materials technology development has made to the modern society.
BASF WALLTITE®, a kind of spray-applied polyurethane foam, is an insulating air barrier system. While WALLTITE® and Infinergy®, which is used for the midsole of adidas sneakers, are made of polyurethane, they differ in hardness because of different formulations.
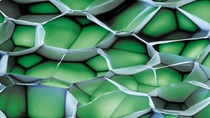
The polyurethane foam used by WALLTITE® greatly reduces the thickness of the insulation layer as its thermal conductivity is much lower than that of other insulation materials. WALLTITE® also creates a comfortable living environment and reduced harm to nature for its higher flame retardancy (carbonization, melting-free), strong air tightness, construction convenience and a long service life.
In addition to the "coats" of buildings, BASF has made great efforts in its "cuffs" and "collars". The Ultradur® co-extrusion reinforced materials produced using the polyurethane pultrusion technology can be used to make door and window sub-frames for energy-efficient buildings. Windows with Ultradur are 60% lighter in weight than metal ones, improving energy efficiency by 15-20%, and reducing indoor heating costs.
Meanwhile, BASF has innovatively applied Elastocoat® polyurethane composites to the auxiliary frames of windows and doors. The Elastocoat® continuous fiber reinforced composites provide a perfect auxiliary frame system for energy-efficient windows and doors for its outstanding low thermal conductivity while enhancing their mechanical properties, guaranteeing long service life for its excellent corrosion and aging resistance.
These days how to create a "sponge city", with strong water absorption capacity, has become a major challenge for urban life.
BASF Elastopave®, a polyurethane binder system mixed with gravel or stones and yielding air- and water-permeable pavements, provides a solution for future cities to prevent water build-up. Compared to concrete or tar, the high proportion of large and small stone pieces creates interconnected cavities. This feature facilitates water-permeability of roads and public spaces. Its porous structure can achieve sustainable management of rainwater, and absorb up to 1.1 liters of water per second per square meter given suitably absorbent ground.
Innovations based on chemistry require market-oriented research and development that focuses strongly on customer needs. Making ordinary plastics magical through innovation is what BASF's R&D team has been continuously working on.
"Our R&D success factors are creativity, efficiency and integration. Fostering creativity and creating the conditions necessary to achieve it are among the company’s most important tasks," said Dr. Martin Brudermüller, Vice Chairman of the Board of Executive Directors and Chief Technology Officer of BASF. "To do this, we need to intelligently combine the competencies of our global Research and Development Verbund while also taking advantage of our external networks."
The foundation of BASF’s innovation strength is its global team of highly qualified employees from various disciplines. In 2015, about 10,000 employees were working in Research and Development worldwide. The central research areas – Process Research & Chemical Engineering, Advanced Materials & Systems Research and Bioscience Research – serve as BASF’s three global research platforms. They are headquartered in the company’s main regions – Europe, Asia Pacific and North America. Together with the development units of the divisions, they form the core of BASF’s Know-How Verbund.
The Advanced Materials & Systems Research platform gathers nearly 200 employees at its Shanghai base. Its recent research focus is "Noise, Vibration and Harshness". Here, BASF experts are investigating the possibilities of minimizing unwanted noise and vibrations through material and component design.
With increasing urbanization, more and more people are living in confined spaces. Households not only have more electrical appliances, the equipment is also getting more powerful. The resulting noise and vibration needs to be minimized. An interdisciplinary BASF team of chemists, physicists and engineers is improving various polymer solutions that can be used to optimize frequencies in the range that can be felt and heard: from 1 to 20,000 hertz. Depending on the frequency range and the requirements, the team is able to change the design of components and/or the molecular or foam structure of the materials used (polyamides, polyurethanes, melamine resin foams) through computer simulations.
This is just a glimpse of BASF's technology blueprint that reveals the path of materials technology. The R&D and production of performance materials is only the beginning of the creativity. The innovative collaboration of material design, process design, modern-simulation technology and the global R&D integration is giving infinite magic to plastics. The changing properties of plastics are making our life more interesting and convenient.
Now, it is your turn to imagine …