Media
The new lightness in furniture construction
Kaurit® Light from BASF makes chipboard 30 percent lighter for modern interior design
Whether cupboards or tables, shelving or kitchen countertops – chipboard is now an indispensable feature of furniture production. It comes in various thicknesses, with different surfaces, for dry or moist rooms. Chipboard is extremely versatile and strong but unfortunately rather heavy too. Anyone who has ever tried manhandling a flat pack of shelving into their shopping cart will nod in agreement. The furniture industry has long been on the lookout for more lightweight boards.
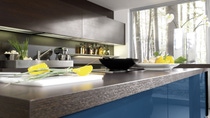
BASF has now developed a technology for an innovative wood-based material with the potential to revolutionize the furniture market: Kaurit® Light. "Wood-based panels made with the new technology weigh 30 percent less than conventional chipboard while offering the same strength," explains Dr. Stephan Weinkötz, project manager at BASF. "Kaurit® Light panels consist of wood chips, a foamed polymer and Kaurit® glue. For this new development we have combined and successfully utilized existing know-how from two of BASF's operating divisions," continues Weinkötz.
Conventional chipboard is made of three layers. The two outer layers have the smoothest possible surface and are therefore made of small wood particles. Between them is the middle layer making up two thirds of the total wood content. The larger wood chips incorporated in this layer make sure the panel can withstand loading. To produce the chipboard, the wood chips are first dried and then mixed with glue. They are then spread in three layers on top of each other on a conveyor belt and bonded together under high pressure at up to 250 degrees Celsius.
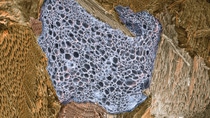
With the Kaurit® Light concept, about 200 kilograms of wood per cubic meter of wood-based panel are replaced by 15 to 25 kilograms of polymer. The polymer is added in the form of foam beads only in the middle layer. Although the panel now incorporates much more air, BASF's development scientists have succeeded in achieving practically the same strength as with conventional chipboard. The result is a versatile wood-based panel that now weighs only 450 kilograms per cubic meter compared to 650 kilograms with standard chipboard.
Furniture is easier to transport and assemble. Tables, armchairs or sliding doors are much easier to move. When moving house, lightweight furniture is easier to carry, which means fewer scratches and dents. The new material is also attractive for producers: chipboard manufacturers can fabricate the panels on their existing equipment without the need for large financial investment in new machines. Transport and handling costs are lower, less packaging material is required. Both of which also save energy and conserve resources. Furniture manufacturers can continue using the same metal fittings and connectors. Moreover, the lightweight material also opens up new possibilities in design and construction.
"The new wood-based panel is very suitable for industrial furniture production. This has been demonstrated in numerous practical trials conducted in our own facilities," says Michael Timinger, Managing Director of the company Nolte Holzwerkstoff in Germersheim, Germany. The Nolte group and BASF have cooperated in bringing the Kaurit®Light technology to market. Nolte has transferred the production process developed in BASF's laboratory to the industrial scale and is marketing the panel under the tradename "Rheinspan® AirMaxx®". For the medium term, the company is planning to produce around 200,000 cubic meters of these panels per year – equivalent to almost 9,000 kilometers of kitchen countertop. The affiliated company Nolte Küchen, one of Europe's largest kitchenmanufacturers, started supplying AirMaxx® countertops for the first time in July 2008. Nolte Küchen has meanwhile switched all countertops with a thickness of more than 38 millimeters to the new technology.
The environmental friendliness of the Kaurit® Light panels was also evaluated. An "Eco-Efficiency Analysis", a method developed by BASF and tested by the impartial German organization TÜV, showed that the eco-efficiency of the new wood-based panel at least as good as that of conventional chipboard. The entire lifecycle was analyzed – from production and transportation to usage and disposal.
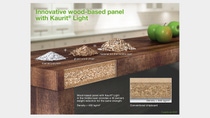
The Prospects
The Kaurit® Light technology from BASF is attracting great interest because it exactly meets the needs of the chipboard industry: a lightweight panel that can be produced and processed further on the existing equipment. Besides Nolte Küchen, flat-pack furniture manufacturer CS Schmal already has a furniture series based on this technology in its product range.
The market potential looks promising: in the medium term, the new material could replace about ten percent of all globally produced chipboard. Besides the furniture industry, other applications for the Kaurit® Light panels are conceivable, for example trade fair and prefabricated house construction, door manufacture, interior fittings for caravans, ships or containers.
BASF's experts are already busy optimizing Kaurit® Light. Their aim is to further reduce the density of the panels while improving the mechanical properties of the panel material. Furthermore, laboratory trials are already ongoing in which the Kaurit® Light technologie is being used in combination with other wood-containing or wood-like materials, such as wood fibers or shives.
The Info Box
From the tree to the chipboard
Chipboard is produced mainly from forest thinnings and waste wood. The wood is first chopped into fine chips, and then dried with hot air in large rotating drums. The chips are then separated according to size, mixed with glue and spread out on a broad conveyor belt.
Spreader machines ensure that the lower and upper layer consist of fine particles, while the larger chips end up in the middle layer. The conveyor belt transports the "chip cake" firstly to a cold pre-press and then on to the hot press which is up to 70 meters long. Here it is compressed under high pressure and at up to 200–250 degrees Celsius. The glue sets and hey presto – you've got chipboard. The press produces an "endless" panel ribbon which is finally cut down to the required lengths. It is then cooled and smoothed by sanding; the surface can be coated as desired.
In the Kaurit® Light panel, expanded polymer in the form of foamed beads is added to the middle layer. The beads fill the cavities, form additional binding sites for the wood chips and thereby enhance the panel's strength. They also generate counterpressure during compression, making for high compaction of the outer layers.
Kaurit® glue
As long as the 1930s, BASF began industrial production of urea based glues and impregnating resins. BASF was therefore the world’s first company to market synthetic wood glues with its Kaurit® brand and replace the formerly used glues. BASF has maintained its European market leadership to this day and cooperates with customers in developing innovative solutions. Every year, several hundred thousand metric tons of these glues are produced at Ludwigshafen site. 60 to 70 percent goes to the furniture industry, while the rest is used in floors and in the construction sector.