Media
Testing the limits in powder snow
Synthetic fibers with PolyTHF® stay flexible even in the cold - the ideal choice for winter athletes' functional wear.
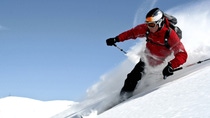
Crisp cold air, sparkling fresh-fallen snow and a swift board beneath their feet: that's all it takes to make winter athletes happy. As they speed down the slope at full tilt, swiftly ducking and weaving their way between the slalom poles and whirling up the snow, it can get pretty warm inside the ski suit, even when the temperature is freezing outside.
"A synthetic fiber with truly exceptional properties is needed if the clothing is to withstand not only the cold, but also the athlete's vigorous movements and perspiration," says Dr. Dieter Rodewald, Senior Manager Technical Services, BASF Intermediates in Asia. "Spandex fibers, made from the BASF intermediate PolyTHF, are ideally suited to these extreme conditions. The textiles are permeable to water vapor and retain their elasticity and flexibility even at icy temperatures, making the fabric feel like a second skin." Well into the 20th century, this was something people could only dream of. As they ventured out into the snow wearing a woolen jumper, velvet pants or fur jacket, they would feel their fingers - and their clothes - gradually getting cold. The natural fibers became rigid and the pants felt as stiff as a board. The advent of synthetic fibers in the nineteen-thirties put an end to this unhappy situation.
Spandex fibers are unfazed by frost or humidity. A look at the labels on different items of clothing will tell you that most textiles contain some spandex: you'll find it in socks, in long underpants and leggings, sweaters, T-shirts and jacket linings. In fabrics, spandex fibers always come mixed with other fibers, for example wrinkle-free and tear-resistant polyamide. Functional underwear such as ski underpants or jerseys contains five to ten percent spandex fibers. The spandex content in stretch jeans is about three percent. "Spandex fibers come in a variety of grades, for example customized for swimwear or high-quality outerwear applications," explains Professor Thomas Gries, Director of the Institute of Textile Technology at RWTH Aachen University. The more stretch a fabric is to have, the more PolyTHF the spandex fiber should contain. "The spandex content in functional wear, swimwear, jerseys and underwear is higher than in upmarket outerwear," says Gries.
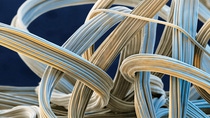
A low spandex content is sufficient to accommodate the normal range of everyday movements in trousers or shirts.
Athletes especially benefit from the superior elasticity of a spandex fiber, which consists of about 80 percent PolyTHF. With this percentage, even doing the splits would be no challenge for the pants. "Garments made of fabric containing spandex retain their fit even during extreme body movements," explains Gries. "Spandex fibers will stretch to as much as seven times their original length." Another advantage of these fibers is their long-term dimensional stability, which means they retain their extreme elasticity and always return to their original shape after stretching. Even when it's cold outside. Coping with skiers' perspiration is a job that demands a fiber immune to humidity. Step forward PolyTHF: "These fibers are the perfect solution for direct body contact applications, in sportswear or underwear for example," explains Dieter Rodewald. Moreover, the arrangement of atoms in PolyTHF molecules make them hard to digest for microorganisms. That's why microbes and mites shun spandex fibers - good news for allergy sufferers.
About 70 percent of the PolyTHF produced by BASF goes to the textile industry. It is also used to make highly abrasion-resistant hoses and films. Cable sheathing and dashboard films are major PolyTHF applications in the automotive industry. Another important usage for this versatile material is in rail track construction. The durably elastic molecular structure makes PolyTHF based plastics ideal for producing heavy-duty railroad bedding mats that dampen shock and vibrations. The benefits: less wear and tear, and less noise from passing trains. As a major constituent of polyurethane elastomers, PolyTHF is also used to manufacture long life wheels for skateboards and inline skates.
BASF is one of the global leaders in the PolyTHF business and expects future demand for this product to remain high. "As prosperity increases, so do textile sales," explains Rodewald. "Consumers can afford to wear the latest fashions and will part more readily with their old clothes."
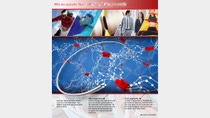
The Info Box
What is PolyTHF?
Polymere wie PolyTHF sind Makromoleküle, die sich aus vielen Untereinheiten zusammensetzen. Das weiße PolyTHF, das in der Textilindustrie eingesetzt wird, ist bei Raumtemperatur von wachsartiger Konsistenz.
How is PolyTHF produced?
The basic raw material of PolyTHF is typically 1,4-butanediol from which the cyclic tetrahydrofuran (THF) is formed in the presence of a catalyst. This is finally polymerized to open-chain polytetramethylene ether glycol (PTMEG) - or PolyTHF.
Why are spandex fibers so stretchable?
The extreme extensibility of spandex fibers is due to their molecular structure: Spandex consists of block copolymers, which means that a soft and flexible PolyTHF containing block is followed by a more rigid block, resulting in hard and soft segments. The rigid hard segments attract and cohere strongly with each other. By means of hydrogen bridges they form firm branch points between the individual macromolecules that are hard to break up. This is what gives the fiber its structure.
The flexible soft segments consist mainly of PolyTHF. As the forces of attraction between them are weak, they can arrange in coiled or extended form, making the fiber as elastic as a rubber band. The polymer structure is reminiscent of a chest expander. The handles of the expander correspond to the branch points of the hard segments, and the straps correspond to the soft segments. When you pull on the fiber, the flexible segments decoil and the fiber can expand. When the fiber is stretched, the soft segment arrange in parallel. But this expanded state is less stable, so the soft segments tend to coil up again: the fiber contracts and regains its original shape after being stretched.