Media
How rotor blades defy the forces of nature
Special epoxy resin systems and coatings make rotor blades of wind turbines resistant.
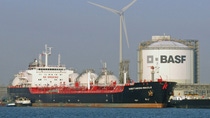
Wind energy is on the rise as a climate friendly source of energy. Ever larger rotor blades are constantly increasing the power output of modern wind turbines. The stresses and strains to which rotor blades of wind turbines are exposed at 90 meters above the ground are truly immense. Reaching top speeds of up to 300 kilometers per hour, forces are exerted on blade tips which make them bend for more than a meter. Weather conditions such as snow, rain, heat and UV radiation also take their toll on the blades.
BASF is supporting the manufacturers of these mighty machines by supplying innovative epoxy resin systems for highly resilient, fiber-reinforced components and coatings for rotor blades. The longevity of these wind energy plants is a key factor in improving the economic efficiency of wind power as a climate friendly source of energy.
The use of wind power presents a challenge for both technology and materials, on which it places the highest demands. Rotor blades need to be very tough and weather resistant to survive operating times of 20 years. Modern rotor blades are made of glass or carbon fiber mats bonded with epoxy resin systems to give them strength (see Info Box). "Basically, this works on the same principle as a two-component adhesive. The first component consists of synthetically manufactured resins and the second is the hardener, or curing agent. When mixed together, they crosslink with each other," explains Dr. Gregor Daun, Head of the BASF Team for Development and Marketing of Epoxy Systems for Composites.
This two-component system of epoxy resins and hardeners is marketed by BASF under the name Baxxodur®. The manufacturing process for large rotor blades can be speeded up significantly using this product. To ensure that the molds for the blades are filled completely and quickly, the hardener initially reacts slowly. When warmed after filling the mold, the hardening rate increases, leaving the mold free more rapidly to produce the next blade. This allows rotor blade manufacturers to speed up this process step by as much as 30 percent.
The time saving also reduces manufacturing costs while simultaneously increasing production output, making electricity generation by wind power more cost effective and even more competitive. This innovative system has been approved by certification agencies for wind energy plants including the worldwide leading Germanischer Lloyd AG.
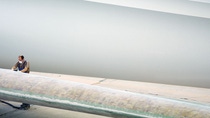
Another important factor besides the technical design of the rotor blades is how well their coating withstands environmental impacts. "Imagine a car driving constantly at 200 kilometers per hour through the rain: signs of damage would start to appear after a few months. A rotor blade is exposed to even harsher conditions for between ten and twenty years – without suffering harm," says Dr. Harald Müller, Manager Development for Industrial Coatings at Relius Coatings GmbH. The special coatings developed by BASF's subsidiary are flexible to minimize the risk of stress cracking and do not flake off when the blades bend. Quite something, considering that the tips of a rotor blade can vibrate back and forth for more than a meter.
"The high-tech coatings are based on the special plastic polyurethane. They are highly abrasion resistant, withstand UV radiation and are solvent-free," is how Müller lists the advantages. The topcoats are matt to prevent the sun being reflected from the rotor blades which could pose a potential hazard for air traffic. The coating systems marketed under the name Oldodur consist of several products, such as gelcoat, surfacer, edge protection and topcoat. More than 25,000 rotor blades with Relius coatings are now spinning in the wind and have been defying the forces of nature for years.
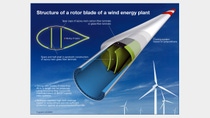
The Prospects
Wind energy is continuing its unbroken global success story. At the end of 2008, the World Wind Energy Association (WWEA) reported that wind energy plants with a total capacity of 120 gigawatts (GW) were installed worldwide. This represents a growth rate of almost 30 percent over the previous year. These plants supplied about 1.5 percent of global electric power consumption.
The WWEA also estimates that by 2020 wind energy could supply at least 12 percent of the global demand for electric power. Moreover, advances in technology are expected to reduce the costs even further by then, adding economic competitiveness to the ecological benefits. Wind power as part of a mix with other energy sources will then make a sustainable contribution to energy supply in Germany and the world.
At present two trends dominate the development of wind energy: turbines are growing ever larger in order to generate more power, and wind power is moving offshore. The first plants with a rated output of 5 to 6 megawatts (MW) of electricity per hour are already on the market. The dimensions are colossal: rotor diameters of about 127 meters and blade lengths of over 60 meters. And still no end in sight: design concepts already exist for 70 meter blades and test rigs for blades up to 90 meters long. Rotor blades are constantly increasing in size because a blade of twice the length covers an area four times the size and can therefore capture four times as much energy. The target for 2020 is 20 MW. This is precisely the vision being pursued by the European "UpWind" project, launched in 2006 and scheduled to run until 2011. "UpWind" is the flagship project for European research cooperation in the field of wind turbine development. The aim is to further improve the competitiveness of wind power compared to other energy sources. Existing technologies will be refined and innovative technical approaches and design methods evaluated. The new giants are intended mainly for offshore wind farms where the wind blows more strongly and constantly.
The Info Box
How are wind turbine blades produced?
Manufacturing rotor blades for wind turbine plants is a demanding business: the largest and most modern blades are made from glued glass and carbon fiber mats into which epoxy resin is injected under vacuum. The high-tech design ensures the exceptional level of stability and flexibility that is required while keeping the blades thin and lightweight.
The vacuum infusion process by the sandwich construction method is now a widely used technique in rotor blade production. Blades are produced along the following lines: first, the mold consisting of two heatable half-shells is charged with a release agent. The shell is then lined with glass fiber mats and other reinforcing material. After that, special tubing from which the mixture of epoxy resin, hardeners and additives will flow is placed in the mold. This is followed by a plastic film that seals the entire unit airtight. In the next step, all the air between the mold and the film is withdrawn. The resulting vacuum sucks the fluid resin and hardener mixture through the tubing into the mold and saturates the reinforcing material. The advantage of this process is that the fibers are homogeneously saturated, ensuring high quality of the resulting components and their reproducibility. The rotor blade halves are then hardened at about 70 degrees Celsius. This is followed by the "marriage" of the two components: gluing the two halves of the blade together. Before the multistage coating process the surface of the rotor blade is grounded to remove the release agent.
A gelcoat applied to the rotor blade in the first step protects it against environmental influences such as moisture and light. Small irregularities on the surface are smoothed with the surfacer. Edge protection that guards against wear and a topcoat are applied last after the blades have been coated.