Sustainability
It’s the (many) little things that count: Creating chemistry without Wasting Energy
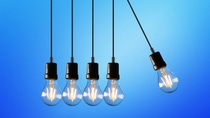
On October 11th, 2018 BASF South East Asia Pte Ltd won the top prize for Excellence in Energy Management at the annual Energy Efficiency National Partnership (EENP) Awards in Singapore. The award recognizes companies which have achieved excellence in energy management.
Energy management is more than a buzzword. It’s a set of strategies crucial to running a profitable manufacturing business. And it’s a fundamental competency for companies committed to reducing carbon emissions in light of the growing climate threat.
BASF has a long-standing commitment to energy efficiency. It pioneered the Verbund, a system of inter-linked chemical production processes designed to channel the excess heat, and waste product, from one process to feed the next. The Verbund saved BASF about 19.2 million megawatt hours of power in 2017 – which translates to 3.9 million metric tons of CO2 that were not released into the environment.
"Creating chemistry for a sustainable future is at the heart of what BASF does," said Dieter Vanneuville, site manager, Performance Chemicals, Jurong Island, BASF South East Asia Pte Ltd. "Our Verbund principle, which is about intelligent interlinking of production plants, energy flows and infrastructures, makes a critical contribution to this commitment."
Many companies would like to save energy, money and carbon. How is it done? The process starts with extensive homework: investigation of where new technologies, processes or data-enabled information could enable better efficiency. Often there is no one right answer: there are many. And designing them in an additive fashion can accelerate the process.
The strategies BASF implemented at Jurong Island included by-passing an entire heating and cooling step, upgrading chillers, and using real-time data to optimize energy use. Targeted training enabled energy managers on site to cultivate a culture of energy stewardship among colleagues. Adjustments to maintenance and processes played a key role as well.
The results of these cumulative strategies speak for themselves. Over 5 years the site reduced specific energy consumption by 40%, while production levels increased. It was awarded the International Standards Organization (ISO) 50001 certification in 2017, a global standard for energy management. Mr Vanneuville said: "As a company, we will continue to work towards achieving 90 per cent coverage of our primary energy demand through certified energy management systems at all relevant production sites by 2020."