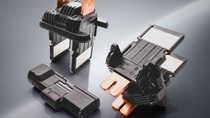
Less electro-corrosion, more color: New Ultramid® Advanced N for high-voltage connectors in electric cars
BASF is now complementing its polyphthalamide (PPA) portfolio by Ultramid® Advanced N3U42G6, a polyamide 9T with non-halogenated flame-retardant, which minimizes electro-corrosion of metal contacts in electric and electronics (E&E) parts for e-mobility. The PPA increases the safety and durability of high-voltage (HV) connectors in e.g. inverters, DC-DC converters and batteries of electric cars. Due to its high strength and stiffness over a broad temperature range, its outstanding chemical resistance and dimensional stability, the Ultramid® Advanced N grade enhances the robustness and reliability of thin-walled HV connectors meeting growing industry needs for halide-free E&E components used in warm and humid conditions. The new Ultramid® Advanced N3U42G6 is available in uncolored with UL-certified masterbatches but also as pre-colored version with high color stability for easy processing and excellent color retention after heat ageing.