Who we are
Florina Corina Patcas
Without them, neither photosynthesis nor respiration nor energy production from food would be possible: catalysts. In the form of enzymes, they enable almost all vital chemical reactions in living organisms. They also clean the exhaust fumes of our cars. Catalysts are also irreplaceable for the production of many chemical products. But to this day, catalysts pose many questions to science, because little is known about the details of how they work. Florina Corina Patcas has been researching catalysts for 25 years and is deciphering their secrets piece by piece.
Catalysts are substances that influence the reaction rate of a chemical reaction without being consumed themselves. How exactly they do this is often still a "black box" in complex reactions. How do you still develop catalysts that work precisely?
In principle, research on catalysts works in a similar way to a dating portal. Little is known about why exactly the chemistry between two people is right and why they fall in love. However, there is a lot of empirical data as to which profiles and properties harmonize particularly well. Algorithms can learn from this amount of data and predict who might be a good match. It's a similar story in catalysis research. We do a lot of experiments, change the composition of the catalysts, and evaluate the results. Through machine learning and mathematical models, we can identify patterns in the data that improve and evolve catalysts. We don't have to understand every detail. It is important that the result is right.
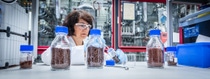
They are small and inconspicuous, but play an essential role in the efficient and resource-saving manufacture of many products: Catalysts.
Is there a moment when you felt like you were looking right into the black box of catalytic converters?
Yes, but it was different from what you imagine. Through my scientific studies, I was used to taking the rational path, i.e., solving problems and finding optimization approaches by precisely penetrating cause and effect. My big eye-opener was finding out you can optimize processes or a chemical reaction even without a complete understanding of all the interrelationships – if you have collected enough data. Artificial intelligence and machine learning make this possible. That is, it is not at all necessary to completely x-ray the black box. We can also optimize both the catalysts and the production processes in which they are used. We have developed an app for our customers with which they can adapt and optimize their process parameters according to their framework conditions. And for catalyst development, we use design-of-experiment (DOE), i.e., statistical design of experiments, coupled with data analysis to obtain as much information as possible with the minimum amount of experimentation.
What are you currently working on with your laboratory team at BASF?
We continue to develop catalysts for styrene production for BASF Catalysts and our customers from various industries. Styrene is an important raw material for producing plastics, such as the insulation of buildings, for example. The complex reaction to produce styrene would be neither economical nor sustainable without a catalyst, because half of the starting materials would be split into smaller molecules and rendered unusable instead of reacting to the desired product.
With the help of our catalysts, 95 percent of the starting material ethylbenzene is converted into the desired product. Catalysts are therefore crucial for conserving our resources, producing as little waste as possible and reducing energy consumption and thus CO2 emissions in the production process. Through them, a reaction takes place even at lower temperatures. In addition, we can use catalysts to influence the properties of the end products. We make the entire chemical process better with catalysts, which is a nice feeling.
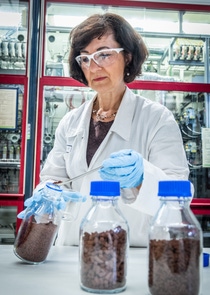
Florina Corina Patcas has been researching for 25 years on revealing the secrets of catalysts.
Catalysts are crucial for conserving our resources, producing as little waste as possible and reducing energy consumption and thus CO2 emissions in the production process.
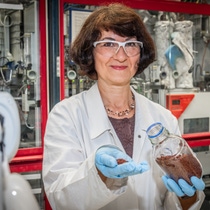
Hundreds of tons of catalysts are needed in large production plants.
What does such a catalyst for the styrene plant look like?
The cats, as we call the catalysts here in the laboratory, are solid, small cylindrical grains. They essentially consist of iron oxide, i.e., in principle rust, and other elements in the form of salts, carbonates and hydroxides. The trick is to optimally combine the ingredients and the amount for the desired effect. For styrene production, 100 to 700 tons of the catalytic converters are needed in a plant, which then ensure an optimal course of the chemical reaction for several years.
How did you come to want to become a researcher? And why do you like working with catalysts so much?
In my home country, Romania, it was a matter of course that girls are also good at science. I think that's very important, because it doesn't create any fear of contact with science subjects in the first place. I decided to study chemical engineering because I have always been interested in practicality. The more I understood how to control and improve catalysts, the deeper I wanted to dig into the matter, because I realized that I was still scratching the surface and there was so much to discover. It was as if I had just eaten the appetizer – I wanted to know what was coming. As a postdoc and lecturer, I spent several years researching at the Karlsruhe Institute of Technology before embarking on an expert career at BASF in 2008. Here I can do exactly what suits me best that I enjoy the most – researching, discovering and helping to optimize catalysts for practical use.
Assuming you had unlimited resources, what topic would you be researching? Would you try to fully unravel the secrets of catalysts?
As a university researcher, I would definitely try to understand everything that happens in the catalyzed styrene reaction. But that's a pretty big task and even though it would, of course, be very exciting for me as a researcher, it doesn't help us fast enough in the development of catalysts. We are already doing this very well with a certain pragmatism and mathematical models. As an industrial researcher today, I would prefer to put the resources into two topics that will help us as a society move forward: the electrical heating of reactors and plastics recycling. I am convinced that science has always been able to solve problems and that it is still able to do so today – provided it is given the opportunity.
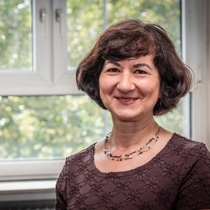
With her experience, gut feeling, and perseverance Florina Corina Patcas finds answers to the many questions catalysts pose to science.
I am convinced that science has always been able to solve problems and that it is still able to do so today – provided it is given the opportunity.
Further Links
- Becoming a Smart Scientist yourself? The world needs innovation. We need you. Have a look at open positions.