Media
BASF at The Battery Show Europe 2024: The chemistry to power up sustainable mobility
- Enabling advancements for next generation battery systems
- Solutions for elevating protection and performance
- Improving efficiency while lowering the environmental impact
BASF will be showcasing its innovative power solutions at The Battery Show Europe 2024 in Stuttgart, Germany. Taking place between June 18-20, Europe’s largest industry event brings together the battery and electric vehicle (EV) community combining real-world commercial and technical aspects. As a leading solution provider for various battery applications, BASF will be presenting its range of products specifically targeted to enable advancements of battery technologies and future automotive mobility at booth 10-C110.
Innovative batteries with BASF battery materials and recycling solutions
Battery materials are at the heart of lithium-ion batteries as they significantly determine their performance. BASF offers one of the broadest cathode active material (CAM) portfolios with a well-established position in key CAM technologies like NCA (nickel-cobalt-aluminum-oxide), NCM (nickel-cobalt-manganese-oxide) and LCO (lithium-cobalt-oxide). By leveraging industry-leading R&D platforms and passion for innovation, BASF Battery Materials already today looks into future CAM products ranging from cost-efficient manganese-rich solutions to high-performance ultra-high nickel products, high-performance LMO (lithium manganese oxide) as well as CAM dedicated for sodium-ion applications. BASF also provides base metals sourcing and management to ensure a stable, responsible, and sustainable supply chain for the production of cathode active materials.
In addition, BASF’s portfolio also includes comprehensive battery recycling solutions in order to offer its customers recycled metals with a lower carbon footprint compared to virgin metals, thus helping to meet regulatory requirements. In March, BASF started operating its prototype metal refinery for battery recycling in Schwarzheide, Germany, to further improve the process of recovering valuable metals such as lithium, nickel, cobalt, manganese and copper from end-of-life batteries and battery production scrap. It complements BASF’s existing CAM plant and the battery recycling plant to produce black mass, which is scheduled to start operations later this year. The portfolio addresses various customer requirements, including closed loop offerings and digital end-to-end solutions to set up regional recycling value chains.
Products for high voltage connectors
With the Ultramid® DC grades (Durable Color), BASF offers a broad portfolio of engineering plastics for the eMobility market – even in the flame-retardant sector. High technical requirements from the industry require innovative solutions based on PA66 and PA6. In the case of already proven Ultradur® (PBT) products, color stability can be largely guaranteed, especially in orange (RAL 2003) which is in high demand in the industry. In addition, some grades are specially optimized for laser markability with high contrast values.
New advancements in busbar technology for high voltage power electronics
Busbars play a crucial role in providing electrical isolation and connecting various components in high voltage power electronics. In the case of battery electric vehicles (BEVs), busbars serve as a connection between the inverter and the electric motor or play an important role inside the HV battery pack. This requires a high level of electrical insulation. In case the plastic is used in a busbar holder function, a certain stiffness and strength must be ensured. On the other hand, being used as a busbar sheathing for HV in the battery pack the orange signal color is a must-have. Additionally, these plastics need to show excellent temperature resistance and electrical isolation properties even after harsh aging. All Ultramid® and Ultradur® grades for busbars meet these requirements.
Furthermore, the use of thermoplastic polyurethane (TPU) Elastollan® in busbar applications offers stronger resistance to thermal cycling due to optimized thermal linear expansion. This reduces the risk of cracks occurring during temperature changes which increases the safety standard.
Materializing eMobility ambitions with Elastollan® (TPU)
The increasing demand for a broader charging infrastructure for Electric Vehicles (EV) is driving the need for robust and lasting charging cables at home and on the road. Those cables need to withstand harsh environmental conditions and be rugged enough to hold up over time. To cope with these challenges BASF's TPU Elastollan® are particularly suitable for cable sheathings ensuring a strong resistance to UV, weathering, ozone, and microbes. To make the charging process safe, cables should be made flame retardant without halogens, and must be coilable and flexible. Elastollan® further sets itself apart from other materials by being recyclable.
Introducing Ultramid® Expand: A particle foam for electric vehicle batteries
Ultramid® Expand stands out with its exceptional heat resistance and mechanical properties, making it an ideal choice for high-temperature applications, withstanding temperatures above 120°C. Furthermore, it exhibits outstanding chemical resistance to automotive fluids, ensuring long-lasting durability and reliability. Key feature of this new foam is its drop-in compatibility with existing expanded polypropylene (EPP) tools, making it a straightforward and cost-effective solution for manufacturers. The foam is also compatible with cathodic dip coating and can be easily recycled, highlighting BASF's commitment to innovation and sustainability in the plastics industry. The applications of this particle foam are diverse and include battery protection, battery cell holders, and complex 3D geometries.
Long-lasting protection and performance with the right surface treatment and coatings
For optimal protection and enhanced performance across a wide range of platform designs and battery systems, BASF offers a range of innovative coating solutions. These solutions, spanning from pretreatment to e-coat, are instrumental in achieving the desired outcomes. A standout technology is Chemetall's eco-friendly Oxsilan® thin film technology, which applies a uniform and protective layer on metal surfaces. When combined with CathoGuard® technology, this unique combination significantly bolsters corrosion protection, thereby improving the durability and performance of battery systems. BASF's CathoGuard® portfolio further ensures comprehensive corrosion protection for multi-metal car bodies and components, including battery covers, ensuring that all vital components remain shielded from the damaging effects of corrosion.
In a next step of innovation, Chemetall is developing non-chrome surface treatment solutions for copper foil, which is used as anode current collector. Removing hexavalent chromium from the passivation process promotes both a safer and more sustainable future. Additionally, BASF is developing protective interfacial coatings for electrode foils, an exciting advancement towards safeguarding cathodes and anodes, whilst also enhancing performance. Such coatings help to enable novel battery systems, for example Lithium solid state, or Lithium-Sulfur cells. BASF’s portfolio of surface treatment and coating solutions therefore not only provide corrosion protection but also can enhance performance and lifespan of battery cells, enabling development of further improved battery systems.
Smoother processing with the right additives
High-performance processing additives empower battery cell manufacturers to overcome challenges in all aspects of battery cell manufacturing, such as conductive slurry preparation, improved performance and enable an enhanced runability on the coating lines. BASF’s portfolio of innovative processing additives provides suitable solutions to overcome current and future requirements and challenges, enabling a smoother and more efficient manufacturing experience.
Overcoming the limits of lithium-ion batteries
To achieve cleaner and more efficient batteries the need for high-performance materials increases. Despite improvements over recent years Lithium-ion batteries still offer room for technical improvement, particularly in terms of charge capacity. Licity® binders have been designed to overcome the current limits of the technology. The waterborne binders possess high colloidal stability, making them highly compatible with cobinders like CMC. In addition, they exhibit exceptional processability and superior coating behavior, as well as excellent mechanics and electrochemical performance. With these unique properties, Licity® binders enable an increased performance for Lithium-ion cells, contributing to the development of cleaner and more efficient batteries.
Sealant component for batteries and electronics
OPPANOL® is a highly versatile polyisobutylene that is an excellent choice for enhancing the performance and efficiency of next-generation batteries in automotive applications. By using OPPANOL® as a binder, the risk of electrochemical disturbances is significantly minimized. Its chemical inertness ensures that it does not react with the electrolyte or other components of the battery, preventing the formation of undesirable byproducts or detrimental reactions that could compromise the battery‘s performance. In addition, high molecular weight OPPANOL® exhibits superior elasticity and elongation. This means that it can effectively accompany the mechanical expansions and contractions during battery operation, reducing the risk of physical damage or premature failure.
Extensive portfolio for the automotive industry
Modern vehicles are already heavily based on chemical products and solutions. BASF is the world’s leading chemical supplier to the automotive industry. The company cooperates closely with customers worldwide through its network across the regions. Supplying functional materials and solutions the company enables vehicles to be built more efficiently and with a lower environmental impact. But chemistry is set to play an even greater role in the future as it contributes significantly to solving the mobility challenges ahead. BASF expects the chemical content of cars to increase further as a result of developments in automotive industry with regard to sustainability, electromobility, new interior concepts, safety and comfort. Leveraging its broad portfolio of innovative technologies and solutions, BASF strives to empower automotive manufacturers and suppliers to create the next generation of vehicles that are safer, more efficient, and more environmentally friendly.
Visit us at The Battery Show Europe 2024 - Booth 10-C110
https://www.thebatteryshow.eu
More information on BASF’s solutions for the automotive industry and electromobility: www.basf.com/automotive
About BASF and the automotive industry
The automotive industry is one of BASF’s key customer industries. In 2023, BASF’s automotive driven sales totaled €15.4 billion – representing approximately 22% of BASF Group’s sales. BASF supplies and develops functional materials and solutions that enable vehicles to be built more efficiently and have a lower environmental impact, whatever powertrain technology they use. BASF’s product range includes for example plastics, coatings, catalysts, automotive fluids as well as battery materials. With such an extensive range of products, BASF is the world’s leading chemical supplier to the automotive industry. BASF cooperates closely with customers all over the world through a network embracing Europe, Asia-Pacific, North and South America as well as Africa. Further information on BASF’s solutions for the automotive industry is available at automotive.basf.com.
About BASF
At BASF, we create chemistry for a sustainable future. We combine economic success with environmental protection and social responsibility. Around 112,000 employees in the BASF Group contribute to the success of our customers in nearly all sectors and almost every country in the world. Our portfolio comprises six segments: Chemicals, Materials, Industrial Solutions, Surface Technologies, Nutrition & Care and Agricultural Solutions. BASF generated sales of €68.9 billion in 2023. BASF shares are traded on the stock exchange in Frankfurt (BAS) and as American Depositary Receipts (BASFY) in the United States. Further information at www.basf.com.
P-24-214
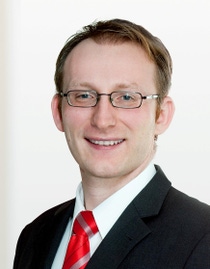