Careers
Automation technology engineers
We work on solutions for challenges of tomorrow
Do you want to change the world together? With topics such as sustainability, energy transformation and Industry 4.0 a diverse and exciting range of tasks awaits automation engineers at BASF. And that´s not all! With their innovations, they actively contribute to a sustainable future and bring BASF a step closer to its ambitious goal of net zero CO2 emissions worldwide by 2050. For instance our engineers work on energy-efficient plants, the use of renewable energies and innovations in battery materials and electromobility.
Attractive working environment
Requirement profile
Trainee programs: Our entry for young professionals
Our E&I engineers tell their stories:
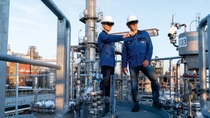