Média
3 questions for Nikolaus Raupp
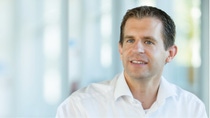
Since 2013, BASF has offered its customers the option of replacing fossil feedstock in the Verbund with renewable resources. BASF project manager Nikolaus Raupp, PhD, explains how the biomass balance approach certified by technical inspection board TÜV SÜD works.
There is a growing interest in the use of renewable raw materials – also in the chemical industry. How can BASF’s biomass balance approach contribute to this?
Nikolaus Raupp: With this process, renewable raw materials can be used as feedstock in our existing Production Verbund and then allocated to the respective sales products. The principle is similar to that of “green energy” tariffs, where the electricity coming out of the socket does not necessarily come from renewable energy. The important thing, though, is that the volume of renewable raw materials in the system overall is correct. Furthermore, an advantage of this solution is that the product will reliably offer the same level of quality. The unique feature is that the volume of fossil raw materials needed for production can be replaced by renewable resources.
Depending on the customer’s preferences, up to 100 percent of the fossil feedstock needed can be replaced with renewable raw materials. How can you prove this?
We can calculate all the way back along the raw material chain in the Production Verbund. Here at the Ludwigshafen site, we have around 200 interconnected plants across an area spanning 10 square kilometers. And we can calculate exactly which of the various raw materials go in and come out of each of these plants. If a customer buys one metric ton of a biomass balance product, we replace the corresponding volume of fossil feedstock with renewable raw materials. TÜV SÜD carefully monitors these calculations. Even though the raw material prices are higher, there is a lot of interest in our biomass balance approach – especially in the construction sector, the furniture industry and among producers of hygiene products. There are now more than 40 BASF products, such as plastics or superabsorbents for baby diapers, certified according to this approach. And more are being added all the time. A recent example is the use of binders sold under the Acronal® brand, which were processed by the architectural coatings producer DAW to make its newly launched Caparol and Alpina interior paints.
Renewable raw materials are not necessarily always sustainable. What standards are applied?
The TÜV SÜD standard applied here stipulates that the process must use only raw materials that meet certified sustainability standards. It is important to BASF that the highest-possible share of raw materials is derived from organic waste, such as agricultural residues.