Média
Innovative uses for 3D printing
Although 3D printing is not a completely new phenomenon – the first patent was awarded in 1986 – it is evolving rapidly: New applications appear almost daily, from all around the world, in fields as diverse as medicine, consumer products and construction.
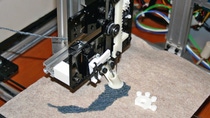
Cuddly teddy bears straight off the printer? The Disney Research Team in the United States has found a way to print in wool, meaning that alongside hard, precise objects, this new technology can now also be used to create things that are soft and squeezable. The printer builds up the yarn in layers, producing a unified mass that looks and feels like felt. In collaboration with a team from Carnegie Mellon University’s Human-Computer Interaction Institute in Pennsylvania, USA, they even printed a moveable teddy bear arm.
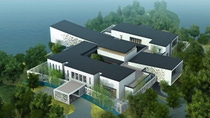
The Chinese construction company WinSun Decoration Design Engineering has not only shown it can quickly and cheaply produce houses using a 3D printer and recycled concrete material – printing 10 houses in one day – it has now gone on to print an entire 5-story apartment building and a standalone villa. The aim is to be able to construct homes at affordable prices for the Chinese market. The smaller houses cost just around €4,500 ($5,000) to produce.
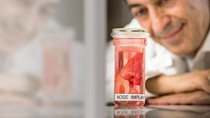
While 3D printing is already widely used in dentistry to print teeth and parts of jawbones, U.K. scientists have developed a process for printing ears out of synthetic material for children with severe disfigurements. Replacement ears are normally made manually. 3D printing simplifies the process. In the first clinical trial of its kind, a team at University College London has been carrying out tests and is months away from implanting the printed ears into patients. The team is also working on printed noses, tracheae, tear ducts or blood vessels.
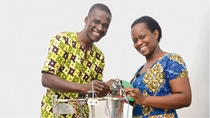
If 3D printing is set to revolutionize manufacturing, Afaté Gnikou from Togo is making sure that no one needs to be left out for lack of resources. Together with a team at the Woelab Fab Lab in Lomé, he has developed the first 3D printer made entirely of electronic waste. Tailored for the African market, the W.AFATE printer is now in series production and won first prize at the international Fab Lab Conference in Barcelona in 2014.
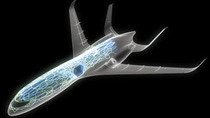
Aircraft manufacturer Airbus wants to use 3D printing to create new airplane structures that mimic the design of bone or skeleton – strong, flexible forms that weigh significantly less than those built with traditional manufacturing processes. Starting with tiny carbon nanotubes that “grow” inside the printer, huge complex structures can be created quickly with very little material waste. The weight reduction from the lighter materials would lead to huge fuel savings.

With 4D printing, Australia has gone one step further and added a new dimension: time. Researchers at the University of Wollongong have succeeded in printing a valve that opens and contracts over time in reaction to surrounding water temperature. The achievement opens up myriad possibilities in areas like medicine, construction and robotics, for fully functioning devices that come straight off the printer – no assembly required.
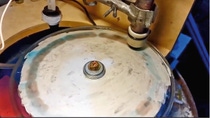
3D printing in metal is pricey. But Argentinian engineer Gastón Accardi has come up with a prototype of a metal printer that cost him less than €2 to make. Essentially a marker filled with a copper acid solution, it uses the concept of electroplating to build up 3D objects layer by layer in different types of metal. Although still a little slow, the machine could one day be a boost to small businesses.
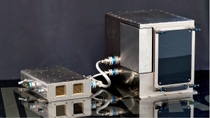
With visions of life on Mars firing our imaginations, 3D printing is seen as an offworld solution to everything the human needs, from food to shelter. But without gravity, how do you prevent the material you are printing from just floating away? Working with NASA, U.S. company Made In Space has developed Zero G, the first 3D printer designed to operate in zero gravity. Launched into orbit in 2014, it is serving as a test bed for space manufacturing technology.