可持续发展
产品碳足迹
一个产品在其生命周期内排放多少温室气体?过去几年间,这个问题变得愈发重要。“产品碳足迹”可以给出答案。
产品碳足迹统计了一个产品在其生命周期各个阶段产生的所有温室气体排放量。例如,“摇篮到大门”(部分)的产品碳足迹,指的是从资源开采、前体制造、成品制造,到成品离开公司大门过程产生的碳排放。而“摇篮到坟墓”的产品碳足迹覆盖一个产品的完整生命周期,包括产品使用阶段和其报废后产生的碳排放。
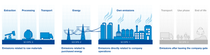
Processing
The emissions related to processing can vary greatly depending on the purchased raw material. Generally upstream commodities (oil, gas, base chemicals) cause rather low processing emissions, whereas fine chemicals/specialties (resins, precious metals) carry higher emissions due to the complexity of their production routes.
Transport
For most raw materials sourced by BASF, emissions from transportation are relatively small in comparison to the total PCF (<5%). This is due to the fact that BASF’s raw materials are mostly transported in bulk and in rather large quantities, leading to low specific emissions.
Energy
For BASF, the purchase of electricity at sites that are not yet supplied by renewable electricity is responsible for the largest share of Scope 2 emissions. In some cases, BASF is also supplied with steam for its processes by other companies close by. The specific emissions (kg CO2/kWh) depend on the energy provider's energy mix.
Own emissions
For BASF, the most important drivers are process emissions from our production plants (CO2, CH4, N2O, HFCs), emissions from our power plants to produce electricity and steam for the Verbund sites, as well as emissions from the disposal of waste streams in our waste treatment facilities.
Transport
Transport emissions caused by the product after it leaves BASF’s gate. BASF can calculate data for the transport from BASF to its direct customers on demand.
Use phase
Emissions associated with use of the BASF product, either as is or incorporated in a customer's product. Since the range of application for BASF’s products is very diverse, use phase emissions of a product vary according to its usage.
End of life
Emissions from waste disposal and treatment of BASF’s products at end-of-life. End-of-life treatment methods include e.g. recycling, incineration or landfill, resulting in different specific emissions.
Extraction
The emissions caused by the extraction of materials from the environment for further use, e.g. mining of coal, production of oil or natural gas, cultivation and harvesting of crops.
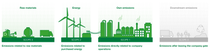
Raw materials
BASF creates transparency and increases accuracy of its raw material related emissions by inquiring suppliers’ PCF information for procured materials. Based on this, PCF will become an additional criterion for targeted procurement of raw materials with lower carbon footprints. In parallel, BASF introduces circular feedstocks with biogenic or recycled characteristics into the value chain. The high raw material impact on BASF’s PCF (on average ~70%), makes these activities an important reduction lever.
Energy purchase
The largest reduction lever for Scope 2 emissions is the sourcing of green electricity (GE) which reduces emissions to nearly zero. This can be achieved via direct procurement from the energy provider or through purchase of renewable energy certificates. An additional lever is the utilization of green steam, however here, markets are still in development.
Own emissions
The interconnected production of BASF (Verbund) helps to produce efficiently and reduces waste. Emission reductions are driven by continuous process improvements, use of biofuels, and the large transformation projects (e.g. e-furnace, methane pyrolysis, heat pumps, carbon capture and storage). To cover the energy demand of those projects BASF invests in renewable energy production.
Downstream emissions
Scope 3 downstream emissions of BASF’s are mainly governed by the product’s carbon content and the method of disposal. While incineration in waste treatment plants leads to emissions equivalent to the carbon contained in the product, end-of-life emissions are greatly reduced if the waste is recycled into new products (e.g., by depolymerization or pyrolysis for ChemCycling®).
在巴斯夫不断努力争取在2050年前实现二氧化碳净零排放的同时,越来越多的客户在采购决策时将环保纳入考量之中。因此,巴斯夫开发了一套数字化解决方案,用来计算其 45,000 款在售产品“摇篮到大门”的碳足迹。巴斯夫将提供所有全球在售产品的碳足迹数据。因此,客户也将获得有价值的信息,知悉采用巴斯夫的材料将为其业务活动和成品带来多少碳排放量。
巴斯夫产品碳足迹的计算基于其自身生产装置的温室气体排放量,以及所采购的原材料和能源的高质量平均数据。一旦供应商能提供我们所采购原材料的具体碳排放数据,巴斯夫将逐步替代这些平均数据。
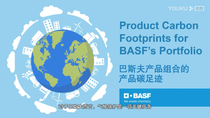
减少产品碳足迹的另一选择
产品碳足迹为客户提供了避免温室气体排放的宝贵信息。目前,我们已经通过使用可替代原材料为客户创造附加值,从而帮助客户减少其产品的碳足迹。
例如,巴斯夫的生物质平衡方案,将有机废料与植物油中提炼出的可再生原材料,代替化石燃料,用于一体化生产体系,并精准分配至相应的在售产品中。物质平衡方案的另一应用案例是巴斯夫的“化学循环”(ChemCycling™)项目。2020 年,巴斯夫为客户提供了在生产初始阶段使用“化学回收”废塑料所得原材料而制成的首批商品。与纯化石原材料生产的产品相比,巴斯夫使用这两种方法制得的商品性能相同,但更低碳。
- 了解更多关于生物质平衡 (英文)的信息
- 了解更多关于 “化学循环”(ChemCyclingTM)项目的信息
推动国际标准和规则的确立
巴斯夫产品碳足迹的计算遵循产品生命周期评估(ISO 14044)、产品碳足迹(ISO 14067)的通用标准和《温室气体协议产品标准》。
然而,这些标准没有具体规定如何准确计算每一个产品的碳足迹。在缺乏此类标准的情况下,由不同公司制造的相同产品,其碳足迹还不能直接进行比较。为了创造公平的竞争环境,巴斯夫致力于在化工行业推出基于产品的碳足迹计算指南,创造业内公平竞争环境,使对比产品碳足迹成为可能。
如何进行更全面的可持续发展评估
产品碳足迹使产品的温室气体排放量变得透明。同时,这只是我们更为宏大的可持续发展图景的组成部分。我们采用环境、经济和社会标准对产品进行全面的可持续发展评估。如果您希望有更全面的了解,我们建议您使用多标准评估工具,例如我们的生态效益分析(英文)。
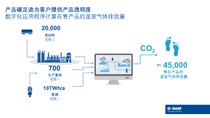