Magazine
It’s all about changing mindsets
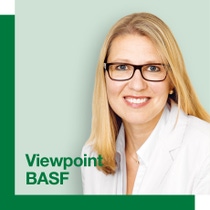
Talke Schaffrannek
is Director of Circular Economy at BASF, Ludwigshafen, Germany. Her previous responsibilities include applied sustainability, business development in Asia, diversity and inclusion, and product management. She has an MBA from Mannheim Business School, Germany, and Tongji University Shanghai, China.

The core of a circular economy, for me, is to decouple growth from resource consumption. We need to shift to smarter growth models that do not rely on finite resources and instead turn waste into raw materials. Together with my team here at BASF, we recently launched a circular economy program with concrete actions in three areas: new circular feedstock (recycled and renewable); new material circles (direct recycling loops and enabling circularity); and new business models (digital and service-based).
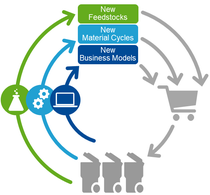
New business models
We develop new business models that meet the needs of our customers. Digital innovation will play a key role here, for example in developing track and trace solutions, or smart farming. We see this as an opportunity to enter new markets. We see potential in offering service models rather than just selling a chemical product.
Shaping new material cycles
By new material cycles, we mean products that close the loop by being based on renewable or recycled raw materials or by enabling recyclability and/or biodegradability.
Circular feedstocks
We will continue to increase the volume of renewable and recycled feedstocks from sustainable sources which we already use as drop-in solution. We expect that 250,000 metric tons of feedstock will come from recycled sources by 2025. The certified mass balance approach enables us to offer products with an allocated share of renewable or recycled feedstock. Customers can choose these products if they want to contribute to saving fossil resources and a lower carbon footprint. We also offer a bio-based portfolio, e.g. for personal care, nutrition or plastics. By offering a portfolio based on renewable and recycled feedstock, we contribute to reaching our target of €22bn sales with Accelerator products in 2025.
We have set ourselves the target of using 250,000 tons of recyclate-based feedstock by 2025, thereby replacing fossil-based input. A significant contribution to this will come from our ChemCycling™ project, in which we manufacture high-performance products such as, for example, parts for the automotive industry, from feedstock derived from tires or mixed plastic waste on an industrial scale. In addition, sustainable bio-based feedstock will increasingly replace finite raw materials.
We also want to close direct recycling loops for the products we sell. Let’s take polyurethanes for foam mattresses or battery materials for electric cars. Chemical innovations will play a key role in enabling circularity for these products. Internally, we have set up a co-funding program to stimulate ideas within the business units. Here, we provide financial support and coaching to incubate new circular project ideas. So far, we have supported more than 20 global projects. Most of the circular business models are only feasible because of digital solutions such as tracking and tracing or optimizing complex logistics. Here, we work together with start-ups and value-chain partners and are always looking for new collaborations.
Discovering opportunities
A perfect example for partnerships is our “waste-2-chemicals” project in Nigeria. With great entrepreneurial spirit, colleagues are working with local NGOs in Lagos to collect mixed plastic waste, which is then thermochemically transformed into pyrolysis oil, a high-quality feedstock. It is a small project but with a big impact locally, because it offers income opportunities for the waste pickers and helps to keep plastic waste streams out of the environment.
For BASF, circular economy offers many opportunities, not only in closing direct loops but also by contributing to much more efficient resource use. These approaches can only work if we stop thinking in terms of “take-make-dispose,” and if we have the courage to try out new business models with many unknown variables. The circular economy is not just about technology, nor is it just about marketing or waste collection. More than anything, it is about changing mindsets. Worldwide, we have to find solutions that decouple growth from resource consumption. I think that the chemical industry, and BASF in particular, can lead the way in this transformation.