BASF in Greater China 2021
Energy efficiency and environmental protection
As an energy-intensive company, we are committed to energy efficiency and global climate protection. With our carbon management, we are trying to drastically minimize our own carbon footprint by utilizing sophisticated technologies and processes, constantly upgrading our facilities, and increasing our use of renewable energies. We make our manufacturing operations as energy efficient as possible with the help of comprehensive energy management. We are researching and developing completely new processes and technologies to reduce our greenhouse gas emissions over the long term.
In 2021, the total energy consumption at BASF sites in Greater China increased primarily due to higher production capacity and output. Electricity consumption totaled 1.015 million megawatt hours (MWh) in (2020: 0.845 million MWh). Steam supply totaled 3.076 million MWh (2020: 2.709 million MWh). Fossil and residual fuel use in power plants was higher than in 2020 (2021: 0.912 million MWh, 2020: 0.834million MWh).
.png)
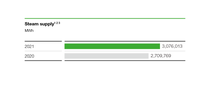.png)
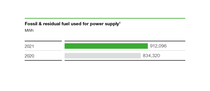.png)
1The comparative figure for 2020 has been restated in alignment with the Corporate Report consolidation rules and change of calculation method to GHG Protocol 5th Assessment Review instead of 4th in the 2020 report.
2Adjusted method for recognizing import/export of electricity and steam.
3Conversion factor: 0.75 MWh per metric ton of steam.
We are committed to achieving our carbon neutrality goals through improving energy efficiency. In 2021, many sites in Greater China continued their efforts to save energy. For example, one site in Nanjing reduced electricity usage by optimization of its chiller after adding electrical heat tracing to control oil separator temperature and optimizing operation to reduce energy consumption of the plant. By installing vapor line insulation, one site in Xinjiang was able to save steam. One site in Shanghai reduced material loss and avoided hundreds of tons of CO2 emissions by optimizing the sump temperature.
In addition to site-specific upgrades, we also collaborated with external partners to ensure broader environmental protection. Shanghai has seven facilities actively participating in a local pilot carbon emissions pricing plan (ETS). We also work closely with industry associations such as CPCIF and AICM to prepare for the national ETS and conducting dialogues with relevant authorities.
BASF had set a goal of introducing certified energy management systems (DIN EN ISO 50001) at all relevant production sites by 2020. Since 2016, several sites in Greater China have been ISO 50001 certified. All energy efficiency measures are recorded in a global database, and are available as best practices for all our sites worldwide.
BASF has set itself even more ambitious goals on its journey to climate neutrality. The company wants to reduce its greenhouse gas emissions worldwide by 25% by 2030 compared with 2018, and achieve net zero emissions by 2050. All BASF sites in Greater China have taken measures to contribute and help in achieving this ambitious goal.
In 2021, GHG emissions from BASF’s chemical operations in Greater China totaled 1.182 million metric tons, a decrease of 4.5% from the previous year (2020: 1.238 million), despite higher production in volume and an increase in newly acquired sites in 2021.
GHG emissions from a few sites were reduced even with higher production due to key initiatives such as increasing the use of renewable energy by joining the R-DPP pilot trade in China and building up photovoltaic power stations.
Besides GHG emissions, BASF measures emissions of other air pollutants, including inorganic compounds such as carbon monoxide (CO), sulfur oxides (SOx), nitrogen oxides (NOx) and ammonia, as well as dust or non-methane volatile organic compounds (NMVOC). In 2021, air pollutants from BASF’s operations in Greater China totaled 312 metric tons, an increase of 14% from 2020 (274 metric tons in 2020).
Several sites upgraded NMVOC treatment facilities in order to meet the increasingly stringent VOC emission standards in China. More sites in Shanghai, Jiangsu Chongqing and Guangdong province have installed online monitoring facilities and set internal alarms to avoid any potential emissions. Almost all sites with NMVOC emissions in Shanghai, Jiangsu, Chongqing, Guangdong and Xinjiang conducted Leak Detection and Repair (LDAR) programs for fugitive NMVOC. These measures will not only ensure BASF's full compliance with China's increasingly stringent emission rules while minimizing the impact on the environment.
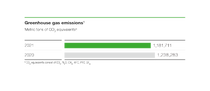

1The comparative figure for 2020 has been restated in alignment with the Corporate Report consolidation rules and change of calculation method to GHG Protocol 5th Assessment Review instead of 4th in the 2020 report.
Water is a scarce resource but is of fundamental importance in chemical production. It is used as a coolant, a solvent, and a cleaning agent, as well as in the manufacturing of our products. BASF is committed to its responsible use along the entire value chain, and especially in its production sites’ water catchment areas. We aim to use water as sparingly as possible and further reduce emissions into the water. We have set global goals for sustainable water management. BASF sites in Greater China follow the group requirements and local regulations. The European Water Stewardship (EWS) Project has been completed at twelve BASF sites in water-stressed parts of Greater China, with four more sites to be covered by 2030.
To minimize unforeseen emissions and the pollution of surface or groundwater, we have developed a water protection strategy for each production site, as a mandatory part of the global Responsible Care initiative, of which BASF is a member. The wastewater protection plans involve evaluating wastewater in terms of risk and drawing up suitable monitoring strategies. The result of the evaluation was audited to check if these measures were being implemented and followed.
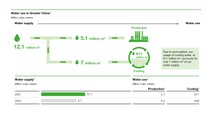.png)
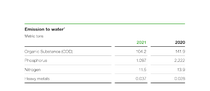
Wastewater risk assessment helps in the identification of potential risks from unanticipated wastewater releases. In 2021, one site in Shanghai optimized the transesterification unit, which significantly reduced the amount of wastewater production. Another site in Nanjing re-evaluated the steam condensate drainage system to reduce 4,000 tons of wastewater. A few sites in Shanghai have installed mass flow meters to optimize their process of water usage.
In 2021, emissions of water pollutants were decreased compared to 2020. Emissions of organic substances (COD) totaled 104.2 metric tons (2020: 141.9 metric tons). Phosphorus emissions were at 1.097 metric tons (2020: 2.222 metric tons). Nitrogen emissions were at 11.5 metric tons (2020: 13.9 metric tons), and heavy metals emissions increased to 0.037 metric tons (2020: 0.028 metric tons).
Due to higher production, and the launch of new sites and projects in Greater China, the total water supply in 2021 in Greater China was 12.1 million cubic meters, (2020: 9.7 million cubic meters). Among them, 5.1 million cubic meters were used in production in 2021 (2020: 4.3 million cubic meters), while the rest was predominantly used for cooling purposes. We reduce our water use by recirculating as much water as possible. The recirculated water used for cooling at BASF’s Greater China sites amounted to 611 million cubic meters in 2021 (2020: 609 million cubic meters).
BASF strives to create products and processes to avoid waste as much as possible. If waste cannot be avoided, we will try to explore options for recycling and energy recovery at BASF’s existing Verbund site. Waste from BASF’s chemical operations in Greater China in 2021 totaled 109,489.6 metric tons, an increase of 13.5% from last year (2020: 96,484.2 metric tons).
BASF continued to work on reducing waste and improving recycling. One of our sites in Xinjiang recovers the metal from spent catalysts rather than disposing it through landfill. In 2021, the total amount of waste recovered was at 79,598 metric tons, with an increase of 14% from the previous year (2020: 69,807 metric tons); while the total waste disposed was at 29,891 metric tons (2020: 26,677 metric tons).
Meanwhile, we regularly audit external waste management companies, ensuring that our hazardous waste is properly disposed of. This helps in preventing soil pollution by preventing today's trash from becoming tomorrow's contamination. We have closely monitored site soil and groundwater status in Greater China and documented the information in a global database since 2013.
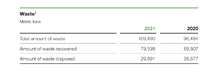
1The comparative figure for 2020 has been restated in alignment with the Corporate Report consolidation rules and change of calculation method to GHG Protocol 5th Assessment Review instead of 4th in the 2020 report.