Our research focus – we create chemistry for a sustainable future
Chemistry as a cross-sectional technology plays a key role in addressing future challenges, because innovations in the field of chemistry provide answers to exactly those questions that will concern humanity in the future: raw materials, environment and climate, food and nutrition, and quality of life. Trends in these areas drive our innovation process at BASF. They deliver impulses and determine the topics for which we pursue research and develop solutions.
Examples of current research projects
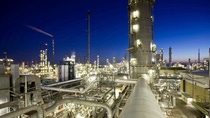
Carbon management: New technologies for clean high temperature reactions
Because energy is needed to perform chemical reactions, fossil fuels are the largest source of CO2 in the chemical industry. BASF’s steam crackers, for example, must reach a temperature of 850°C in order to break down naphtha into olefins and aromatics for further processing. If this energy could come from renewable electricity instead of the natural gas typically used now, CO2 emissions could be dramatically reduced by as much as 90%. BASF therefore aims to develop the world’s first electrical heating concept for steam crackers within the next five years. At the same time, material testing will be necessary to determine which metallic materials can withstand the high electrical currents and are suitable for use in this type of high-temperature reactor.
More about BASF’s commitment to energy and climate protection and BASF’s Carbon Management Program
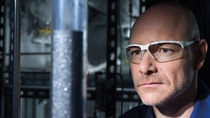
Carbon management: New process for clean hydrogen
- The production of hydrogen also releases significant volumes of CO2. The chemical industry uses large quantities of hydrogen as a reactant. At BASF, for instance, it is used in ammonia synthesis. Hydrogen will also be essential for many sustainable energy carrier and energy storage applications in the future. Together with cooperation partners, BASF is therefore developing a new process technology to produce hydrogen from natural gas. This technology splits natural gas directly into its components hydrogen and carbon. The resulting solid carbon can potentially be used in steel or aluminum production, for example. This methane pyrolysis process requires comparatively little energy. If this energy comes from renewable sources, hydrogen can be produced on an industrial scale without CO2 emissions.
More about BASF’s commitment to energy and climate protection and BASF’s Carbon Management Program
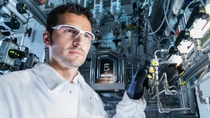
Carbon management: New catalysts for clean olefines
As a central, high-volume intermediate, olefins represent an especially important area where BASF is looking to develop new low-emission processes. The considerable CO2 emissions resulting from current production methods in the steam cracker could also be significantly reduced through “dry reforming” of methane. This process creates a syngas which is then transformed into olefins via an intermediate step of dimethyl ether. BASF researchers have now been able to find a way to do this for the first time thanks to new, high-performance catalyst systems. These new-generation catalysts are being marketed in cooperation with Linde. Depending on the availability of raw materials and renewable electricity, this innovative process could then be a complement or alternative to the potential electrical heating of steam crackers.
More about BASF’s commitment to energy and climate protection and BASF’s Carbon Management Program
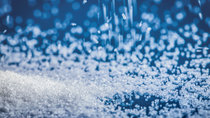
Carbon management: New chemistry for using CO2
BASF is also presenting a new approach for using CO2 as a chemical feedstock: the production of sodium acrylate from ethylene and CO2. Sodium acrylate is an important starting material for superabsorbents, which are widely used in diapers and other hygiene products. A few years ago, researchers at the BASF-supported Catalysis Research Laboratory (CaRLa) at the University of Heidelberg were able for the first time to successfully close the catalyst cycle for this reaction. In the meantime, BASF experts have made important progress in scaling up this process to industrial scale and have demonstrated that it can be successfully implemented at laboratory scale in a mini plant. Compared to the current propylene-based production method for superabsorbents, in the new process CO2 would replace around 30% of the fossil fuels, provided that a larger-scale process also proves to be stable and energetically favorable.
More about BASF’s commitment to energy and climate protection and BASF’s Carbon Management Program
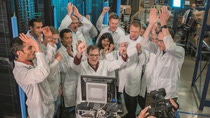
Virtual and real-life experiments complement each other
Digital technologies have a rapidly expanding influence on research and development. Managing large quantities of data has become a decisive factor for future scientific and economic success. With BASF’s digital approach, virtual modeling and computer simulation go hand in hand with physical experiments in the lab – they complement each other. Simulations help with the design of experiments and facilitate forecasting, while experiments deliver measurable results and evaluate the computer models. This results in a better understanding of chemical products and processes, and thus enables greater innovation to be achieved in a shorter period of time. A key element is the new
supercomputer which has been put into operation in October 2017 in Ludwigshafen. With 1.75 petaflops, it offers around 10 times the computing power that BASF currently has dedicated to scientific computing. In the ranking of the 500 largest computing systems in the world, the BASF supercomputer was number 65 on the June 2017 list.
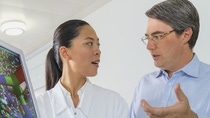
Digital technologies are indispensable for everyday R&D operations
Digitalization gives researchers additional opportunities to implement their creative ideas and to collaborate intensively with others around the world. In the view of BASF experts, it is essential to integrate digital technologies directly into the daily work of the R&D units. Direct access to knowledge-based systems is necessary to enable effective problem-solving and it opens up new horizons. A cloud-based app platform, for example, will make it considerably easier for all researchers to expand knowledge networks.
In recent months, successful projects by BASF researchers have already demonstrated the enormous potential that digitalization offers in research. For example, researchers were able for the first time to conduct a systematic investigation of the data on catalysts used in the production of the intermediate product ethylene oxide. The investigation found correlations between the formulations and the application properties of the catalysts, which enabled their performance and lifetime to be predicted more accurately and faster.
Another example are computer simulations of microencapsulation. It is used to protect active ingredients, for example from moisture and oxygen. Simulations help to better understand and predict the complex chemical and physical interactions within the microcapsule, allowing laboratory test series to be planned more precisely.
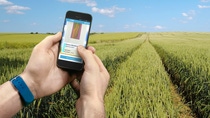
Agronomic models support farmers
BASF is also playing an important role in the digital transformation of agriculture, where it relies on internal and external cooperation. The online application Maglis® helps farmers use available information more efficiently and make better decisions regarding the cultivation of their fields. The firm ZedX, which BASF acquired at the end of May, specializes in developing agronomic models for weather, plant growth and infestation with diseases, weeds and pests. BASF and ZedX have already jointly developed a model that, based on weather and environmental conditions, identifies the right window of application for a BASF herbicide.
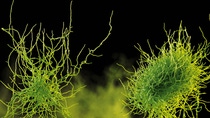
White biotechnology: thermostable enzyme for animal nutrition
BASF researchers from the research platform Bioscience Research have developed improved phytase (Natuphos®E) for animal nutrition. Phytase is an enzyme that helps animals to better digest the phosphate contained in plants. But many enzymes are heat-sensitive and can be destroyed by the high temperatures in the pelleting process used to make animal feed, thus rendering the enzymes ineffective. To develop an effective, thermostable phytase, BASF researchers examined numerous different phytases that exist in bacteria and then developed the best possible hybrid from these using biotechnological methods. This was then further improved and an appropriate production strain based on the fungus Aspergillus niger was developed for the fermentation (biotechnological production) of the enzyme. The new phytase has already been launched in some countries in Asia, South America as well as in the United States and is currently in the approval phase in other countries.
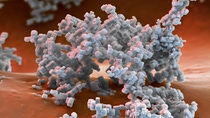
Catalyst: added value for exhaust gas cleaning and refineries
The research platform Process Research & Chemical Engineering works on specialty zeolites, such as BASF’s copper chabazite, which play a vital role in emission-control catalysts for diesel engines because they are especially efficient at removing nitrogen oxides from exhaust gas. Demand for modern catalyst systems for cars is growing steadily thanks to increasingly stringent emission regulations. To meet this demand, BASF researchers are continually working on developing the next generation of specialty zeolites. Using sophisticated raw materials and processes, they can adjust the size of the pores in order to make particles that are more consistent. BASF has also developed a boron-based catalyst technology (BoroCatTM) that enables refineries to increase yields of valuable products like gasoline, diesel and other fuels from crude oil. The nickel contained in crude oil presents a particular challenge to further processing, as it significantly increases the generation of undesirable by-products like petroleum coke and hydrogen. Containing an optimized pore structure, the new BoroCat Fluid Catalytic Cracking (FCC) catalyst intercepts nickel in processing, thus preventing undesirable chemical reactions.
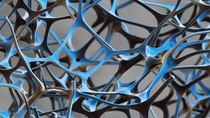
Plastics: successfully minimizing noises and vibrations
For the research platform Advanced Materials & Systems Research, the focus was on the topic “Noise, Vibration and Harshness.” BASF experts are investigating the possibilities of minimizing unwanted noise and vibrations by using material and component design. This is becoming increasingly important since both background noise levels and vibrations continue to grow as our home and work environments become more automated. At the same time, the noises are changing. In electromobility, for example, engine noise is quieter but other annoying frequencies become more prominent and need to be reduced. Another example is household appliances. With increasing urbanization, more and more people are living in confined spaces. Households not only have more electrical appliances, the equipment is getting more powerful. The resulting noise and vibration need to be minimized. An interdisciplinary BASF team comprising chemists, physicists and engineers is improving various polymer solutions that can be used to optimize frequencies in the range that can be felt and heard: from 1 to 20,000 Hertz. Depending on the frequency range and the requirements, the team is able to change the design of components and/or the molecular or foam structure of the materials used (polyamides, polyurethanes, melamine resin foams) with computer simulations.