Media
Building sustainably with concrete
BASF admixtures make concrete more flowable, more durable, stronger - and improve the eco-friendliness of concrete structures.
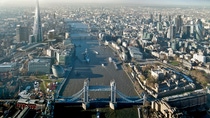
When laying the foundation, for example, these additives allowed an almost 5,500 cubic meter single concrete pour - a record in British construction history.
"The entire foundation slab was poured on a single weekend," explains Brian Williams, Southern Regional Sales Manager BASF Admixture Systems UK. "Because right in the middle of London, causing prolonged traffic snarl-ups with the construction vehicles was out of the question. To ensure that the densely packed steel reinforcement bars at the base of the slab were coated quickly and completely within this short time, the concrete had to be particularly flowable. Clearly a job for BASF's specially developed Glenium® SKY." One further advantage of the admixture: the concrete can be pumped to an altitude of 300 meters without problems.
Another major challenge was the immense amount of concrete needed to cast the foundation. Because concrete generates heat while setting - a lot of concrete means a lot of heat. And the hotter concrete becomes, the faster it sets. This can create a serious problem: if the first poured layers set too quickly, the following layers cannot bond with them properly. The resulting concrete is neither homogeneous nor stable enough. In "The Shard", the admixture Pozzolith® prevented the concrete from setting too soon, thereby ensuring high, homogeneous concrete quality.
This high concrete quality also ensures that the construction material can cope with the huge pressure generated by the enormous height of the tower. Thanks to Glenium admixtures, the concrete withstands a pressure equivalent to the weight of a small car resting on an area the size of a big toe. This outstanding strength ensures a long lifetime for the concrete structure and makes for sustainable building usage.
Glenium superplasticizers improve not only the structural properties of concrete, but also its eco-friendliness.
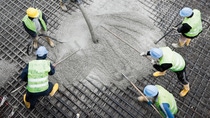
Because of its versatility, concrete is the most widely used man-made material. But it has one considerable disadvantage: it causes large amounts of climate damaging carbon dioxide (CO2). This is because concrete consists mainly of cement, which in turn contains cement clinker, a material fired at almost 1,500 degrees Celsius and whose production requires enormous amounts of energy. Cement clinker accounts for about six to seven percent of global carbon emissions.
Using BASF's concrete admixture Glenium, up to 50 percent of the cement clinker can be replaced with other materials. These materials include fly ash, a byproduct of coal-fueled electric power plants, or blast furnace slag obtained during steel production and recycled for these purposes. In this way, Glenium admixtures allow savings of up to 60 percent carbon in concrete production. In 2008, BASF's concrete admixtures already racked up savings of 22 million metric tons of carbon dioxide, equal to the emissions of the entire Berlin conurbation. Glenium admixtures also save energy, valuable raw materials and landfill space that would otherwise be needed to dump fly ash and blast furnace slag.
Glenium therefore contributes considerably to reducing carbon emissions in cement production. The industry has committed itself to this effort in a global sector agreement. In the USA and China, the emphasis is on modifying the composition of the cement, for example by including higher proportions of clinker substitutes. In Europe, the focus in producing standardized composite cements is more on improved energy efficiency and alternative fuels such as biomass and refuse incineration.
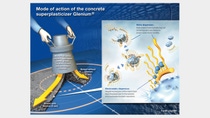
The Prospects
In Europe, the use of supplementary cementitious materials so far has only been possible when the suitability was established - unlike in the USA, where BASF has developed the concept of "Green Sense Concrete".
Andreas Tselebidis, BASF's concrete admixture expert, is enthusiastic about the concept: "This concrete consists partially of recycled material like fly ash and blast furnace slag, as well as specially formulated admixtures such as Glenium®. These materials make the innovative construction material much more eco-preferable than conventional concrete."
As a cradle-to-gate eco-efficiency analysis has shown, when compared to conventional concrete mixtures, Green Sense Concrete mixtures require 30 percent less energy, cause 37 percent less climate damaging carbon dioxide and consume 35 percent less raw materials. The water consumption is also much lower: the novel construction material needs five percent less water - representing a saving of 417 liters of water per single family house, roughly equivalent to three full bathtubs. Green Sense Concrete can also be produced economically. In this way, BASF is making an important contribution to sustainable construction.
Another initiative is the establishment of the American "Green Building" certification, known as LEED (Leadership in Energy and Environmental Design), a prestigious seal of quality awarded for outstanding achievements in sustainable construction and building management. The certification covers six aspects: environmental impact of construction and consumption of water, energy and resources, comfort and room quality. Points can be awarded in several categories for the use of BASF's Green Sense Concrete.
The Info Box
What is cement?
The main ingredients of cement are limestone and clay. These materials are mixed with quartz sand and iron ore, finely ground and dried. This raw mix is then fired (sintered as the experts say) at 1,450 degrees Celsius.
When it melts, it produces roundish particles measuring about three centimeters - known as cement clinker. This consists of chemical compounds which later cause the cement to set. These compounds include calcium silicates, calcium aluminates and calcium aluminum ferrites. Finally, the cement clinker is ground with gypsum or anhydrite to produce cement.
What is concrete?
Concrete consists mainly of cement, water and aggregate (sand, gravel and crushed rocks). The cement is the glue that holds everything together. When mixed with water, it sets to produce crystalline needles that firmly interlock with each other to produce a hard, rock-like material. The properties of the concrete, such as weight, varying strength levels, low shrinkage and cracking potential, corrosion resistance etc. can be varied as required by changing the mixing ratios and admixtures. Concrete can also be combined with steel as well as plastic or glass fibers, providing higher ductility and flexural properties.
How does a modern concrete superplasticizer work?
Modern superplasticizers like Glenium are based on synthetic organic polymers such as polycarboxylate ether (PCE). A PCE molecule consists of one long main chain and shorter side chains. The main chains of the PCE molecules are negatively charged. When mixed with fresh concrete, they are adsorbed onto the surfaces of the cement grains and other fine particles. The side chains of the molecules point outward like the spines of a chestnut burr and hold the particles at a distance to each other. This makes it easier for them to move against each other and the concrete becomes more fluid. Concrete can be given different properties by varying the length of the main and side chains of the admixtures.