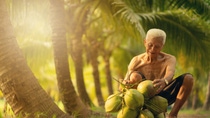
BASF’s Care Chemicals division publishes its Responsible Sourcing Report for 2024
Ludwigshafen, Germany, March 31, 2025 – BASF’s Care Chemicals operating division today released the third edition of its Responsible Sourcing Report (RSR). The report shows the division’s progress in 2024 in the three pillars of sustainability – economy, environment and society. At the same time, it underscores BASF’s commitment to sustainability, demonstrating the company’s dedication to supporting smallholder farmers and promoting sustainable practices. BASF’s comprehensive sustainability statement can be found in the company’s Annual Report 2024.