Factbook
Catalysts
BASF’s Catalysts division is the global market leader in catalyst technologies. The division develops and produces process catalysts and battery materials, and offers base metals sourcing, recycling and management services. It is also the home of BASF’s Environmental Catalyst and Metal Solutions (ECMS) standalone entity, comprising mobile emissions catalysts and precious metals trading, recycling, and related products and services. BASF expands its leading role in both catalysts and battery materials through continuous process and product innovation.
Sales by region 2023 (location of customer)
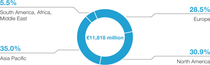
Sales by direct customer industry 20231
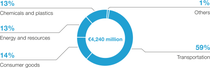
1 Excluding sales of €7,578 million in precious metal trading and precious metal sales in the automotive catalyst business
Portfolio
Battery base metals and precursor cathode active materials (PCAM)
This global business unit supports the battery materials business and its customers with services related to base metals sourcing and management. BASF also provides a variety of pricing and delivery arrangements to meet logistical, financial and price-risk management requirements. Moreover, BASF ensures a sustainable and reliable supply chain for metals used in PCAM, starting with the refining of metal ores. Our customized PCAM development ensures maximum CAM performance, for example, in terms of driving range, charging time and safety of the battery.
Battery recycling
In addition, BASF offers battery recycling solutions and services for its customers in the e-mobility value chain. Battery producers and electric vehicle manufacturers can choose from a range of individual services along the battery value chain. Moreover, BASF also offers end-to-end support for OEMs, ensuring a one-stop-shop experience to meet our customers’ battery recycling needs.
Cathode active materials (CAM)
BASF is a leading global supplier of advanced CAM for the lithium-ion batteries market, providing high-performance CAM to the world’s largest cell producers and for leading platforms of OEMs. BASF has a global presence with R&D and production capacity in all regions, in some cases leveraging partnerships. BASF is a frontrunner in developing innovative solutions and conducting next-generation battery materials research.
Environmental Catalyst and Metal Solutions (ECMS)
BASF Environmental Catalyst and Metal Solutions is a standalone entity within BASF Group. It comprises two business units – mobile emissions catalysts and precious metal services and recycling.
The mobile emissions catalysts unit enables cost-effective regulatory compliance, providing technologies that control emissions from gasoline and diesel-powered passenger cars, trucks, buses, off-road vehicles and motorcycles. The unit also offers technologies to improve indoor air quality and cabin air in airplanes.
The precious metal services and recycling unit has in-depth knowledge and vast experience in the field of metals management, offering industrial customers a full loop of services from precious metal supply and recycling to financial risk management. The unit also produces precious metal chemicals, temperature-sensing thermocouple and optical technologies, and is expanding its capabilities and footprint in PEM (proton exchange membrane) electrolyzer and fuel cell technologies to support customers.
Process catalysts
BASF is a leading global manufacturer of catalysts for the chemical industry, with solutions across the chemical value chain. The business comprises chemical catalysts and adsorbents, refinery catalysts and custom catalysts.
BASF’s market position and main competitors
The Catalysts division holds one of the top three market positions in all strategic business areas in which it is active.
The main competitors (alphabetical order) include Albemarle, Clariant, Easpring, Ecopro, Johnson Matthey, Umicore and W.R. Grace.
Focus of research and development
For battery materials, the focus is on offering a comprehensive product portfolio meeting customers’ requirements for e-mobility applications in all segments, including improving energy density to extend driving range as well as stability, safety and cost. For mobile emissions catalysts, the focus is on improved products to meet future vehicle emission standards. Precious metal services and recycling is developing next-generation electrocatalysts and catalyst coated membranes to improve performance and reduce cost for PEM electrolyzers and fuel cells. In the process catalysts business, priority is given to developing new and improved products that enable the chemical industry’s transformation to net-zero emissions.
Acquisitions/JVs/investments
From 2021 onward
Product group | Description | Year |
Battery materials | BASF and Shanshan formed joint venture (BASF 51%) for CAM and PCAM production in China | 2021 |
CAM capacity expansion for the joint venture BASF Shanshan in Chansha, China | 2023 | |
PCAM manufacturing plant in Harjavalta, Finland | – 1 | |
CAM manufacturing plant in Schwarzheide, Germany | 2023 | |
Battery recycling prototype plant in Schwarzheide, Germany | 2024 | |
CAM capacity expansion for the joint venture BASF TODA in Onoda, Japan | 2024 | |
Black mass recycling plant in Schwarzheide, Germany | 2024 | |
Mobile emissions catalysts | Capacity expansion in Chennai, India | 2022 |
Precious metal services | Acquisition of Zodiac Enterprises LLC assets in Caldwell, Texas, for catalyst recycling | 2021 |
Refinery capacity expansion in Seneca, South Carolina | 2022 | |
BASF HERAEUS (China) Metal Resource Co., Ltd. formed in Pinghu, China, for automotive catalyst recycling | 2022 | |
Acquisition of Arc Metal AB in Hofors, Sweden | 2024 | |
Process catalysts | Construction of global Catalyst Development and Solids Processing Center in Ludwigshafen, Germany | 2024 |
1 Startup date of the plant depends on the outcome of the ongoing permitting process.
Divestitures/shutdowns
From 2021 onward
Product group | Description | Year |
Process catalysts | Closure of the Erie, Pennsylvania, production site | 2021 |
Divestiture of De Meern, Netherlands, production site to IQatalyst B.V., Luxembourg | 2023 |
Innovation example

X3D™ technology improves performance and sustainability
The novel X3D™ technology enables the production of catalysts with optimal shape to achieve best performance and efficiency while reducing energy consumption. Catalysts produced with this technology feature an open structure, resulting in a reduction of the pressure drop across the reactor and a high surface area, significantly improving the catalysts’ performance. The technology offers a greater freedom of catalyst design compared to conventional production technologies. It brings catalysts’ performance to the next level and helps to customize catalysts to customers’ specific conditions and needs by designing infill patterns, fiber diameter and orientation. Customers can benefit from an increased reactor output, higher product quality and lower energy consumption, enabling significantly higher sustainability. The technology can be applied to a wide variety of existing catalytic materials, including base or precious metal catalysts as well as carrier materials. The novel catalysts are mechanically robust and proven in several commercial plant operations.