Sustainability
Our Carbon Management

We want to live up to our responsibility for climate protection. One way we do this is with our products, which enable our customers to lower CO2 emissions. But that is not all: We also become more efficient in our production and energy use, we will increase our use of renewable energies and we will accelerate the development and deployment of new CO2-free processes for the production of chemicals.
How can we create a more climate-friendly chemical industry?
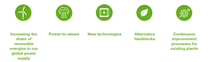
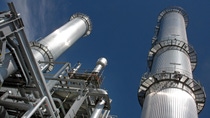
In recent decades, we have already significantly reduced our CO2 emissions by optimizing energy generation and production processes and systematically reducing nitrous oxide emissions. These continuous improvements will remain an important lever on the way to climate neutrality in the future.
In our production, we are increasingly using renewable and recycled raw materials to replace fossil raw materials.
Steam is one of the most important energy sources in the chemical industry. We use it to dry our products or to heat reactors. When steam is generated from fossil fuels, CO2 is produced. In future, we want to generate steam electrically and avoid these emissions.
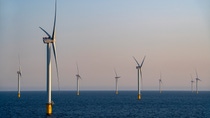
In order to be able to reduce greenhouse gas emissions on a large scale, the focus is on switching to renewable energy sources. This is because when new technologies are used, fossil fuels such as natural gas will be replaced by electricity from renewable sources in the future.
BASF is developing several promising technologies for reducing CO2 emissions in the chemical industry. These include the electrically heated steam cracker furnace and the CO2-free production of hydrogen. If it is not possible to produce CO2-free, we also want to examine the use of storage processes for CO2.
BASF is setting itself an ambitious goal of net zero by 2050 because we are convinced of the long-term strategic necessity and technical feasibility. Nevertheless, most new technologies are not yet competitive under the current conditions. Since the replacement of existing highly efficient production processes by new plants is very capital-intensive, BASF is working on German and European funding programs such as the IPCEI (Import Project of Common European Interest).
In addition, we work with numerous partners from universities, research institutes and companies on sustainable solutions for a carbon neutral future. We are convinced that the challenges of climate change can only be mastered together with our partners.
News board
Find out more about: