BASF Antwerp
Production Verbund
The BASF Antwerpen site includes about fifty production facilities. Some of these are integrated to a high degree. This is what we call our 'production Verbund'.
All production steps, from raw material to final product, are close together. By-products from one process are used as the raw materials for another. Installations are connected through an ingenious system of pipelines.
The advantages?
- Less transport required
- By-products are utilized in another process
- Reduced impact on the environment
- Knowledge-sharing platform
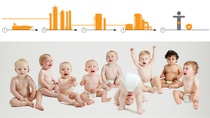
From nafta to diaper: a fine example of our production verbund
Step 1
Nafta, an oil derivative from petroleum refineries, is delivered as a raw material with a seagoing ship or international pipelines.
Step 2
Our largest facility, the steamcracker, breaks down this raw material into the basic building blocks of the chemical industry such as ethylene, propylene and benzene.
Step 3
The propylene fraction is conveyed through a pipeline to our acrylic acid facility and is converted into acrylates there.
Step 4
Once again a pipeline conveys the "pure" acrylic acid, this time to the superabsorber facility where it reacts with sodium hydroxide, thus polymerising into ultrafine granules.
Step 5
One characteristic of these granules is that they can absorb many times their own weight in water. This is the active substance that our customers incorporate into their diapers, for instance.