Sustainability
Innovative automotive drive system: Ultramid® components from BASF for fuel cells
March 11, 2019
Which automotive drive system will become dominant in future? How can we achieve further reductions in energy consumption and emissions through new and improved powertrain concepts for cars? These and other questions are occupying the minds not only of car manufacturers but also of BASF, as the biggest chemical supplier to the automotive industry.
Alongside the continued development of cars with more efficient internal combustion engines, chemistry is making an important contribution to a number of different electric drive concepts. Further progress is also being made in the field of fuel cells. In close cooperation with Joma-Polytec and Mercedes-Benz Fuel Cell, a subsidiary of Daimler AG, the engineering plastic Ultramid has successfully been used to manufacture a number of fuel cell system components. This innovative solution is being used as standard in the new Mercedes GLC F-CELL, which combines a fuel cell with a rechargeable lithium-ion battery.
Plastics increase efficiency – not only in hybrid, plug-in and electric vehicles but also in internal combustion engines. “Our extensive plastics portfolio offers all sorts of advantages which help us to satisfy specific customer requirements, depending on the drive concept and the specific component,” explains Andreas Stockheim, Segment Manager Powertrain and Chassis at BASF. “By continually developing new products in close collaboration with our customers, we are also able to adapt our portfolio to trends and changes in the market.”
Rating: particularly challenging
The high quality and safety requirements in the automotive industry place huge demands on materials. With versatile and sophisticated polyamides (Ultramid), polybutylene terephthalates (Ultradur®), polyphthalamides (PPA), and the plastics polyoxymethylene (Ultraform®) and polyethersulfone (Ultrason®), BASF is able to keep pace with car manufacturers’ latest developments, while also setting innovative trends. Technical properties and high functionality are key here. For the Mercedes GLC F-Cell, it is the all-round excellence of Ultramid’s properties that counts: good thermal and chemical resistance, dynamic stiffness, impact strength, and good long-term performance.
“Earlier tests with other materials revealed mechanical problems, so Daimler had very specific requirements for the material,” explains Stefan Milimonka, Key Account Manager in BASF’s Performance Materials division. “Our expertise with plastic automotive components and the extensive choice of existing products meant that we were able to work out possible solutions with our partners and identify the right material. It shows that with specialist knowledge and good cooperation between everyone involved, a complex project like this can be brought to a successful conclusion.”
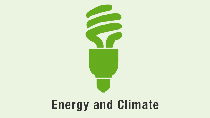
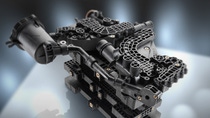
Three partners – one tailor-made solution
In conjunction with Joma-Polytec GmbH and Mercedes-Benz Fuel Cell GmbH, a subsidiary of Daimler AG, a development project was initiated. Its aim: to find an optimal solution satisfying the extensive range of requirements including thermal stability, media resistance, and durability. In view of the unique material structure, and on the basis of intensive material analyses of the chemical and mechanical resistance, the partners ultimately decided on the tailor-made Ultramid grades A3WG10 CR and A3EG7 EQ. Following successful testing of all components, the two glass fiber-reinforced Ultramid grades are now being used as standard to manufacture the anode- and cathode-end plate in fuel cells. Ultramid A3EG7 EQ is an ideal material, given the exceptional purity requirements associated with sensitive applications in the electronics industry. In the case of the media distribution plate and the water separator unit, which is exposed to a wide variety of media through the cooling water, air and hydrogen channel, this Ultramid grade offers excellent resistance, while at the same time meeting all requirements regarding the purity of the material.
“Thanks to BASF’s extensive product portfolio and the specialist knowledge of all the parties involved, we have taken an important step forward in the serial development of fuel cells,” is how Stefan Heinz, deputy head of plastics technology development at Joma-Polytec GmbH, sums up the project. “We worked together to analyze the stringent requirements and were able to put in place a highly efficient solution.”